Air-Powered Grippers

Combine these grippers with your gripping fingers to lift and move items in pick-and-place applications.
Circular grippers are best for a snug grip on round objects.
Grippers with a forced-air jaw return have two air ports: one to move the jaws open and another to move them closed. The jaws grip items from the outside as well as the inside.
Grippers with steel jaws are harder and stronger than aluminum. Note: Choose a gripper with a holding force at least 10 times your item's weight.
Warning: Never use to lift people or items over people.

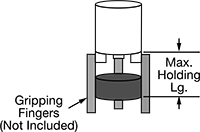
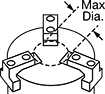

Dia., mm | O'all | Port | |||||||||||||
---|---|---|---|---|---|---|---|---|---|---|---|---|---|---|---|
External Gripping Force | Internal Gripping Force | Max. Gripping Cap. | Max. | Min. | Max. Holding Lg., mm | Wt. | Lg., mm | Dia., mm | Max. Pressure, psi | Pipe Size | Thread Size | Thread Type | Manufacturer (Series/Model No.) | Each | |
Aluminum Housing | |||||||||||||||
3.15 lbs. @ 72.5 psi | 3.6 lbs. @ 72.5 psi | 0.24 lbs./ 0.1 kg | 14 | 10 | 29 | 0.14 lbs./ 0.06 kg | 35 | 30 | 85 | __ | M3 × 0.5 | Metric | SMC (MHS3 16) | 0000000 | 0000000 |
5.62 lbs. @ 72.5 psi | 6.29 lbs. @ 72.5 psi | 0.43 lbs./ 0.19 kg | 16 | 12 | 35 | 0.23 lbs./ 0.1 kg | 38 | 36 | 85 | __ | M5 × 0.8 | Metric | SMC (MHS3 20) | 0000000 | 000000 |
9.44 lbs. @ 72.5 psi | 10.57 lbs. @ 72.5 psi | 0.72 lbs./ 0.32 kg | 20 | 14 | 39 | 0.31 lbs./ 0.14 kg | 40 | 42 | 85 | __ | M5 × 0.8 | Metric | SMC (MHS3 25) | 0000000 | 000000 |
57 lbs. @ 85 psi | 60 lbs. @ 85 psi | 2.75 lbs./ 1.25 kg | 21 | 16 | 50 | 0.26 lbs./ 0.12 kg | 27 | 56 | 115 | __ | M3 × 0.5 | Metric | Schunk (JGZ 40) | 0000000 | 000000 |
73 lbs. @ 85 psi | 79 lbs. @ 85 psi | 3.52 lbs./ 1.6 kg | 28 | 20 | 64 | 0.55 lbs./ 0.25 kg | 34 | 72 | 115 | __ | M5 × 0.8 | Metric | Schunk (JGZ 50) | 0000000 | 000000 |
130 lbs. @ 85 psi | 140 lbs. @ 85 psi | 6.39 lbs./ 2.9 kg | 32 | 20 | 80 | 0.94 lbs./ 0.43 kg | 43 | 87 | 115 | __ | M5 × 0.8 | Metric | Schunk (JGZ 64) | 0000000 | 000000 |
220 lbs. @ 85 psi | 240 lbs. @ 85 psi | 11.02 lbs./ 5 kg | 42 | 26 | 100 | 1.74 lbs./ 0.79 kg | 49 | 111 | 115 | __ | M5 × 0.8 | Metric | Schunk (JGZ 80) | 0000000 | 000000 |
400 lbs. @ 85 psi | 430 lbs. @ 85 psi | 19.84 lbs./ 9 kg | 52 | 32 | 125 | 3.1 lbs./ 1.41 kg | 59 | 135 | 115 | 1/8 | __ | BSPP | Schunk (JGZ 100) | 0000000 | 000000 |
690 lbs. @ 85 psi | 740 lbs. @ 85 psi | 34.17 lbs./ 15.5 kg | 66 | 40 | 160 | 6.1 lbs./ 2.8 kg | 67 | 166 | 115 | 1/8 | __ | BSPP | Schunk (JGZ 125) | 0000000 | 00000000 |
1,340 lbs. @ 85 psi | 1,430 lbs. @ 85 psi | 66.13 lbs./ 30 kg | 82 | 50 | 200 | 12.3 lbs./ 5.6 kg | 81 | 212 | 115 | 1/8 | __ | BSPP | Schunk (JGZ 160) | 0000000 | 00000000 |
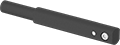
Add optional sensors to your gripper to signal when fingers are either open or closed (open and closed for sensors with two-position detection), and use that information to trigger other actions in your system. Since they’re magnetic, they detect the finger position using magnets placed on the piston.
Sensors with a plug connection work with the input/output on robot tool mounts with a power/signal block. Sensors with a hardwire connection have wire leads you either wire to a plug or hardwire to a power source.
NPN sensors communicate proximity with a negative signal, while PNP sensors send a positive signal.
Sensors with two-position detection send a signal when the fingers open and close, so you can trigger actions in your system based on both signals.
For Manufacturer (Series) | Signal Output Type | No. of Sensing Positions | Plug Type | No. of Wire Leads | Current, mA | Voltage | Switch Starting Position | Each | |
Magnetic with Plug Connection | |||||||||
---|---|---|---|---|---|---|---|---|---|
Schunk (DPG+, DPZ+, DRG, JGP, JGP-P, JGZ, KGG, MPG+, PGN+E) | NPN | 1 | 3-Pin M8 | __ | 50 | 24V DC | 1 Off (Normally Open) | 00000000 | 0000000 |
Schunk (DPG+, DPZ+, DRG, JGP, JGP-P, JGZ, KGG, MPG+, PGN+E) | PNP | 1 | 3-Pin M8 | __ | 50 | 24V DC | 1 Off (Normally Open) | 0000000 | 000000 |
Schunk (DPG+, DPZ+, DRG, JGP, JGP-P, JGZ, KGG, MPG+, PGN+E) | PNP | 2 | 4-Pin M8 | __ | 100 | 24V DC | 1 Off (Normally Open) and 1 On (Normally Closed) | 00000000 | 000000 |
Magnetic with Hardwire Connection | |||||||||
Schunk (DPG+, DPZ+, DRG, JGP, JGP-P, JGZ, KGG, MPG+, PGN+E) | NPN | 1 | __ | 3 | 50 | 24V DC | 1 Off (Normally Open) | 00000000 | 000000 |
Schunk (DPG+, DPZ+, DRG, JGP, JGP-P, JGZ, KGG, MPG+, PGN+E) | PNP | 1 | __ | 3 | 50 | 24V DC | 1 Off (Normally Open) | 00000000 | 000000 |
Schunk (DPG+, DPZ+, DRG, JGP, JGP-P, JGZ, KGG, MPG+, PGN+E) | PNP | 2 | __ | 4 | 100 | 24V DC | 1 Off (Normally Open) and 1 On (Normally Closed) | 00000000 | 000000 |
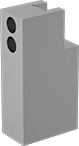
Finger blanks come ready to mount, so you can make custom fingers without starting from scratch. Just machine the blank’s gripping end to create fingers that will securely grip your specific parts.
When used in pairs, individual blanks have a symmetrical design that’s suitable for most applications.
Aluminum blanks are lightweight and resist rusting in wet environments. They’re softer than steel blanks, making them easier to machine and less likely to scratch your parts.
Steel blanks are stronger and more durable than aluminum blanks, so they’re less likely to break if they hit a nearby object. You can harden them for even more strength and durability.
For Gripper Jaw | Overall | |||||||
---|---|---|---|---|---|---|---|---|
For Manufacturer (Series/Model No.) | Wd., mm | Dp., mm | Lg., mm | Wd., mm | Dp., mm | Mounting Hardware Included | Each | |
Aluminum | ||||||||
Schunk (JGP, JGP-P, JGZ, PGN+, PGN+E, PGN+P, PZN+ 64) | 21 | 12.5 | 64 | 32 | 22 | Yes | 00000000 | 000000 |
Schunk (JGP, JGP-P, JGZ, PGN+, PGN+E, PGN+P, PZN+ 80) | 26 | 15 | 80 | 41 | 22 | Yes | 00000000 | 00000 |
Schunk (JGP, JGP-P, JGZ, PGN+, PGN+E, PGN+P, PZN+ 100) | 33 | 18.5 | 100 | 52 | 30 | Yes | 00000000 | 000000 |
Steel | ||||||||
Schunk (JGP, JGP-P, JGZ, PGN+, PGN+E, PGN+P, PZN+ 64) | 21 | 12.5 | 64 | 32 | 22 | Yes | 00000000 | 00000 |
Schunk (JGP, JGP-P, JGZ, PGN+, PGN+E, PGN+P, PZN+ 80) | 26 | 15 | 80 | 41 | 22 | Yes | 00000000 | 000000 |
Schunk (JGP, JGP-P, JGZ, PGN+, PGN+E, PGN+P, PZN+ 100) | 33 | 18.5 | 100 | 52 | 30 | Yes | 00000000 | 000000 |
![]() | ![]() Adjustable Finger Mount |
![]() Scale |
Attach adjustable finger mounts to your Schunk grippers, so they can handle a wider range of part sizes and shapes. Each mount has a positioning slide that moves along a rail, which has a scale for making adjustments. Connect your fingers to the slides, position them on the rail, and tighten the knob to secure them in place. Use one mount for as many fingers as your gripper will hold.
Gripper | Finger | ||||||||||||
---|---|---|---|---|---|---|---|---|---|---|---|---|---|
For Manufacturer (Series/Model No.) | Manufacturer (Series/Model No.) | Rail Lg., mm | Travel Lg., mm | Carriage Wd., mm | O'all Ht., mm | Adjustment Increments (Lg.), mm | Bolt Hole Thread Size | No. of Bolt Holes | Bolt Hole Thread Size | No. of Bolt Holes | Mounting Fasteners Included | Each | |
Anodized Aluminum | |||||||||||||
With Nonremovable Positioning Slides | |||||||||||||
Schunk (JGP, JGP-P, JGZ, PGN+, PGN+E, PGN+P, PZN+ 64) | Schunk (UZB 64) | 63.5 | 33 | 36 | 36 | 2 | M4 × 0.7 mm | 2 | M4 × 0.7 mm | 2 | No | 00000000 | 0000000 |
With Removable Positioning Slides | |||||||||||||
Schunk (JGP, JGP-P, JGZ, PGN+, PGN+E, PGN+P, PZN+ 125) | Schunk (UZB 125) | 112.75 | 72 | 52 | 49 | 3 | M6 × 1 mm | 2 | M6 × 1 mm | 2 | No | 00000000 | 000000 |
Schunk (JGP, JGP-P, JGZ, PGN+, PGN+E, PGN+P, PZN+ 80) | Schunk (UZB 80) | 79 | 44 | 42 | 39.5 | 2 | M5 × 0.8 mm | 2 | M5 × 0.8 mm | 2 | No | 00000000 | 000000 |
Schunk (JGP, JGP-P, JGZ, PGN+, PGN+E, PGN+P, PZN+ 100) | Schunk (UZB 100) | 96.5 | 55 | 47 | 45.5 | 3 | M6 × 1 mm | 2 | M6 × 1 mm | 2 | No | 00000000 | 000000 |
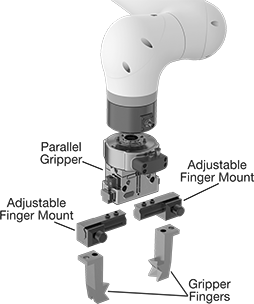
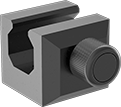
Removable positioning slides are part of the adjustable finger mounts. Add additional slides for tasks that require frequent finger changes. Having slides on hand with fingers already attached, makes it quick and easy to retool your gripper.
Clean Room Air-Powered Grippers

Lift and move items in pick-and-place operations where small particles could damage sensitive electronics. To limit contamination, these grippers have a port you can connect to a vacuum pump to capture particles. Use them with gripping fingers to grab items. They use forced air to move the jaws: one air port pushes them open and another closes them.
Circular grippers are best for a snug grip on round objects.

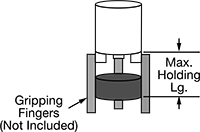
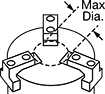

Dia. | O'all | Port | ||||||||||||||
---|---|---|---|---|---|---|---|---|---|---|---|---|---|---|---|---|
External Gripping Force | Internal Gripping Force | Max. Gripping Cap. | Max., mm | Min., mm | Max. Holding Lg., mm | Wt. | Lg., mm | Dia., mm | Max. Pressure, psi | Pipe Size | Thread Size | Thread Type | Manufacturer (Series/Model No.) | Each | ||
Aluminum Housing—IP54, ISO Class 5 | ||||||||||||||||
D | 51 lbs. @ 85 psi | 56 lbs. @ 85 psi | 2.53 lbs. / 1.15 kg | 68 | 63 | 40 | 0.44 lbs./ 0.2 kg | 34 | 68 | 115 | __ | M3 × 0.5 | Metric | Schunk (DPZ+ 40) | 0000000 | 000000000 |
D | 65 lbs. @ 85 psi | 71 lbs. @ 85 psi | 3.19 lbs. / 1.45 kg | 89 | 81 | 50 | 0.81 lbs./ 0.37 kg | 40 | 89 | 115 | __ | M5 × 0.8 | Metric | Schunk (DPZ+ 50) | 0000000 | 00000000 |
D | 115 lbs. @ 85 psi | 135 lbs. @ 85 psi | 5.73 lbs. / 2.6 kg | 106 | 94 | 64 | 1.36 lbs./ 0.62 kg | 49 | 106 | 115 | __ | M5 × 0.8 | Metric | Schunk (DPZ+ 64) | 0000000 | 00000000 |
D | 200 lbs. @ 85 psi | 220 lbs. @ 85 psi | 9.92 lbs. / 4.5 kg | 128 | 112 | 80 | 2.86 lbs./ 1.3 kg | 56 | 128 | 115 | __ | M5 × 0.8 | Metric | Schunk (DPZ+ 80) | 0000000 | 00000000 |
D | 360 lbs. @ 85 psi | 430 lbs. @ 85 psi | 17.85 lbs. / 8.1 kg | 158 | 138 | 100 | 4.18 lbs./ 1.9 kg | 67 | 158 | 115 | 1/8 | __ | BSPP | Schunk (DPZ+ 100) | 0000000 | 00000000 |
D | 660 lbs. @ 85 psi | 670 lbs. @ 85 psi | 32.4 lbs. / 14.7 kg | 198 | 172 | 125 | 7.7 lbs./ 3.5 kg | 76 | 198 | 115 | 1/8 | __ | BSPP | Schunk (DPZ+ 125) | 0000000 | 00000000 |
D | 1,280 lbs. @ 85 psi | 1,320 lbs. @ 85 psi | 62.83 lbs. / 28.5 kg | 271 | 239 | 125 | 17.4 lbs./ 7.9 kg | 93 | 271 | 115 | 1/8 | __ | BSPP | Schunk (DPZ+ 160) | 0000000 | 00000000 |
D | 1,510 lbs. @ 85 psi | 1,600 lbs. @ 85 psi | 73.85 lbs. / 33.5 kg | 345 | 295 | 160 | 34.3 lbs./ 15.6 kg | 111 | 345 | 115 | 1/8 | __ | BSPP | Schunk (DPZ+ 200) | 0000000 | 00000000 |
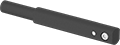
For Manufacturer (Series) | Signal Output Type | No. of Sensing Positions | Plug Type | No. of Wire Leads | Current, mA | Voltage | Switch Starting Position | Each | |
Magnetic with Plug Connection | |||||||||
---|---|---|---|---|---|---|---|---|---|
Schunk (DPG+, DPZ+, DRG, JGP, JGP-P, JGZ, KGG, MPG+, PGN+E) | NPN | 1 | 3-Pin M8 | __ | 50 | 24V DC | 1 Off (Normally Open) | 00000000 | 0000000 |
Schunk (DPG+, DPZ+, DRG, JGP, JGP-P, JGZ, KGG, MPG+, PGN+E) | PNP | 1 | 3-Pin M8 | __ | 50 | 24V DC | 1 Off (Normally Open) | 0000000 | 000000 |
Schunk (DPG+, DPZ+, DRG, JGP, JGP-P, JGZ, KGG, MPG+, PGN+E) | PNP | 2 | 4-Pin M8 | __ | 100 | 24V DC | 1 Off (Normally Open) and 1 On (Normally Closed) | 00000000 | 000000 |
Magnetic with Hardwire Connection | |||||||||
Schunk (DPG+, DPZ+, DRG, JGP, JGP-P, JGZ, KGG, MPG+, PGN+E) | NPN | 1 | __ | 3 | 50 | 24V DC | 1 Off (Normally Open) | 00000000 | 000000 |
Schunk (DPG+, DPZ+, DRG, JGP, JGP-P, JGZ, KGG, MPG+, PGN+E) | PNP | 1 | __ | 3 | 50 | 24V DC | 1 Off (Normally Open) | 00000000 | 000000 |
Schunk (DPG+, DPZ+, DRG, JGP, JGP-P, JGZ, KGG, MPG+, PGN+E) | PNP | 2 | __ | 4 | 100 | 24V DC | 1 Off (Normally Open) and 1 On (Normally Closed) | 00000000 | 000000 |