Robot-Ready Gripper Compensation Devices
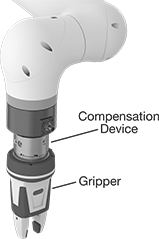
Ready to mount between your robot arm and gripper, these devices have standard ISO mounting hole patterns and allow grippers to adjust, so they can grab parts that are misaligned or have different tolerances. They also compensate when aligning parts during placement, which increases efficiency and reliability in your process, while protecting parts and robots from wear. Use them to avoid jams and keep automated assembly, bin picking, and machine tending jobs running smoothly. If you don't see your robot model number listed, measure the bolt circle diameter to determine mounting compatibility.
For technical drawings and 3-D models, click on a part number.
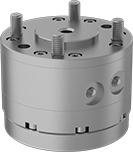
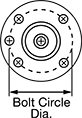
Devices for X and Y axes tilt grippers and move them side-to-side to make angled and horizontal adjustments. Use them to help grippers grab items on an incline and center items, such as a pin, above a hole.
Devices with spring actuation and spring reset use compression springs to position your grippers. Use the set screws to adjust the force of the springs.
End of Robot Arm | Gripper | |||||
---|---|---|---|---|---|---|
Resetting Force Range | Bolt Circle Dia. (Mount. Hole Pattern Compatibilty) | Mount. Fasteners Included | Mount. Fasteners Included | For Robot Arm Manufacturer (Series/Model Number) | Each | |
Anodized Aluminum Housing—Spring Actuation and Spring Reset | ||||||
±1.5 mm Horizontal Compensation | ||||||
0.34-0.79 lbs. / 0.15-0.36 kgf | 31.5 mm (ISO 31.5) | Yes | No | ABB (IRB 120; IRB 1200) FANUC (CR 4iA, 7iA; LR Mate 200iD/7L) KUKA Robotics (KR 10 R1100-2) Precise Automation (PAVP6; PF3400) Yaskawa/Motoman (GP 7, 8; MH 3BM, 3F, 5LS II, 5S II; MPP 3H, 3S) | 00000000 | 000000000 |
0.9-1.3 lbs. / 0.41-0.56 kgf | 31.5 mm (ISO 31.5) | Yes | No | ABB (IRB 120; IRB 1200) FANUC (CR 4iA, 7iA; LR Mate 200iD/7L) KUKA Robotics (KR 10 R1100-2) Precise Automation (PAVP6; PF3400) Yaskawa/Motoman (GP 7, 8; MH 3BM, 3F, 5LS II, 5S II; MPP 3H, 3S) | 00000000 | 00000000 |
1.3-1.5 lbs. / 0.56-0.71 kgf | 31.5 mm (ISO 31.5) | Yes | No | ABB (IRB 120; IRB 1200) FANUC (CR 4iA, 7iA; LR Mate 200iD/7L) KUKA Robotics (KR 10 R1100-2) Precise Automation (PAVP6; PF3400) Yaskawa/Motoman (GP 7, 8; MH 3BM, 3F, 5LS II, 5S II; MPP 3H, 3S) | 00000000 | 00000000 |
±2 mm Horizontal Compensation | ||||||
0.67-1.1 lbs. / 0.31-0.51 kgf | 40 mm (ISO 40) | Yes | No | ABB (IRB 360 6/1600, 8/1130; IRB 140; IRB 1410; IRB 1600) FANUC (M-20 iA) Precise Automation (PP100) | 00000000 | 00000000 |
0.9-1.5 lbs. / 0.41-0.71 kgf | 40 mm (ISO 40) | Yes | No | ABB (IRB 360 6/1600, 8/1130; IRB 140; IRB 1410; IRB 1600) FANUC (M-20 iA) Precise Automation (PP100) | 00000000 | 00000000 |
1-2 lbs. / 0.46-0.92 kgf | 40 mm (ISO 40) | Yes | No | ABB (IRB 360 6/1600, 8/1130; IRB 140; IRB 1410; IRB 1600) FANUC (M-20 iA) Precise Automation (PP100) | 00000000 | 00000000 |
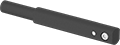
Sensors detect gripper positions by responding to magnets in the compensation devices. They signal whether the grippers are open or closed, and use that information to trigger other actions in your system. Two sensors are required for each device. Select sensors that match the electrical connections on your robot arm. PNP sensors communicate gripper positions with a positive signal, while NPN send a negative signal.
Electrical Connection Type | Plug Type | Number of Wire Leads | Switch Starting Position | Current | Voltage | Cord Length, ft. | Number of Sensing Positions | Each | |
PNP | |||||||||
---|---|---|---|---|---|---|---|---|---|
Hardwire | __ | 4 | 1 Off (Normally Open) and 1 On (Normally Closed) | 100 mA | 24V DC | 2 | 2 | 00000000 | 0000000 |
Plug | 4-Pin M8 | __ | 1 Off (Normally Open) and 1 On (Normally Closed) | 100 mA | 24V DC | 6 1/2 | 2 | 00000000 | 000000 |