Robot-Ready Electric Grippers
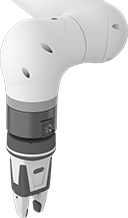
Gripper Fingers and
Robot Arm (Not Included)
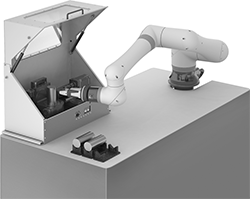
Including a robot tool mount and electrical connectors, these grippers come ready to attach to robot arms with standard ISO mounting hole patterns. Good for areas without compressed air, they use electricity to pick and place items in packaging, assembly, and machine-tending applications. All have a servomotor that opens and closes the grippers with equal force to grasp and release items from the inside or outside. Install the included software directly into your controller or teach pendant to program your gripper.
Select grippers that match your arm’s manufacturer series and model number or that are compatible with your electrical connection and signal output. Grippers with PNP signal output communicate proximity with a positive signal, while those with NPN signal output send a negative signal.
Grippers for FANUC CRX arms are FANUC approved, and grippers for Universal Robots (UR) arms are UR+ certified, so they've been tested to work seamlessly.
Warning: Never use to lift people or items over people.
For technical drawings and 3-D models, click on a part number.
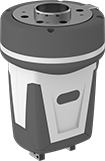
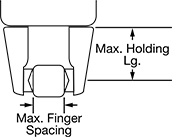
Discrete I/O grippers have four set gripping forces to move items—use a screwdriver to select the force you’ll need. Since these grippers open and close at the same force and stroke with every cycle, they’re good for picking items of a similar size and material. A discrete I/O signal and included inductive proximity sensor send information about an item’s location to your robot arm. All of these grippers are suitable for use in clean rooms rated to ISO Class 5. They’re also rated IP30 to prevent objects greater than 2.5 mm, such as a screwdriver, from making contact with live circuits.
ISO/TS 15066 grippers help you meet international safety standards. They don’t have pinch points or sharp edges, so you can use them on robots that will be near people.
Grippers with an LED status ring have three programmable colors to show if the gripper picked or released an item, or failed.
O'all | ||||||||||||||
---|---|---|---|---|---|---|---|---|---|---|---|---|---|---|
For Robot Arm Manufacturer (Series/Model No.) | External / Internal Gripping Force | Max. Gripping Cap. | Cycles per Sec. | Stroke Wd., mm | Max. Finger Spacing, mm | Max. Holding Lg., mm | Wt. | Mounting Hole Pattern Compatibility | Lg., mm | Wd., mm | Dp., mm | Manufacturer (Series/Model No.) | Each | |
ISO/TS 15066 Nylon Plastic Housing and Steel Jaws | ||||||||||||||
NPN Signal Output and M8 Plug, 24V DC | ||||||||||||||
Techman (TM 5, 12, 14) Omron (TM 5, 12, 14, 16, 20) | 7.5 lbs. 15 lbs. 22.5 lbs. 30 lbs. | 1.5 lbs. / 0.7 kg | 2 | 6 | 28 | 50 | 1.3 lbs. / 0.59 kg | ISO 50 | 126 | 93 | 90 | Schunk (Co-act EGP-C 40) | 0000000 | 000000000 |
NPN Signal Output and Wire Leads, 24V DC—With LED Status Ring | ||||||||||||||
Techman (TM 5, 12, 14) Omron (TM 5, 12, 14, 16, 20) | 7.5 lbs. 15 lbs. 22.5 lbs. 30 lbs. | 1.5 lbs. / 0.7 kg | 2 | 6 | 28 | 70 | 1.8 lbs. / 0.86 kg | ISO 50 | 126 | 93 | 90 | Schunk (Co-act EGP-C 40) | 0000000 | 00000000 |
Techman (TM 5, 12, 14) Omron (TM 5, 12, 14, 16, 20) | 12.5 lbs. 25 lbs. 37.5 lbs. 50 lbs. | 2.4 lbs. / 1.1 kg | 1 | 10 | 44 | 80 | 3 lbs. / 1.38 kg | ISO 50 | 152 | 125 | 86 | Schunk (Co-act EGP-C 64) | 0000000 | 00000000 |
PNP Signal Output and M8 Plug, 24V DC | ||||||||||||||
Doosan (M0609, M0617, M1013, M1509) Omron (TM 5, 12, 14, 16, 20) | 7.5 lbs. 15 lbs. 22.5 lbs. 30 lbs. | 1.5 lbs. / 0.7 kg | 2 | 6 | 28 | 50 | 1.3 lbs. / 0.59 kg | ISO 50 | 118 | 93 | 90 | Schunk (Co-act EGP-C 40) | 0000000 | 00000000 |
FANUC (CRX 5iA, 10iA, 10iA/L, 20iA/L, 25iA) Omron (TM 5, 12, 14, 16, 20) | 7.5 lbs. 15 lbs. 22.5 lbs. 30 lbs. | 1.5 lbs. / 0.7 kg | 2.5 | 6 | 28 | 50 | 1.3 lbs. / 0.59 kg | ISO 50 | 118 | 93 | 90 | Schunk (Co-act EGP-C 40) | 0000000 | 00000000 |
FANUC (CRX 5iA, 10iA, 10iA/L, 20iA/L, 25iA) Omron (TM 5, 12, 14, 16, 20) | 12.5 lbs. 25 lbs. 37.5 lbs. 50 lbs. | 2.4 lbs. / 1.1 kg | 1 | 10 | 44 | 80 | 2.2 lbs. / 1.11 kg | ISO 50 | 144 | 125 | 86 | Schunk (Co-act EGP-C 64) | 0000000 | 00000000 |
Omron (TM 5, 12, 14, 16, 20) Universal Robots (UR3, UR3e, UR5, UR5e, UR10, UR10e, UR16, UR16e) | 7.5 lbs. 15 lbs. 22.5 lbs. 30 lbs. | 1.5 lbs. / 0.7 kg | 2 | 6 | 28 | 50 | 1.3 lbs. / 0.59 kg | ISO 50 | 118 | 93 | 90 | Schunk (Co-act EGP-C 40) | 0000000 | 00000000 |
PNP Signal Output and Wire Leads, 24V DC—With LED Status Ring | ||||||||||||||
FANUC (CR 7iA) Omron (TM 5, 12, 14, 16, 20) | 7.5 lbs. 15 lbs. 22.5 lbs. 30 lbs. | 1.5 lbs. / 0.7 kg | 2 | 6 | 28 | 50 | 1.4 lbs. / 0.66 kg | ISO 31.5 | 118 | 93 | 90 | Schunk (Co-act EGP-C 40) | 0000000 | 00000000 |
FANUC (CR 7iA) Omron (TM 5, 12, 14, 16, 20) | 12.5 lbs. 25 lbs. 37.5 lbs. 50 lbs. | 2.4 lbs. / 1.1 kg | 1 | 10 | 44 | 80 | 3 lbs. / 1.38 kg | ISO 31.5 | 144 | 125 | 86 | Schunk (Co-act EGP-C 64) | 0000000 | 00000000 |
Omron (TM 5, 12, 14, 16, 20) Universal Robots (UR3, UR3e, UR5, UR5e, UR10, UR10e, UR16, UR16e) | 7.5 lbs. 15 lbs. 22.5 lbs. 30 lbs. | 1.5 lbs. / 0.7 kg | 2 | 6 | 28 | 50 | 1.8 lbs. / 0.86 kg | ISO 50 | 118 | 93 | 90 | Schunk (Co-act EGP-C 40) | 0000000 | 00000000 |
Omron (TM 5, 12, 14, 16, 20) Universal Robots (UR3, UR3e, UR5, UR5e, UR10, UR10e, UR16, UR16e) | 14 lbs. 25.5 lbs. 38.5 lbs. 51 lbs. | 2.2 lbs. / 1 kg | 2 | 10 | 44 | 64 | 2.6 lbs. / 1.22 kg | ISO 50 | 144 | 125 | 86 | Schunk (Co-act EGP-C 64) | 0000000 | 00000000 |
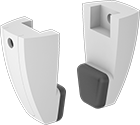
Simply connect these fingers to your Schunk gripper and start moving items. Made of lightweight but also strong nylon, all have rubber gripping pads to protect items from damage.
Warning: Never use to lift people or items over people.
Width, mm | Finger | For Gripper Jaw | ||||||||
---|---|---|---|---|---|---|---|---|---|---|
For Manufacturer (Series/Model No.) | Min. | Max. | Lg., mm | Wd., mm | Dp., mm | Wd., mm | Dp., mm | Mounting Hardware Included | Pair | |
Nylon Plastic | ||||||||||
Schunk (Co-act EGP-C, EGP 40) | 0 | 12 | 50 | 25.5 | 30 | 6 | 16 | Yes | 0000000 | 0000000 |
Schunk (Co-act EGP-C, EGP 40) | 12 | 24 | 50 | 19.5 | 30 | 6 | 16 | Yes | 0000000 | 000000 |
Schunk (Co-act EGP-C, EGP 64) | 0 | 20 | 80 | 39 | 36.9 | 10 | 20 | Yes | 000000 | 000000 |
Schunk (Co-act EGP-C, EGP 64) | 20 | 40 | 80 | 29 | 34 | 10 | 20 | Yes | 0000000 | 000000 |
Electric-Powered Grippers
Unlike air-powered grippers, which leak air, these electric grippers won’t release dirt or particulates, making them good for pick-and-place assembly, packaging, and finishing jobs in labs, electronics plants, and other clean environments. All have a servomotor that opens and closes the grippers with equal force to grasp and release items from the inside or outside. A discrete I/O signal actuates the grippers with a set gripping force—use a screwdriver to select the force you’ll need. Since these grippers open and close at the same force and stroke with every cycle, they’re good for picking items of a similar size and material.
To determine if gripper fingers are open or closed, and use that information to trigger other actions, add a sensor. All of these grippers are compatible with PNP and NPN signal outputs, which means they can communicate proximity with a positive or negative signal.
Warning: Never use to lift people or items over people.
For technical drawings and 3-D models, click on a part number.
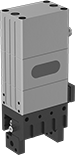
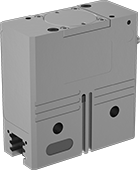

IP30 grippers prevent objects greater than 2.5 mm, such as a screwdriver, from making contact with live circuits. Suitable for use in clean rooms, they are also rated to ISO Class 5. They have one M8 4-pin connection, which brings power to the gripper and two digital input signals to the grippers' controller. All are compatible with optional inductive sensors.
IP40 grippers prevent objects greater than 1 mm, such as a wire, from making contact with live circuits. They have two M8 4-pin connections—one that brings power to the gripper and two digital input signals to the grippers' controller, and another that signals the position of your fingers back to the controller. All are compatible with optional magnetic sensors.
IP64 grippers are dust-tight and protected from water splashing in all directions. They have two M8 4-pin connections—one that brings power to the gripper and two digital input signals to the grippers' controller, and another that signals the position of your fingers back to the controller. All are compatible with optional magnetic sensors.
O'all | |||||||||||||||
---|---|---|---|---|---|---|---|---|---|---|---|---|---|---|---|
External / Internal Gripping Force | Max. Gripping Cap. | Cycles per Second | Stroke Wd., mm | Grip Opening / Closing Time | Max. Finger Spacing, mm | Max. Holding Lg., mm | Wt. | Lg., mm | Wd., mm | Dp., mm | Voltage | Mounting Hardware Included | Manufacturer (Series/Model No.) | Each | |
Aluminum Housing and Steel Jaws | |||||||||||||||
IP30 Rated | |||||||||||||||
4.5 lbs. 9 lbs. | 0.44 lbs. / 0.2 kg | 5 | 6 | 90 ms | 17 | 32 | 0.24 lbs. / 0.11 kg | 72.7 | 26.5 | 18 | 24V DC | No | Schunk (EGP 25) | 0000000 | 000000000 |
7.5 lbs. 15 lbs. 22.5 lbs. 30 lbs. | 1.5 lbs. / 0.7 kg | 2 | 12 | 200 ms | 28 | 50 | 0.7 lbs. / 0.32 kg | 88.4 | 40 | 26 | 24V DC | No | Schunk (EGP 40) | 0000000 | 00000000 |
12 lbs. 24 lbs. 36 lbs. 48 lbs. | 2.2 lbs. / 1 kg | 2 | 16 | 210 ms | 34 | 64 | 1.1 lbs. / 0.5 kg | 104.4 | 50 | 30 | 24V DC | No | Schunk (EGP 50) | 0000000 | 00000000 |
16 lbs. 32 lbs. 48 lbs. 64 lbs. | 2.6 lbs. / 1.2 kg | 1 | 20 | 490 ms | 44 | 80 | 1.7 lbs. / 0.8 kg | 114.7 | 64 | 35 | 24V DC | No | Schunk (EGP 64) | 0000000 | 00000000 |
IP40 Rated | |||||||||||||||
29 lbs. 58 lbs. 87 lbs. 116 lbs. | 6.1 lbs. / 2.8 kg | 1 | 16 | 260 ms | 27 | 125 | 2.2 lbs. / 1 kg | 103 | 96 | 42 | 24V DC | No | Schunk (PGN+E 80) | 0000000 | 00000000 |
45 lbs. 90 lbs. 135 lbs. 180 lbs. | 8.8 lbs. / 4 kg | 1 | 20 | 290 ms | 34.5 | 160 | 3.7 lbs. / 1.7 kg | 123 | 120 | 50 | 24V DC | No | Schunk (PGN+E 100) | 0000000 | 00000000 |
IP64 Rated | |||||||||||||||
29 lbs. 58 lbs. 87 lbs. 116 lbs. | 6.1 lbs. / 2.8 kg | 1 | 16 | 260 ms | 27 | 125 | 2.4 lbs. / 1.1 kg | 103 | 96 | 42 | 24V DC | No | Schunk (PGN+E 80) | 0000000 | 00000000 |
45 lbs. 90 lbs. 135 lbs. 180 lbs. | 8.8 lbs. / 4 kg | 1 | 20 | 290 ms | 34.5 | 160 | 3.9 lbs. / 1.8 kg | 123 | 120 | 50 | 24V DC | No | Schunk (PGN+E 100) | 0000000 | 00000000 |
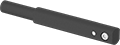
Optional sensors signal when gripper fingers are either open or closed, and use that information to trigger other actions in your system. Magnetic sensors detect finger position by responding to magnets placed on the motor of electric-powered grippers. Use them with IP40 and IP64 grippers. Those with programmable two-position detection send a signal when fingers open and close, letting you trigger actions in your system based on both signals. Inductive sensors respond to a metallic flag on the gripper. They are not, however, the best choice for machining applications since metallic debris can accidentally trigger them. Use these sensors with IP30 grippers.
Sensors with a plug connection work with the input/output on robot tool mounts with a power/signal block. Sensors with a hardwire connection have wire leads you either wire to a plug or to a power source.
PNP sensors communicate proximity with a positive signal, while NPN send a negative signal.
Signal Output Type | Number of Sensing Positions | Number of Wire Leads | Current, mA | Voltage | Switch Starting Position | Cord Lg., ft. | Each | |
Magnetic Sensors for IP40 and IP64 Grippers | ||||||||
---|---|---|---|---|---|---|---|---|
3-Pin M8 Plug | ||||||||
NPN | 1 | __ | 50 | 24V DC | 1 Off (Normally Open) | 1 | 00000000 | 0000000 |
PNP | 1 | __ | 50 | 24V DC | 1 Off (Normally Open) | 1 | 0000000 | 000000 |
4-Pin M8 Plug | ||||||||
PNP | 2 | __ | 100 | 24V DC | 1 Off (Normally Open) and 1 On (Normally Closed) | 6 1/2 | 00000000 | 000000 |
Hardwire | ||||||||
NPN | 1 | 3 | 50 | 24V DC | 1 Off (Normally Open) | 6 1/2 | 00000000 | 000000 |
PNP | 1 | 3 | 50 | 24V DC | 1 Off (Normally Open) | 6 1/2 | 00000000 | 000000 |
PNP | 2 | 4 | 100 | 24V DC | 1 Off (Normally Open) and 1 On (Normally Closed) | 2 | 00000000 | 000000 |
Inductive Sensors for IP30 Grippers | ||||||||
3-Pin M8 Plug | ||||||||
PNP | 1 | __ | 200 | 24V DC | 1 Off (Normally Open) | 1 | 00000000 | 000000 |
PNP | 1 | __ | 200 | 24V DC | 1 On (Normally Closed) | 1 | 00000000 | 000000 |
Hardwire | ||||||||
PNP | 1 | 3 | 200 | 24V DC | 1 Off (Normally Open) | 6 1/2 | 00000000 | 000000 |
PNP | 1 | 3 | 200 | 24V DC | 1 On (Normally Closed) | 6 1/2 | 00000000 | 000000 |
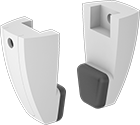
Connect fingers to your gripper and start moving items. Made of lightweight but also strong nylon, all have rubber gripping pads to protect items from damage.
Width, mm | Finger | For Gripper Jaw | ||||||||
---|---|---|---|---|---|---|---|---|---|---|
For Manufacturer (Series/Model No.) | Min. | Max. | Lg., mm | Wd., mm | Dp., mm | Wd., mm | Dp., mm | Mounting Hardware Included | Pair | |
Nylon Plastic | ||||||||||
Schunk (Co-act EGP-C, EGP 40) | 0 | 12 | 50 | 25.5 | 30 | 6 | 16 | Yes | 0000000 | 0000000 |
Schunk (Co-act EGP-C, EGP 40) | 12 | 24 | 50 | 19.5 | 30 | 6 | 16 | Yes | 0000000 | 000000 |
Schunk (Co-act EGP-C, EGP 64) | 0 | 20 | 80 | 39 | 36.9 | 10 | 20 | Yes | 000000 | 000000 |
Schunk (Co-act EGP-C, EGP 64) | 20 | 40 | 80 | 29 | 34 | 10 | 20 | Yes | 0000000 | 000000 |
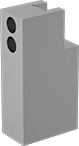
Finger blanks come ready to mount, so you can make custom fingers without starting from scratch. Just machine the blank’s gripping end to create fingers that will securely grip your specific parts.
When used in pairs, individual blanks have a symmetrical design that’s suitable for most applications.
Aluminum blanks are lightweight and resist rusting in wet environments. They’re softer than steel blanks, making them easier to machine and less likely to scratch your parts.
Steel blanks are stronger and more durable than aluminum blanks, so they’re less likely to break if they hit a nearby object. You can harden them for even more strength and durability.
For Gripper Jaw | Overall | |||||||
---|---|---|---|---|---|---|---|---|
For Manufacturer (Series/Model No.) | Wd., mm | Dp., mm | Lg., mm | Wd., mm | Dp., mm | Mounting Hardware Included | Each | |
Aluminum | ||||||||
Schunk (JGP, JGZ, PGN+, PGN+E, PGN+P, PZN+, JGP-P 80) | 26 | 15 | 80 | 41 | 22 | Yes | 00000000 | 000000 |
Schunk (JGP, JGZ, PGN+, PGN+E, PGN+P, PZN+, JGP-P 100) | 33 | 18.5 | 100 | 52 | 30 | Yes | 00000000 | 000000 |
Schunk (EGP 40) | 6 | 16 | 55 | 29 | 22 | Yes | 00000000 | 00000 |
Steel | ||||||||
Schunk (JGP, JGZ, PGN+, PGN+E, PGN+P, PZN+, JGP-P 80) | 26 | 15 | 80 | 41 | 22 | Yes | 00000000 | 000000 |
Schunk (JGP, JGZ, PGN+, PGN+E, PGN+P, PZN+, JGP-P 100) | 33 | 18.5 | 100 | 52 | 30 | Yes | 00000000 | 000000 |
Schunk (EGP 40) | 6 | 16 | 55 | 29 | 16 | Yes | 00000000 | 000000 |
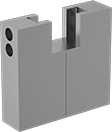
Finger blanks come ready to mount, so you can make custom fingers without starting from scratch. Just machine the blank’s gripping end to create fingers that will securely grip your specific parts.
Uncut pair blanks can be cut off center, making them good for applications where symmetrical fingers may hit nearby objects, such as when moving around machine spindles and parts trays during machine tending.
Aluminum blanks are lightweight and resist rusting in wet environments. They’re softer than steel blanks, making them easier to machine and less likely to scratch your parts.
For Gripper Jaw | Overall | |||||||
---|---|---|---|---|---|---|---|---|
For Manufacturer (Series/Model No.) | Wd., mm | Dp., mm | Lg., mm | Wd., mm | Dp., mm | Mounting Hardware Included | Pair | |
Aluminum | ||||||||
Schunk (EGP 40) | 6 | 16 | 55 | 62 | 22 | Yes | 00000000 | 0000000 |
![]() | ![]() Adjustable Finger Mount |
![]() Scale |
Attach adjustable finger mounts to your Schunk grippers, so they can handle a wider range of part sizes and shapes. Each mount has a positioning slide that moves along a rail, which has a scale for making adjustments. Connect your fingers to the slides, position them on the rail, and tighten the knob to secure them in place. Use one mount for as many fingers as your gripper will hold.
Gripper | Finger | ||||||||||||
---|---|---|---|---|---|---|---|---|---|---|---|---|---|
For Manufacturer (Series/Model No.) | Manufacturer (Series/Model No.) | Rail Lg., mm | Travel Lg., mm | Carriage Wd., mm | O'all Ht., mm | Adjustment Increments (Lg.), mm | Bolt Hole Thread Size | No. of Bolt Holes | Bolt Hole Thread Size | No. of Bolt Holes | Mounting Fasteners Included | Each | |
Anodized Aluminum | |||||||||||||
With Removable Positioning Slides | |||||||||||||
Schunk (JPG, JGZ, PGN+, PGN+E, PGN+P, PZN+ 80) | Schunk (UZB 80) | 79 | 44 | 42 | 39.5 | 2 | M5 × 0.8 mm | 2 | M5 × 0.8 mm | 2 | No | 00000000 | 0000000 |
Schunk (JPG, JGZ, PGN+, PGN+E, PGN+P, PZN+ 100) | Schunk (UZB 100) | 96.5 | 55 | 47 | 45.5 | 3 | M6 × 1 mm | 2 | M6 × 1 mm | 2 | No | 00000000 | 000000 |
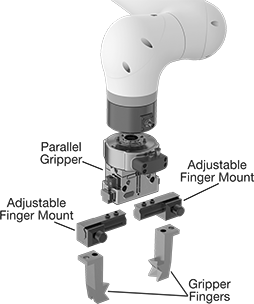
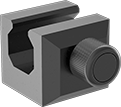
Removable positioning slides are part of the adjustable finger mounts. Add additional slides for tasks that require frequent finger changes. Having slides on hand with fingers already attached, makes it quick and easy to retool your gripper.
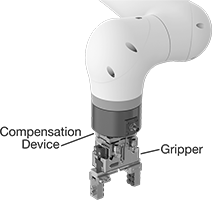
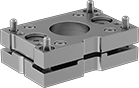
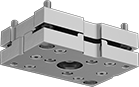
Compensation devices help you avoid jams and keep automated assembly, bin picking, and machine tending jobs running smoothly. They mount between your gripper and robot arm and have rubber pads that compress slightly when pressure is applied, allowing your grippers to adjust and grasp misaligned parts. These pads also compensate when aligning parts during placement, which increases efficiency and reliability in your process, while protecting parts and robots from wear.
These devices tilt and rotate on three axes, so grippers can grab parts in horizontal, vertical, and angled positions. They do not communicate with controllers, so there’s no need for electrical connections.
Capacity | Robot Arm Side | Gripper Side | |||||||||||||
---|---|---|---|---|---|---|---|---|---|---|---|---|---|---|---|
For Manufacturer (Series/Model No.) | English | Metric | Newtons | Lg., mm | Wd., mm | Dp., mm | Bolt Hole Thread Size (No. of) | Mounting Fasteners Included | Bolt Hole Thread Size (No. of) | Mounting Fasteners Included | Z-Axis Deflection | Y-Axis Deflection | X-Axis Deflection | Each | |
Anodized Aluminum Housing | |||||||||||||||
Schunk (PGN+E 80) | 335 lbs. | 150 kg | 1,500 N | 19.6 | 63 | 42 | M4 × 0.7 mm (4) | Yes | M4 × 0.7 mm (4) | No | ±2° | ±1.5° | ±1° | 00000000 | 0000000 |
Schunk (PGN+E 100) | 450 lbs. | 200 kg | 2,000 N | 22.6 | 81 | 50 | M5 × 0.8 mm (4) | Yes | M5 × 0.8 mm (4) | No | ±1.2° | ±1.5° | ±1° | 00000000 | 000000 |
Adjustable Finger Mounts for Schunk Grippers
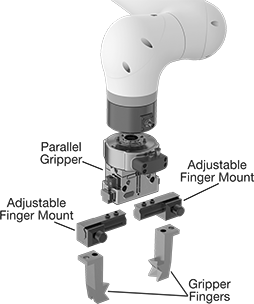
Attach these mounts to your Schunk grippers, so they can handle a wider range of part sizes and shapes. Each mount has a positioning slide that moves along a rail, which has a scale for making adjustments. Connect your fingers (not included) to the slides, position them on the rail, and tighten the knob to secure them in place. Use one mount for as many fingers as your gripper will hold.
Removable positioning slides are good for tasks that require frequent finger changes. Having additional slides on hand with fingers already attached, makes it quick and easy to retool your gripper.
Warning: Never use to lift people or items over people.
For technical drawings and 3-D models, click on a part number.
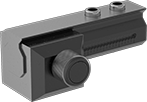
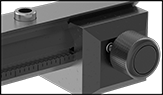
For Manufacturer | Gripper | Finger | |||||||||||||
---|---|---|---|---|---|---|---|---|---|---|---|---|---|---|---|
Series | Model No. | Manufacturer (Series/Model No.) | Rail Lg., mm | Travel Lg., mm | Carriage Wd., mm | O'all Ht., mm | Adjustment Increments (Lg.), mm | Bolt Hole Thread Size | No. of Bolt Holes | Bolt Hole Thread Size | No. of Bolt Holes | Mounting Fasteners Included | Wt. | Each | |
Anodized Aluminum | |||||||||||||||
With Nonremovable Positioning Slides | |||||||||||||||
JGP JGP-P JGZ PGN+ PGN+E PGN+P PZN+ | 64 | Schunk (UZB 64) | 63.5 | 33 | 36 | 36 | 2 | M4 × 0.7 mm | 2 | M4 × 0.7 mm | 2 | No | 0.24 lbs. / 0.11 kg | 00000000 | 0000000 |
With Removable Positioning Slides | |||||||||||||||
JGP JGP-P JGZ PGN+ PGN+E PGN+P PZN+ | 80 | Schunk (UZB 80) | 79 | 44 | 42 | 39.5 | 2 | M5 × 0.8 mm | 2 | M5 × 0.8 mm | 2 | No | 0.37 lbs. / 0.17 kg | 00000000 | 000000 |
JGP JGP-P JGZ PGN+ PGN+E PGN+P PZN+ | 100 | Schunk (UZB 100) | 96.5 | 55 | 47 | 45.5 | 3 | M6 × 1 mm | 2 | M6 × 1 mm | 2 | No | 0.57 lbs. / 0.26 kg | 00000000 | 000000 |
JGP JGP-P JGZ PGN+ PGN+E PGN+P PZN+ | 125 | Schunk (UZB 125) | 112.75 | 72 | 52 | 49 | 3 | M6 × 1 mm | 2 | M6 × 1 mm | 2 | No | 0.77 lbs. / 0.35 kg | 00000000 | 000000 |