Easy-to-Print PLA 3D Printer Filaments
![]() | ![]() Black | ![]() Blue | ![]() Gray | ![]() Green |
![]() Orange | ![]() Red | ![]() White | ![]() Yellow |
The most commonly used 3D printing material, these PLA filaments make detailed parts at a low melting point, so they won’t warp as they cool, rarely clog nozzles, and don’t require a heated printer bed. They’re also unlikely to drip and produce plastic strings for a clean finished part. In general, they’re best for printing prototypes instead of load-bearing parts since they’re not as strong as ABS or as heat resistant as PEEK. Print them on a fused filament fabrication (FFF) 3D printer.
Static-dissipative PLA filaments make parts that protect equipment from electrostatic shocks by diverting electrostatic discharges in a controlled way. They’re often used to create tool handles, tote trays, enclosures, and other parts that are used near sensitive electronics. To adjust the surface resistivity of your printed part, change the temperature of your printer’s extruder. As the extruder’s temperature increases, the printed part’s resistivity will decrease.
Filaments with an annealing temperature can be heat treated to make parts harder, stronger, and better at resisting heat. To anneal, heat your finished part to the listed temperature and then let it cool slowly.
Tensile strength is the best measure of a filament’s overall strength. Similar to the stress applied on a rope during a game of tug-of-war, it’s the amount of pulling force a material can handle before breaking. A higher rating means a stronger filament. A tensile strength of 5,000 psi and above is considered good; 12,000 psi and above is excellent.
Maximum exposure temperature is the point at which a printed part will begin to deform. Above this temperature, your part will start to lose structural integrity. Filaments that can be annealed are also rated for maximum temperature after annealing, which is the new maximum exposure temperature once that process completes.
For technical drawings and 3-D models, click on a part number.
Spool | Each | ||||||||||||
---|---|---|---|---|---|---|---|---|---|---|---|---|---|
Dia., mm | Printing Temp. | For Printer Bed Temp. | Tensile Strength | Max. Exposure Temp. | Annealing Temp. | Max. Temp. After Annealing | For Min. Nozzle Dia., mm | Dia., mm | Dp., mm | Wt., g | 1-9 | 10-Up | |
PLA Plastic | |||||||||||||
Opaque Black | |||||||||||||
1.75 | 190° to 230° C 374° to 446° F | 0° to 70° C 32° to 158° F | 9,500 psi (Good) | 60° C 140° F | 110° to 120° C 230° to 248° F | 130° C 266° F | 0.4 | 200 | 91 | 1,000 | 00000000 | 000000 | 000000 |
2.85 | 190° to 230° C 374° to 446° F | 0° to 70° C 32° to 158° F | 9,500 psi (Good) | 60° C 140° F | 110° to 120° C 230° to 248° F | 130° C 266° F | 0.4 | 200 | 91 | 1,000 | 00000000 | 00000 | 00000 |
Opaque Blue | |||||||||||||
1.75 | 190° to 230° C 374° to 446° F | 0° to 70° C 32° to 158° F | 9,500 psi (Good) | 60° C 140° F | 110° to 120° C 230° to 248° F | 130° C 266° F | 0.4 | 200 | 91 | 1,000 | 00000000 | 00000 | 00000 |
2.85 | 190° to 230° C 374° to 446° F | 0° to 70° C 32° to 158° F | 9,500 psi (Good) | 60° C 140° F | 110° to 120° C 230° to 248° F | 130° C 266° F | 0.4 | 200 | 91 | 1,000 | 00000000 | 00000 | 00000 |
Opaque Gray | |||||||||||||
1.75 | 190° to 230° C 374° to 446° F | 0° to 70° C 32° to 158° F | 9,500 psi (Good) | 60° C 140° F | 110° to 120° C 230° to 248° F | 130° C 266° F | 0.4 | 200 | 91 | 1,000 | 00000000 | 00000 | 00000 |
2.85 | 190° to 230° C 374° to 446° F | 0° to 70° C 32° to 158° F | 9,500 psi (Good) | 60° C 140° F | 110° to 120° C 230° to 248° F | 130° C 266° F | 0.4 | 200 | 91 | 1,000 | 00000000 | 00000 | 00000 |
Opaque Green | |||||||||||||
1.75 | 190° to 230° C 374° to 446° F | 0° to 70° C 32° to 158° F | 9,500 psi (Good) | 60° C 140° F | 110° to 120° C 230° to 248° F | 130° C 266° F | 0.4 | 200 | 91 | 1,000 | 00000000 | 00000 | 00000 |
2.85 | 190° to 230° C 374° to 446° F | 0° to 70° C 32° to 158° F | 9,500 psi (Good) | 60° C 140° F | 110° to 120° C 230° to 248° F | 130° C 266° F | 0.4 | 200 | 91 | 1,000 | 00000000 | 00000 | 00000 |
Opaque Orange | |||||||||||||
1.75 | 190° to 230° C 374° to 446° F | 0° to 70° C 32° to 158° F | 9,500 psi (Good) | 60° C 140° F | 110° to 120° C 230° to 248° F | 130° C 266° F | 0.4 | 200 | 91 | 1,000 | 00000000 | 00000 | 00000 |
2.85 | 190° to 230° C 374° to 446° F | 0° to 70° C 32° to 158° F | 9,500 psi (Good) | 60° C 140° F | 110° to 120° C 230° to 248° F | 130° C 266° F | 0.4 | 200 | 91 | 1,000 | 00000000 | 00000 | 00000 |
Opaque Red | |||||||||||||
1.75 | 190° to 230° C 374° to 446° F | 0° to 70° C 32° to 158° F | 9,500 psi (Good) | 60° C 140° F | 110° to 120° C 230° to 248° F | 130° C 266° F | 0.4 | 200 | 91 | 1,000 | 00000000 | 00000 | 00000 |
2.85 | 190° to 230° C 374° to 446° F | 0° to 70° C 32° to 158° F | 9,500 psi (Good) | 60° C 140° F | 110° to 120° C 230° to 248° F | 130° C 266° F | 0.4 | 200 | 91 | 1,000 | 00000000 | 00000 | 00000 |
Opaque White | |||||||||||||
1.75 | 190° to 230° C 374° to 446° F | 0° to 70° C 32° to 158° F | 9,500 psi (Good) | 60° C 140° F | 110° to 120° C 230° to 248° F | 130° C 266° F | 0.4 | 200 | 91 | 1,000 | 00000000 | 00000 | 00000 |
2.85 | 190° to 230° C 374° to 446° F | 0° to 70° C 32° to 158° F | 9,500 psi (Good) | 60° C 140° F | 110° to 120° C 230° to 248° F | 130° C 266° F | 0.4 | 200 | 91 | 1,000 | 00000000 | 00000 | 00000 |
Opaque Yellow | |||||||||||||
1.75 | 190° to 230° C 374° to 446° F | 0° to 70° C 32° to 158° F | 9,500 psi (Good) | 60° C 140° F | 110° to 120° C 230° to 248° F | 130° C 266° F | 0.4 | 200 | 91 | 1,000 | 00000000 | 00000 | 00000 |
2.85 | 190° to 230° C 374° to 446° F | 0° to 70° C 32° to 158° F | 9,500 psi (Good) | 60° C 140° F | 110° to 120° C 230° to 248° F | 130° C 266° F | 0.4 | 200 | 91 | 1,000 | 00000000 | 00000 | 00000 |
Static-Dissipative PLA Plastic | |||||||||||||
Opaque Black | |||||||||||||
1.75 | 210° to 220° C 410° to 430° F | 23° to 60° C 73° to 140° F | 7,970 psi (Good) | 55° C 131° F | __ | __ | 0.25 | 200 | 70 | 750 | 0000000 | 000000 | 00000 |
2.85 | 210° to 220° C 410° to 430° F | 23° to 60° C 73° to 140° F | 7,970 psi (Good) | 55° C 131° F | __ | __ | 0.25 | 200 | 70 | 750 | 0000000 | 000000 | 00000 |
UV-Indicating Easy-to-Print PLA 3D Printer Filaments
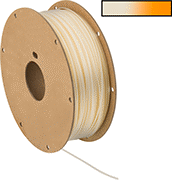
Often used to monitor UV exposure and test UV curing and sterilization equipment, parts made from these filaments change color when exposed to the sun or UV lights. Made from PLA, the most commonly used 3D printing material, they make detailed parts at a low melting point. As a result, they rarely clog nozzles, won’t warp as they cool, and don’t require a heated printer bed. They’re also unlikely to drip and produce plastic strings for a clean finished part. Print them on a fused filament fabrication (FFF) 3D printer.
Tensile strength is the best measure of a filament’s overall strength. Similar to the stress applied on a rope during a game of tug-of-war, it’s the amount of pulling force a material can handle before breaking. A higher rating means a stronger filament. A tensile strength of 5,000 psi and above is considered good; 12,000 psi and above is excellent.
Maximum exposure temperature is the point at which a printed part will begin to deform. Above this temperature, your part will start to lose structural integrity.
Spool | ||||||||||
---|---|---|---|---|---|---|---|---|---|---|
Dia., mm | Printing Temp. | For Printer Bed Temp. | Tensile Strength, psi | Max. Exposure Temp. | For Min. Nozzle Dia., mm | Dia., mm | Dp., mm | Wt., g | Each | |
PLA Plastic | ||||||||||
Beige to Orange Indicator | ||||||||||
1.75 | 190° to 230° C 374° to 446° F | 25° to 60° C 77° to 140° F | 6,620 (Good) | 58° C 136° F | 0.4 | 200 | 65 | 1,000 | 0000000 | 000000 |
Impact-Resistant ABS 3D Printer Filaments
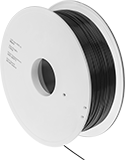

Bumps, scrapes, and falls won’t damage these tough ABS filaments. Known for their durability, they absorb impact without cracking or breaking, and won’t degrade when heated. Use them to print tool handles, storage cases, and other parts that are handled or dropped frequently. These filaments are a good place to start if you’re experimenting with printing impact-resistant parts.
Use with a fused filament fabrication (FFF) 3D printer. These filaments have a high melting point and must be printed onto a heated bed. Without it, parts will cool too quickly and warp. These filaments also release fumes as they are printed, so use an enclosed printer or a fume exhauster to ventilate them. For heavy impact, use polycarbonate ABS filaments. The polycarbonate adds strength to printed parts.
Carbon-fiber-filled ABS filaments make rigid parts that are difficult to bend and break. Their parts can also be threaded and machined more easily than ABS filaments without a filler. Carbon-fiber- and fiberglass-filled filaments are abrasive, so you should use them with an abrasion-resistant nozzle. They will wear out other nozzles.
Static-dissipative filaments make parts that protect equipment from electrostatic shocks by diverting electrostatic discharges in a controlled way. Use them to create tool handles, tote trays, enclosures, and other parts that are used near sensitive electronics. To adjust the surface resistivity of your printed part, change the temperature of your printer’s extruder. As the extruder’s temperature increases, the printed part’s resistivity will decrease.
Filaments rated UL 94 V-0 meet strict flammability standards. Use them to create holders, guards, housings, and other parts that protect sensitive, flammable equipment and machinery.
Tensile strength is the best measure of a filament's overall strength. Similar to the stress applied on a rope during a game of tug-of-war, it's the amount of pulling force a material can handle before breaking. A higher rating means a stronger filament. A tensile strength of 5,000 psi and above is considered good; 12,000 psi and above is excellent.
Maximum exposure temperature is the point at which a printed part will begin to deform. Above this temperature, your printed parts will start to lose structural integrity.
Spool | ||||||||||||
---|---|---|---|---|---|---|---|---|---|---|---|---|
Dia., mm | Printing Temp. | For Printer Bed Temp. | Tensile Strength | Surface Resistivity, ohms/sq. | Max. Exposure Temp. | For Min. Nozzle Dia., mm | Dia., mm | Dp., mm | Wt., g | Color | Each | |
Carbon-Fiber-Filled ABS Plastic | ||||||||||||
1.75 | 220° to 240° C 428° to 464° F | 100° to 110° C 212° to 230° F | 6,670 psi (Good) | __ | 76° C 169° F | 0.4 | 195 | 55 | 750 | Black | 00000000 | 000000 |
2.85 | 220° to 240° C 428° to 464° F | 100° to 110° C 212° to 230° F | 6,670 psi (Good) | __ | 76° C 169° F | 0.4 | 195 | 55 | 750 | Black | 00000000 | 00000 |
ABS Plastic—Static-Dissipative | ||||||||||||
1.75 | 220° to 240° C 428° to 464° F | 100° to 110° C 212° to 230° F | 8,410 psi (Good) | 107-109 | 97° C 207° F | 0.4 | 200 | 75 | 750 | Black | 0000000 | 000000 |
2.85 | 220° to 240° C 428° to 464° F | 100° to 110° C 212° to 230° F | 8,410 psi (Good) | 107-109 | 97° C 207° F | 0.4 | 200 | 75 | 750 | Black | 0000000 | 000000 |
ABS Plastic—UL 94 V-0 | ||||||||||||
1.75 | 220° to 240° C 428° to 464° F | 100° to 110° C 212° to 230° F | 6,520 psi (Good) | __ | 95° C 203° F | 0.4 | 200 | 75 | 750 | Black | 00000000 | 00000 |
2.85 | 220° to 240° C 428° to 464° F | 100° to 110° C 212° to 230° F | 6,520 psi (Good) | __ | 95° C 203° F | 0.4 | 200 | 75 | 750 | Black | 00000000 | 00000 |
Polycarbonate ABS Plastic—UL 94 V-0 | ||||||||||||
1.75 | 265° to 285° C 509° to 545° F | 110° to 120° C 230° to 248° F | 8,700 psi (Good) | __ | 125° C 257° F | 0.4 | 200 | 75 | 750 | Black | 0000000 | 00000 |
UV- and Impact-Resistant ASA 3D Printer Filaments
![]() | ![]() | ![]() |
![]() | ![]() |
Best for outdoor use, parts made from these ASA filaments are UV resistant, so they won't warp or crack from prolonged sun exposure. They’re also durable, so they absorb impact without breaking and won’t degrade when heated.
Use with fused filament fabrication (FFF) 3D printer. These filaments have a high melting point and must be printed onto a heated bed. Without it, parts will cool too quickly and warp. These filaments also release fumes as they are printed, so use an enclosed printer or a fume exhauster to ventilate them.
Tensile strength is the best measure of a filament's overall strength. Similar to the stress applied on a rope during a game of tug-of-war, it's the amount of pulling force a material can handle before breaking. A higher rating means a stronger filament. A tensile strength of 5,000 psi and above is considered good; 12,000 psi and above is excellent.
Maximum exposure temperature is the point at which a printed part will begin to deform. Above this temperature, your printed parts will start to lose structural integrity.
Spool | |||||||||||
---|---|---|---|---|---|---|---|---|---|---|---|
Dia., mm | Printing Temp. | For Printer Bed Temp. | Tensile Strength | Max. Exposure Temp. | For Min. Nozzle Opening Dia., mm | Dia., mm | Dp., mm | Wt., g | Color | Each | |
ASA Plastic | |||||||||||
1.75 | 235° to 255° C 455° to 491° F | 90° to 110° C 194° to 230° F | 6,520 psi (Good) | 95° C 203° F | 0.4 | 200 | 75 | 1,000 | 00000000 | 000000 | |
2.85 | 235° to 255° C 455° to 491° F | 90° to 110° C 194° to 230° F | 6,520 psi (Good) | 87° C 188° F | 0.4 | 198 | 78 | 1,000 | 00000000 | 00000 |
High-Strength Impact-Resistant Polycarbonate 3D Printer Filaments
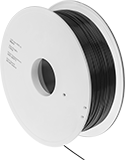
Create strong, durable parts that carry heavy loads and absorb blows and other impact without cracking or breaking. Made of polycarbonate, these filaments are stronger and resist heat better than other impact-resistant filaments, such as those made from ABS or ASA.
Use with a fused filament fabrication (FFF) 3D printer. These filaments have a high melting point and must be printed onto a heated bed. Without it, parts will cool too quickly and warp. These filaments also release fumes as they are printed, so use an enclosed printer or a fume exhauster to ventilate them.
Carbon-fiber-filled polycarbonate filaments make rigid parts that are difficult to bend and break. Parts made from these filaments can also be threaded and machined more easily than parts made from polycarbonate filaments without a filler. Fiberglass-filled polycarbonate filaments make parts that are less likely to warp or shrink than parts made from polycarbonate filaments without a filler. Both carbon-fiber- and fiberglass-filled filaments are abrasive, so you should use them with an abrasion-resistant nozzle.
Static-dissipative filaments make parts that protect equipment from electrostatic shocks by diverting electrostatic discharges in a controlled way. Use them to create tool handles, tote trays, enclosures, and other parts that are used near sensitive electronics. To adjust the surface resistivity of your printed part, change the temperature of your printer’s extruder. As the extruder’s temperature increases, the printed part’s resistivity will decrease.
UL 94 V-0 rated filaments meet strict flammability standards. Use them to create holders, guards, housings, and other parts that protect sensitive, flammable equipment and machinery.
Tensile strength is the best measure of a filament's overall strength. Similar to the stress applied on a rope during a game of tug-of-war, it's the amount of pulling force a material can handle before breaking. A higher rating means a stronger filament. A tensile strength of 5,000 psi and above is considered good; 12,000 psi and above is excellent.
Maximum exposure temperature is the point at which a printed part will begin to deform. Above this temperature, your printed parts will start to lose structural integrity.
Spool | |||||||||||||
---|---|---|---|---|---|---|---|---|---|---|---|---|---|
Dia., mm | Printing Temp. | For Printer Bed Temp. | Tensile Strength | Surface Resistivity, ohms/sq. | Hardness | Max. Exposure Temp. | For Min. Nozzle Opening Dia., mm | Dia., mm | Dp., mm | Wt., g | Color | Each | |
Polycarbonate Plastic | |||||||||||||
1.75 | 280° to 310° C 536° to 590° F | 110° to 120° C 230° to 248° F | 8,990 psi (Good) | __ | Durometer 84D (Hard) | 135° C 275° F | 0.4 | 195 | 40 | 500 | Black | 00000000 | 000000 |
Carbon-Fiber-Filled Polycarbonate Plastic | |||||||||||||
1.75 | 260° to 280° C 500° to 535° F | 80° to 100° C 175° to 210° F | 10,580 psi (Good) | __ | Not Rated | 115° C 245° F | 0.4 | 195 | 55 | 750 | Black | 00000000 | 00000 |
2.85 | 260° to 280° C 500° to 535° F | 80° to 100° C 175° to 210° F | 10,580 psi (Good) | __ | Not Rated | 115° C 245° F | 0.4 | 195 | 55 | 750 | Black | 00000000 | 00000 |
Polycarbonate Plastic—Static-Dissipative | |||||||||||||
1.75 | 260° to 300° C 500° to 572° F | 110° to 120° C 230° to 248° F | 9,860 psi (Good) | 107-109 | Rockwell R125 (Hard) | 135° C 275° F | 0.4 | 200 | 75 | 750 | Black | 0000000 | 000000 |
Fiberglass-Filled Polycarbonate Plastic—UL 94 V-0 | |||||||||||||
1.75 | 280° to 330° C 536° to 626° F | 80° to 100° C 176° to 212° F | 5,300 psi (Good) | __ | Not Rated | 124° C 255° F | 0.6 | 200 | 55 | 700 | Black | 0000000 | 000000 |
2.85 | 280° to 330° C 536° to 626° F | 80° to 100° C 176° to 212° F | 5,300 psi (Good) | __ | Not Rated | 124° C 255° F | 0.6 | 200 | 55 | 700 | Black | 0000000 | 000000 |
Wear-Resistant Nylon 3D Printer Filaments
![]() | ![]() Black |
![]() Gray |
Print tough, long-lasting parts that won’t scratch or wear out from constant motion and friction, such as gears and washers. You can even tap or drill the parts without them cracking or shattering.
Use these filaments with fused filament fabrication (FFF) printers. Because of their relatively high melting point, a heated printer bed is recommended. These filaments also emit fumes when printing, so it’s best to use them in an enclosed printer or to remove the fumes with a fume exhauster. Store them in a sealed container with a desiccant so they don’t absorb moisture in the air, which can make them unusable.
Nylon 6/66 filaments are the strongest nylon filaments without a filler, but may warp while cooling.
Carbon-fiber-filled nylon filaments make rigid parts that are difficult to bend and break. Their parts can also be threaded and machined more easily than the same filaments without any filler. However, they’re abrasive, so only use them with abrasion-resistant nozzles.
Fiberglass-filled nylon filaments make strong parts that are less prone to warping or shrinking than the same filaments without any filler. However, they’re abrasive, so only use them with abrasion-resistant nozzles.
Tensile strength is the best measure of a filament's overall strength. Similar to the stress applied on a rope during a game of tug-of-war, it's the amount of pulling force a material can handle before breaking. A higher rating means a stronger filament. A tensile strength of 5,000 psi and above is considered good; 12,000 psi and above is excellent.
Maximum exposure temperature is the point at which a printed part will begin to deform. Above this temperature, your printed parts will start to lose structural integrity.
Spool | |||||||||||
---|---|---|---|---|---|---|---|---|---|---|---|
Dia., mm | Printing Temp. | For Printer Bed Temp. | Tensile Strength | Hardness | Max. Exposure Temp. | For Min. Nozzle Opening Dia., mm | Dia., mm | Dp., mm | Wt., g | Each | |
Nylon Plastic 6/66 | |||||||||||
Black | |||||||||||
1.75 | 255° to 275° C 491° to 527° F | 60° to 70° C 140° to 158° F | 8,700 psi (Good) | Durometer 60D (Medium) | 85° C 185° F | 0.25 | 200 | 75 | 750 | 000000 | 000000 |
Carbon Fiber-Filled Nylon Plastic | |||||||||||
Black | |||||||||||
1.75 | 280° to 300° C 535° to 570° F | 50° C 122° F | 15,225 psi (Excellent) | Not Rated | 125° C 257° F | 0.4 | 200 | 65 | 500 | 000000 | 00000 |
Fiberglass-Filled Nylon Plastic 6 | |||||||||||
Gray | |||||||||||
1.75 | 280° to 300° C 536° to 572° F | 25° to 50° C 77° to 122° F | 11,950 psi (Good) | Not Rated | 70° C 158° F | 0.4 | 250 | 117 | 2,000 | 0000000 | 000000 |
2.85 | 280° to 300° C 536° to 572° F | 25° to 50° C 77° to 122° F | 11,950 psi (Good) | Not Rated | 70° C 158° F | 0.4 | 250 | 117 | 2,000 | 0000000 | 000000 |
Steam-Resistant High-Temperature PSU 3D Printer Filaments
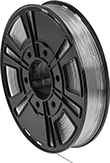

Sterilize your printed parts without them expanding, deforming, or weakening. These PSU filaments resist steam and heat, so you can sterilize parts in an autoclave. They also can be sterilized with ethylene oxide, radiation, plasma, dry heat, and cold sterilization methods. Print these filaments on a fused filament fabrication (FFF) 3D printer. Because of their high melting points, you'll need an all-metal extruder and heated printer bed to reach their minimum printing temperature. Without the heated printer bed, parts will cool too quickly and warp.
Tensile strength is the best measure of a filament’s overall strength. Similar to the stress applied on a rope during a game of tug-of-war, it’s the amount of pulling force a material can handle before breaking. A higher rating means a stronger filament. A tensile strength of 5,000 psi and above is considered good; 12,000 psi and above is excellent.
Maximum exposure temperature is the point at which a printed part will begin to deform. Above this temperature, your part will start to lose structural integrity.
Spool | |||||||||||
---|---|---|---|---|---|---|---|---|---|---|---|
Dia., mm | Printing Temp. | For Printer Bed Temp. | Tensile Strength | Max. Exposure Temp. | For Min. Nozzle Dia., mm | Dia., mm | Dp., mm | Wt., g | Color | Each | |
PSU Plastic | |||||||||||
1.75 | 350° to 380° C 662° to 716° F | 140° to 160° C 284° to 320° F | 10,730 psi (Good) | 172° C 342° F | 0.4 | 198 | 42 | 500 | Semi-Clear Beige | 0000000 | 000000 |
Ultra-Strength High-Temperature PAEK 3D Printer Filaments
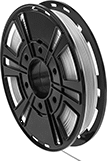

Parts made from these PAEK filaments, a family of materials that includes PEEK and PEKK, remain strong in high temperatures and hold up to wear from repeated use. They don’t degrade when exposed to most chemicals, so they’re often used to print parts for demanding chemical processing applications. Print these filaments on a fused filament fabrication (FFF) 3D printer. Because of their high melting point, you'll need an all-metal extruder and heated printer bed to reach their minimum printing temperature. Without the heated printer bed, parts will cool too quickly and warp.
Fiberglass-filled PEEK filaments make stronger parts that are less likely to warp and shrink than unfilled PEEK filaments. Since they’re abrasive, you should only use them with an abrasion-resistant nozzle.
Tensile strength is the best measure of a filament's overall strength. Similar to the stress applied on a rope during a game of tug-of-war, it's the amount of pulling force a material can handle before breaking. A higher rating means a stronger filament. A tensile strength of 5,000 psi and above is considered good; 12,000 psi and above is excellent.
Maximum exposure temperature is the point at which a printed part will begin to deform. Above this temperature, your printed parts will start to lose structural integrity.
Annealing is the process of heating prints to a specific annealing temperature and then slowly allowing them to cool. This makes the finished print harder, stronger, and better at resisting heat. Maximum temperature after annealing replaces the maximum exposure temperature once this process has been completed.
Spool | |||||||||||||
---|---|---|---|---|---|---|---|---|---|---|---|---|---|
Dia., mm | Printing Temp. | For Printer Bed Temp. | Tensile Strength | Max. Exposure Temp. | Max. Annealing Temp. | Max. Temp. After Annealing | For Min. Nozzle Dia., mm | Dia., mm | Dp., mm | Wt., g | Color | Each | |
PEEK Plastic | |||||||||||||
1.75 | 375° to 410° C 707° to 770° F | 130° to 145° C 266° to 293° F | 14,500 psi (Excellent) | 140° C 284° F | 140° C 284° F | 230° C 446° F | 0.4 | 195 | 40 | 500 | Opaque Beige | 0000000 | 0000000 |
Fiberglass-Filled PEEK Plastic | |||||||||||||
1.75 | 375° to 410° C 707° to 770° F | 130° to 145° C 266° to 293° F | 13,050 psi (Excellent) | 260° C 500° F | 140° C 284° F | 315° C 599° F | 0.4 | 195 | 40 | 500 | Opaque Beige | 0000000 | 000000 |
High-Temperature PEI 3D Printer Filaments
![]() | ![]() |
![]() |
Often used to make parts that will be used near ovens, engines, and other hot machinery, these PEI filaments remain strong and rigid in temperatures that would soften most plastic. They’re a lightweight alternative to machined metal parts. Print these filaments on a fused filament fabrication (FFF) 3D printer. Because of their high melting points, you'll need an all-metal extruder and heated printer bed to reach their minimum printing temperature. Without the heated printer bed, parts will cool too quickly and warp.
Tensile strength is the best measure of a filament’s overall strength. Similar to the stress applied on a rope during a game of tug-of-war, it’s the amount of pulling force a material can handle before breaking. A higher rating means a stronger filament. A tensile strength of 5,000 psi and above is considered good; 12,000 psi and above is excellent.
Maximum exposure temperature is the point at which a printed part will begin to deform. Above this temperature, your part will start to lose structural integrity.
Spool | |||||||||||
---|---|---|---|---|---|---|---|---|---|---|---|
Dia., mm | Printing Temp. | For Printer Bed Temp. | Tensile Strength | Max. Exposure Temp. | For Min. Nozzle Dia., mm | Dia., mm | Dp., mm | Wt., g | Color | Each | |
PEI Plastic | |||||||||||
1.75 | 350° to 380° C 662° to 716° F | 140° to 160° C 284° to 320° F | 7,830 psi (Good) | 158° C 316° F | 0.4 | 195 | 40 | 500 | Semi-Clear Beige | 0000000 | 0000000 |
1.75 | 370° to 390° C 698° to 734° F | 120° to 160° C 248° to 320° F | 8,120 psi (Good) | 208° C 406° F | 0.4 | 195 | 40 | 500 | Opaque Gold | 0000000 | 000000 |
Dremel 3D Printer Filaments
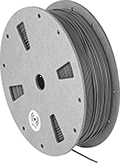







Build parts and prototypes from these filaments using Dremel fused filament fabrication (FFF) 3D printers. An RFID tag on the spool communicates with your printer, automatically adjusting it to the correct temperature and print speed for the filament material and notifying you when the filament is running out.
PLA filaments are the most commonly used in 3D printing. PLA is easy to use; it rarely clogs nozzles, doesn’t require a heated printer bed, and prints at a low temperature—meaning parts won’t warp while cooling. It produces string-free parts, so you can use it to print with a high level of detail. Less durable and more sensitive to heat than ECO-ABS, PLA is better for printing prototypes than end-use parts.
ECO-ABS is less brittle and more impact resistant than PLA, so these filaments are good for printing parts that are frequently handled, dropped, or heated. They are, however, a little more high maintenance—parts may warp during cooling, so they require a heated printer bed.
Nylon resists scratches and wear, and is often used to create parts that encounter constant friction such as gears or bearings. Nylon parts also won’t crack or shatter when they’re drilled or tapped. Exposure to humidity makes these filaments brittle and unusable, so they need to be stored in a sealed container with a desiccant. Like ECO-ABS, parts can warp during cooling and need a heated printer bed. Make sure your printer is connected to a ventilation system, as nylon emits fumes during printing.
PETG is more moisture resistant than ECO-ABS, making it a great choice for printing parts for use in humid or wet environments. Generally, PETG’s other properties fall somewhere between those of PLA and ECO-ABS. It’s more flexible and durable than PLA, but less so than ECO-ABS. It’s harder to print than PLA because it requires a heated printer bed, but easier to print than ECO-ABS. PETG filaments should be kept in a sealed container with a desiccant.
Tensile strength is the best measure of a filament's overall strength. Similar to the stress applied on a rope during a game of tug-of-war, it's the amount of pulling force a material can handle before breaking. A higher rating means a stronger filament. A tensile strength of 5,000 psi and above is considered good; 12,000 psi and above is excellent.
Maximum exposure temperature is the point at which a printed part will begin to deform. Above this temperature, your printed parts will start to lose structural integrity.
Spool | ||||||||||||
---|---|---|---|---|---|---|---|---|---|---|---|---|
Manufacturer Model No. | Dia., mm | Printing Temp. | For Printer Bed Temp. | Tensile Strength | Max. Exposure Temp. | For Min. Nozzle Opening Dia., mm | Dia., mm | Dp., mm | Wt., g | Choose a Color | Each | |
PLA Plastic | ||||||||||||
__ | 1.75 | 200° to 230° C 395° to 445° F | 35° C 95° F | 6,620 psi (Good) | 60° C 140° F | 0.25 | 180 | 55 | 750 | 000000 | 000000 | |
ECO-ABS Plastic | ||||||||||||
ECO-BLA-01 | 1.75 | 190° to 240° C 374° to 464° F | 60° C 140° F | 8,410 psi (Good) | 63° C 145° F | 0.2 | 181 | 55 | 750 | Black | 0000000 | 00000 |
ECO-WHI-01 | 1.75 | 190° to 240° C 374° to 464° F | 60° C 140° F | 8,410 psi (Good) | 63° C 145° F | 0.2 | 181 | 55 | 750 | White | 0000000 | 00000 |
Nylon Plastic | ||||||||||||
DF45-NYP-B | 1.75 | 230° to 250° C 446° to 482° F | 80° C 176° F | 7,540 psi (Good) | 155° C 311° F | 0.4 | 180 | 55 | 500 | Black | 0000000 | 00000 |
PETG Plastic | ||||||||||||
PETG-TRA-01 | 1.75 | 240° to 260° C 464° to 500° F | 80° C 175° F | 7,250 psi (Good) | 84° C 183° F | 0.2 | 181 | 55 | 750 | Clear | 0000000 | 00000 |
Moisture-Resistant Polyester 3D Printer Filaments
![]() | ![]() |
![]() |
Parts printed with these polyester filaments absorb less moisture than other types of plastic, making them ideal for use in wet or humid environments. They are more durable and flexible than PLA, and easier to print than ABS. Use these filaments with fused filament fabrication (FFF) 3D printers, and print onto a heated print bed. Printing onto a cool surface causes the molten filament to change temperature rapidly, which can warp your designs. Although finished parts are moisture-resistant, these filaments are sensitive to humidity, and should be stored in a dehumidifying cabinet or a sealed container with desiccant for the best printing quality.
PETG contains glycol, so it is less brittle and easier to print than PETT and PCTG. Carbon-fiber-filled PETG is often used to make rigid parts that are difficult to bend and break. Finished parts are easier to thread and machine than unfilled parts. Because these filaments are abrasive, use them only with abrasion-resistant nozzles.
PCTG is more impact resistant than PETT and PETG and holds up to a wide range of acids and bases without breaking down. It is often used for printing parts that will be exposed to chemicals and oils.
Static-dissipative filaments make parts that protect equipment from electrostatic shocks by diverting electrostatic discharges in a controlled way. Create tool handles, tote trays, enclosures, and other parts that are used near sensitive electronics. To adjust the surface resistivity of your printed part, change the temperature of your printer’s extruder. As the extruder’s temperature increases, the printed part’s resistivity will decrease.
Antistatic filaments make parts that prevent the buildup of static electricity. This helps prevent the buildup of dust or fibers on the surface of your finished part. However, they are not as effective at preventing electrostatic discharge as static-dissipative filaments.
Tensile strength is the best measure of a filament's overall strength. Similar to the stress applied on a rope during a game of tug-of-war, it's the amount of pulling force a material can handle before breaking. A higher rating means a stronger filament. A tensile strength of 5,000 psi and above is considered good; 12,000 psi and above is excellent.
Maximum exposure temperature is the point at which a printed part will begin to deform. Above this temperature, your printed parts will start to lose structural integrity.
Spool | ||||||||||||
---|---|---|---|---|---|---|---|---|---|---|---|---|
Dia., mm | Printing Temp. | For Printer Bed Temp. | Tensile Strength | Hardness | Surface Resistivity, ohms/sq. | Max. Exposure Temp. | For Min. Nozzle Opening Dia., mm | Dia., mm | Dp., mm | Wt., g | Each | |
PETG Plastic—Static Dissipative | ||||||||||||
Opaque Black | ||||||||||||
1.75 | 230° to 260° C 446° to 500° F | 60° to 90° C 140° to 194° F | 7,250 psi (Good) | Rockwell R110 (Hard) | 107-109 | 75° C 167° F | 0.4 | 200 | 75 | 750 | 0000000 | 0000000 |
2.85 | 230° to 260° C 446° to 500° F | 60° to 90° C 140° to 194° F | 7,250 psi (Good) | Rockwell R110 (Hard) | 107-109 | 75° C 167° F | 0.4 | 200 | 75 | 750 | 0000000 | 000000 |
Carbon-Fiber-Filled PETG Plastic—Antistatic | ||||||||||||
Opaque Black | ||||||||||||
1.75 | 230° to 260° C 446° to 500° F | 60° C 140° F | 8,120 psi (Good) | Not Rated | 109-1012 | 77° C 170° F | 0.4 | 200 | 60 | 750 | 000000 | 00000 |
2.85 | 230° to 260° C 446° to 500° F | 60° C 140° F | 8,120 psi (Good) | Not Rated | 109-1012 | 77° C 170° F | 0.4 | 200 | 60 | 750 | 0000000 | 00000 |
PCTG Plastic | ||||||||||||
Clear | ||||||||||||
1.75 | 250° to 270° C 482° to 518° F | 70° to 80° C 158° to 176° F | 5,510 psi (Good) | Not Rated | __ | 70° C 158° F | 0.25 | 200 | 68 | 1,000 | 00000000 | 00000 |
2.85 | 250° to 270° C 482° to 518° F | 70° to 80° C 158° to 176° F | 5,510 psi (Good) | Not Rated | __ | 70° C 158° F | 0.25 | 200 | 68 | 1,000 | 00000000 | 00000 |
Chemical-Resistant PPSU 3D Printer Filaments
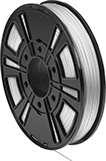

Fabricate custom bottles, packaging, and other parts for chemical processing. Made of PPSU, these filaments won’t break down even after prolonged exposure to virtually any acid, base, or solvent. They also stand up to oil and fuel, so they’re sometimes made into automotive parts. Because they have a low density and won’t transfer electricity, they make parts that are lightweight and protect components from electric currents. These filaments are easy to store too, since they resist absorbing water. Rated UL 94 V-0, they meet flammability standards.
Print these filaments on a fused filament fabrication (FFF) 3D printer. Due to its high melting point, PPSU is more difficult to print than most other materials. You need an all-metal extruder and a heated printer bed to reach its minimum printing temperature. After printing, anneal your part in an oven for 2 to 4 hours to reach its maximum strength, temperature, and ability to resist chemicals.
Tensile strength is the best measure of a filament’s overall strength. Similar to the stress applied on a rope during a game of tug-of-war, it’s the amount of pulling force a material can handle before breaking. A higher rating means a stronger filament. A tensile strength of 5,000 psi and above is considered good; 12,000 psi and above is excellent.
Maximum exposure temperature is the point at which a printed part will begin to deform. Above this temperature, your part will start to lose structural integrity.
Spool | ||||||||||||
---|---|---|---|---|---|---|---|---|---|---|---|---|
Dia., mm | Printing Temp. | For Printer Bed Temp. | Tensile Strength | Annealing Temp. | Maximum Exposure Temperature | Specifications Met | For Min. Nozzle Opening Dia., mm | Dia., mm | Dp., mm | Wt., g | Each | |
PPSU Plastic | ||||||||||||
Off-White | ||||||||||||
1.75 | 390° to 410° C 734° to 770° F | 140° to 160° C 284° to 320° F | 7,970 psi (Good) | 80° to 130° C 176° to 266° F | 180° C 200° C | UL 94 V-0 | 0.4 | 200 | 40 | 500 | 000000 | 0000000 |