About Structural Adhesives
More
About Paint and Protective Coatings
More
Low-Friction Epoxy Coatings
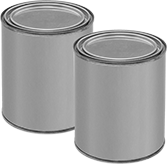
Use these coatings on tanks to create a low-friction lining that prevents bubble formation and turbulence in the liquids within. These thick coatings can also be used in chutes and on foundations for a smooth, glossy surface that resists abrasion, chemicals, and extreme temperatures once cured. Apply with a brush or roller. The size listed is the combined total of the two parts.
Dry Time | ||||||||||||
---|---|---|---|---|---|---|---|---|---|---|---|---|
Mfr. Model Name | Mfr. Model No. | Container Size, gal. | Composition | Touch, hrs. | O'all, hrs. | Approximate Coverage @ Thickness | Application Time After Mixing, min. | Application Temp. Range, °F | For Use On | Color (Appearance) | Each | |
Loctite® Coatings | ||||||||||||
Nordbak Chemical Resistant Coating | PC 7319 | 1 1/2 | Solvent Based | 4 | 16 | 150 sq. ft. @ 10 mil | 25 | 65° to 80° | Aluminum, Brass, Bronze, Copper, Steel, Stainless Steel, Galvanized Iron, Galvanized Steel, Plastic, Composites, Fiberglass, Ceramic, Glass, Masonry, Concrete, Stone, Asphalt, Drywall, Wood | Gray (Gloss) | 000000 | 0000000 |
Impact-Resistant Polyurethane Coatings
Designed for use on hoppers, chutes, and pumps, these coatings protect against impact and abrasion. Thicker than paint, they resist UV, moisture, and chemicals. Apply with a brush, roller, or sprayer. The size listed is the combined total of the two parts.
Primers cannot be sold to Canada due to regulatory limits on VOCs (volatile organic compounds).
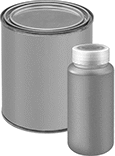
Dry Time | |||||||||||||
---|---|---|---|---|---|---|---|---|---|---|---|---|---|
Container Size, fl. oz. | Composition | Touch, hrs. | O'all, hrs. | Approximate Coverage @ Thickness | Mix Ratio | Application Time After Mixing, min. | Max. Temp., °F | Application Temp. Range, °F | For Use On | Primer Required For Use On | Color (Appearance) | Each | |
14 | Solvent Based | 10 | 16 | 3 sq. ft. @ 50 mil | 77:23 | 30 | 180° | 65° to 85° | Steel, Iron, Plastic, Rubber, Composites, Fiberglass, Concrete, Wood | Steel, Iron, Plastic, Rubber, Composites, Fiberglass, Concrete, Wood | Black (Gloss) | 0000000 | 0000000 |
Dry Time | |||||||||||
---|---|---|---|---|---|---|---|---|---|---|---|
Container Size, fl. oz. | Composition | Touch, min. | O'all, min. | Approximate Coverage @ Thickness | Max. Temp., °F | Application Temp. Range, °F | For Use On | Color (Appearance) | Cannot Be Sold To | Each | |
4 | Solvent Based | 30 | 30 | 10 sq. ft. @ 50 mil | 170° | 25° to 170° | Steel, Iron | Blue (Gloss) | Canada | 0000000 | 000000 |
4 | Solvent Based | 30 | 30 | 10 sq. ft. @ 50 mil | 195° | 55° to 195° | Plastic, Rubber, Composites, Concrete, Wood, Fiberglass | Orange (Gloss) | Canada | 0000000 | 00000 |
Flexible Chemical-Resistant Coatings
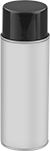
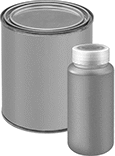
Made with Viton® fluoroelastomer, use these coatings to create a flexible coating on rollers, heavy equipment, and anything else that’s exposed to corrosive chemicals or extreme temperatures. Coatings resist acids, alkalies, fuels, and solvents, as well as temperatures as low as -40° F once cured. They can also be used as an adhesive for Viton® gaskets, O-rings, and seals.
Apply coatings in a bottle and can with a brush or roller. The size listed is the combined total of the two parts.
Container | Dry Time | ||||||||||||
---|---|---|---|---|---|---|---|---|---|---|---|---|---|
Size, qt. | Net Weight, oz. | Composition | Touch, min. | O'all, hrs. | Approximate Coverage @ Thickness | Mix Ratio | Application Time After Mixing, hrs. | Max. Temp., °F | Application Temp. Range, °F | For Use On | Color (Appearance) | Each | |
Viton® Fluoroelastomer—Aerosol Can | |||||||||||||
__ | 12 | Solvent Based | 10 | 24 | 13 sq. ft. @ 1 mil | __ | __ | 400° | 60° to 90° | Aluminum, Brass, Bronze, Copper, Steel, Stainless Steel, Galvanized Iron, Galvanized Steel, Plastic, Rubber, Composites, Fiberglass, Ceramic, Glass, Masonry, Concrete, Stone, Asphalt, Drywall, Wood | Black (Flat) | 000000 | 000000 |
Viton® Fluoroelastomer—Bottle and Can | |||||||||||||
1 | __ | Solvent Based | 10 | 24 | 70 sq. ft. @ 1 mil | 27:1 | 8 | 400° | 40° to 90° | Aluminum, Brass, Bronze, Copper, Steel, Stainless Steel, Galvanized Iron, Galvanized Steel, Plastic, Rubber, Composites, Fiberglass, Ceramic, Glass, Masonry, Concrete, Stone, Asphalt, Drywall, Wood | Black (Flat) | 000000 | 000000 |
Flame-Retardant Coatings
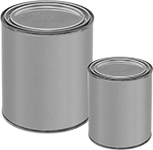
Use these coatings in kitchens, furnace areas, and ships on plastic, metal, wood, and masonry. Apply with a brush, roller, or sprayer. The size listed is the combined total of the two parts.
Clear coatings are frequently used on wood—use one coat on sealed wood and two on unsealed. They can be used outside without breaking down, but prolonged exposure to UV light may cause them to yellow.
White coatings are frequently used on walls, ceilings, doors, and stairwells.
Dry Time | |||||||||||||
---|---|---|---|---|---|---|---|---|---|---|---|---|---|
Container Size, gal. | Composition | Touch, hrs. | O'all, hrs. | Approximate Coverage @ Thickness | Mix Ratio | Application Time After Mixing, hrs. | Max. Temp., °F | Application Temp. Range, °F | Flammability Rating | For Use On | Color (Appearance) | Each | |
Epoxy | |||||||||||||
1 | Water Based | 8 | 48 | 150 sq. ft. @ 10 mil | 100:26 | 2.5 | 250° | 40° to 100° | UL 94 V-0 | Aluminum, Copper, Steel, Stainless Steel, Galvanized Iron, Galvanized Steel, Plastic, Rubber, Composites, Fiberglass, Ceramic, Glass, Masonry, Concrete, Stone, Asphalt, Drywall, Wood | Clear (Gloss) | 000000 | 0000000 |
1 | Water Based | 8 | 48 | 150 sq. ft. @ 10 mil | 100:20 | 2.5 | 300° | 40° to 100° | UL 94 V-0 | Aluminum, Copper, Steel, Stainless Steel, Galvanized Iron, Galvanized Steel, Plastic, Rubber, Composites, Fiberglass, Ceramic, Glass, Masonry, Concrete, Stone, Asphalt, Drywall, Wood | White (Gloss) | 000000 | 000000 |
Flexible Rubber Coatings for Metal
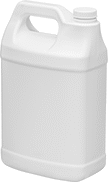
These flexible, slip-resistant silicone coatings resist chemicals, block UV light, and encapsulate lead paint. They withstand temperatures up to 320° F. Apply with a brush, roller, or sprayer.
Dry Time | ||||||||||
---|---|---|---|---|---|---|---|---|---|---|
Container Size, gal. | Composition | Touch, min. | O'all, hrs. | Approximate Coverage @ Thickness | Max. Temp., °F | Application Temp. Range, °F | For Use On | Choose a Color (Appearance) | Each | |
Silicone | ||||||||||
1 | Solvent Based | 60 | 24 | 100 sq. ft. @ 10 mil | 320° | 40° to 80° | Steel, Iron, Composites, Wood | 000000 | 0000000 |
Ready-to-Use Silicone Potting Compounds
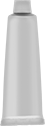
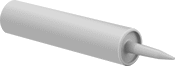
No mixing required—these potting compounds come ready to apply. Use them to encase electronic assemblies for protection from dust, moisture, mechanical shock, and vibration. Softer and more flexible than epoxies and urethanes with the widest temperature range, silicone potting compounds are the best choice for high-temperature applications and electronics exposed to thermal cycling. They have good moisture resistance but poor chemical and abrasion resistance. Silicones provide excellent electrical insulation. They're also known as RTV (room-temperature vulcanizing) compounds because they don’t need heat or UV light to cure.
Container | Dry Time | |||||||||||||
---|---|---|---|---|---|---|---|---|---|---|---|---|---|---|
Mfr. Model No. | Size, fl. oz. | Type | Consistency | Touch | Overall, hrs. | Dielectric Strength, V/mil | Thermal Conductivity, W/m-K | Temp. Range, °F | Specifications Met | For Use On | Color | Clarity | Each | |
Dow Corning Compounds—Soft | ||||||||||||||
748 | 3 | Tube | Paste | 30 min. | 24 | 475 | Not Rated | -65° to 350° | UL 94 HB | Aluminum, Brass, Bronze, Copper, Steel, Stainless Steel, Titanium, Plastic, Rubber, Composites, Fiberglass, Glass | Off-White | Opaque | 000000000 | 000000 |
748 | 10.1 | Cartridge | Paste | 30 min. | 24 | 475 | Not Rated | -65° to 350° | UL 94 HB | Aluminum, Brass, Bronze, Copper, Steel, Stainless Steel, Titanium, Plastic, Rubber, Composites, Fiberglass, Glass | Off-White | Opaque | 000000000 | 00000 |
838 | 3 | Tube | Paste | 45 min. | 24 | Not Rated | Not Rated | -45° to 390° | UL Listed, UL Recognized Component, UL 94 HB | Aluminum, Brass, Bronze, Copper, Steel, Stainless Steel, Titanium, Plastic, Rubber, Composites, Fiberglass, Ceramic, Glass | White | Opaque | 0000000 | 00000 |
839 | 10.3 | Cartridge | Paste | 35 min. | 24 | Not Rated | Not Rated | -45° to 390° | __ | Aluminum, Brass, Bronze, Copper, Steel, Stainless Steel, Titanium, Plastic, Rubber, Composites, Fiberglass, Ceramic, Glass | Blue | Semi-Clear | 0000000 | 00000 |
Optically Clear Two-Part Silicone Potting Compounds
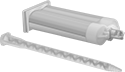
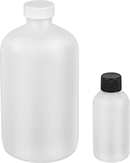
Clear enough to read through, these UV-resistant potting compounds allow optimal light transmission for use with LEDs, solar cells, and fiber optics. Use them to encase electronic assemblies for protection from dust, moisture, mechanical shock, and vibration. Softer and more flexible than epoxies and urethanes with the widest temperature range, these silicone compounds are the best choice for high-temperature applications and electronics exposed to thermal cycling. They have excellent electrical insulation and good moisture resistance but poor chemical and abrasion resistance. Also known as RTV (room-temperature vulcanizing).
Compounds in a cartridge come with a mixer nozzle for precise application. You need a gun (sold separately) to dispense.
Compounds in a bottle are easy to apply in high volumes. Just mix and pour them over components inside containers, such as potting boxes.
Liquid compounds harden around your component to form a strong, durable, and permanent layer of protection.
Gel compounds form a soft and flexible layer of protection. You can also remove them if you need to re-access your components. They are rated IP68 once potted, so they seal out water even if submersed.
Container | Dry Time | |||||||||||||
---|---|---|---|---|---|---|---|---|---|---|---|---|---|---|
Mfr. Model No. | Size | Type | Consistency | Touch, min. | Overall, min. | Dielectric Strength, V/mil | Thermal Conductivity, W/m-K | Temp. Range, °F | Environmental Rating | Certificate | For Use On | Color | Each | |
Loctite® Compounds—Soft | ||||||||||||||
5620 | 13.5 fl. oz. | Cartridge | Thin Liquid | 20 | 30 | 530 | 0.16 | -65° to 390° | __ | Material Certificate with Traceable Lot Number and Product Shelf Life | Aluminum, Brass, Bronze, Copper, Steel, Stainless Steel, Silver, Titanium, Plastic, Composites, Fiberglass | Clear | 00000000 | 0000000 |
Momentive Compounds—Medium Soft | ||||||||||||||
RTV615 | 1 lbs. | Bottle | Thick Liquid | 60 | 60 | 500 | 0.19 | -75° to 400° | __ | __ | Aluminum, Brass, Bronze, Copper, Steel, Stainless Steel, Silver, Titanium, Plastic, Composites, Fiberglass | Clear | 00000000 | 000000 |
Compounds | ||||||||||||||
__ | 10.1 fl. oz. | Bottle | Gel | 15 | 15 | 500 | 0.2 | -75° to 355° | IP68 | __ | Aluminum, Brass, Bronze, Copper, Steel, Stainless Steel, Silver, Titanium, Plastic, Composites, Fiberglass | Clear | 00000000 | 00000 |
Reusable Silicone Potting Compounds
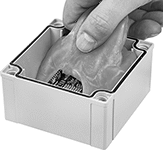
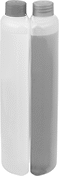
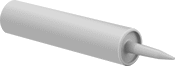
Make repairs or changes to electrical components after they’ve been potted. While most compounds are permanent, these form a gel that bonds to itself, so you can peel it off without damaging your equipment. Often used in junction boxes, they form a water- and dust-proof seal that’s rated IP68 while also providing excellent electrical insulation. Made of silicone, they withstand a wide range of temperatures and are soft and flexible enough to resist shock and vibration. However, they’re not as strong as permanent potting compounds, so they don’t resist scrapes as well as those made of epoxy and urethane. They’re also not as chemical resistant as epoxy and urethane compounds.
These compounds won’t solidify once you open the container, so you have time to make adjustments when applying them. When removing them from your components, they mostly come off in one piece but there might be some residue left over.
Bottle compounds are a better choice for filling up new enclosures than cartridge compounds because you can pour more in at a time. They have a compartment for each component and require mixing.
Cartridge compounds have a nozzle for precise application. The nozzle can also fit into junction box knockouts, so it’s easier to fill up installed enclosures than it is with bottle compounds. They come ready to use with no mixing required and no waiting time.
Dry Time | |||||||||||||
---|---|---|---|---|---|---|---|---|---|---|---|---|---|
Container Size, fl. oz. | Consistency | Touch, min. | Overall, min. | Mix Ratio | Dielectric Strength, V/mil | Thermal Conductivity, W/m-K | Temp. Range, °F | Environmental Rating | For Use On | Color | Clarity | Each | |
Bottle Compounds | |||||||||||||
8.4 | Gel | 15 | 15 | 1:1 | 500 | 0.2 | -75° to 390° | IP68 | Aluminum, Brass, Bronze, Copper, Steel, Stainless Steel, Titanium, Fiberglass, Ceramic, Glass, Composites, Plastic, Rubber | Blue | Semi Clear | 0000000 | 000000 |
33.8 | Gel | 15 | 15 | 1:1 | 500 | 0.2 | -75° to 390° | IP68 | Aluminum, Brass, Bronze, Copper, Steel, Stainless Steel, Titanium, Fiberglass, Ceramic, Glass, Composites, Plastic, Rubber | Blue | Semi Clear | 0000000 | 00000 |
Cartridge Compounds | |||||||||||||
9.4 | Gel | __ | __ | __ | 500 | 0.2 | -75° to 390° | IP68 | Aluminum, Brass, Bronze, Copper, Steel, Stainless Steel, Titanium, Fiberglass, Ceramic, Glass, Composites, Plastic, Rubber | Clear | Clear | 0000000 | 00000 |
Light-Activated Silicone Potting Compounds
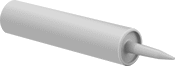
These compounds dry quickly when exposed to UV light allowing you to handle the potted items sooner. Made of silicone, they’re softer and more flexible than epoxy or urethane compounds, so they’re better at protecting against shocks and vibration. They also withstand a wider range of temperatures, so they’re often used with electronics that heat and cool rapidly. These compounds are excellent electrical insulators, and they’ll shield your components from moisture and dust. However, they don’t hold up well to abrasion or chemicals. The tapered nozzle lets you apply them precisely.
Dry Time | ||||||||||||||
---|---|---|---|---|---|---|---|---|---|---|---|---|---|---|
Mfr. Model No. | Container Size, fl. oz. | Consistency | Touch, sec. | Overall, hrs. | Light Intensity Requirements to Reach Full Strength | Cure Type | Dielectric Strength, V/mil | Thermal Conductivity | Temp. Range, °F | Specifications Met | For Use On | Color | Each | |
Loctite® Compounds—Soft | ||||||||||||||
5091 | 10 1/10 | Thick Liquid | 20 | 24 | 60 sec. per side @ 40 mW/cm2 | UV Light | 450 | Not Rated | -65° to 350° | UL Recognized Component | Aluminum, Brass, Bronze, Copper, Steel, Stainless Steel, Titanium, Fiberglass, Composites, Plastic, Silver | White | 0000000 | 0000000 |
Heat-Transfer Epoxy Potting Compounds
Formulated to draw heat away from sensitive electronic components, these potting compounds have higher thermal conductivity than standard potting compounds. Use them to encase electronic assemblies for protection from dust, chemicals, moisture, mechanical shock, and vibration. Rigid and wear resistant, epoxies are the strongest of the potting compounds. They have excellent chemical and moisture resistance, withstand a wide range of temperatures, and provide excellent electrical insulation.
Cartridge potting compound requires a gun and mixer nozzle (each sold separately) to dispense.
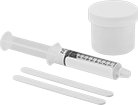
Dry Time | |||||||||||
---|---|---|---|---|---|---|---|---|---|---|---|
Container Size, fl. oz. | Consistency | Touch | Overall, hrs. | Dielectric Strength, V/mil | Thermal Conductivity, W/m-K | Max. Temp., °F | Heating Requirements to Reach Full Strength | For Use On | Color | Each | |
0.9 | Thick Liquid | 25 min. | 24 | 450 | 1.87 | 500° | 1 hr. @ 250° F then 1 hr. @ 350° F | Aluminum, Brass, Bronze, Copper, Steel, Stainless Steel, Cast Iron, Iron, Silver, Titanium, Plastic, Composites, Ceramic, Glass | Black | 0000000 | 000000 |
1 | Gel | 4 hrs. | 6 | Not Rated | 1.87 | 600° | 4 hrs. @ 250° F then 2 hrs. @ 350° F | Aluminum, Brass, Bronze, Copper, Steel, Stainless Steel, Cast Iron, Iron, Silver, Titanium, Plastic, Composites, Ceramic, Glass | Black | 0000000 | 00000 |
1.5 | Thin Liquid | 30 min. | 26 | 450 | 0.21 | 500° | 1 hr. @ 250° F then 1 hr. @ 350° F | Aluminum, Brass, Bronze, Copper, Steel, Stainless Steel, Cast Iron, Iron, Silver, Titanium, Plastic, Composites, Ceramic, Glass | Amber | 0000000 | 00000 |
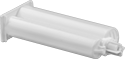
Dry Time | ||||||||||
---|---|---|---|---|---|---|---|---|---|---|
Container Size, fl. oz. | Consistency | Touch, min. | Overall, hrs. | Dielectric Strength, V/mil | Thermal Conductivity, W/m-K | Temp. Range, °F | For Use On | Color | Each | |
1.7 | Thick Liquid | 15 | 8 | 520 | 1.01 | -40° to 210° | Aluminum, Brass, Bronze, Copper, Steel, Stainless Steel, Silver, Titanium, Plastic, Composites, Fiberglass | Black | 0000000 | 000000 |
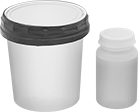
Dry Time | |||||||||||
---|---|---|---|---|---|---|---|---|---|---|---|
Container Size, fl. oz. | Consistency | Touch | Overall, hrs. | Dielectric Strength, V/mil | Thermal Conductivity, W/m-K | Max. Temp., °F | Heating Requirements to Reach Full Strength | For Use On | Color | Each | |
16 | Thin Liquid | 30 min. | 26 | 450 | 0.21 | 500° | 1 hr. @ 250° F then 1 hr. @ 350° F | Aluminum, Brass, Bronze, Copper, Steel, Stainless Steel, Cast Iron, Iron, Silver, Titanium, Plastic, Composites, Ceramic, Glass | Amber | 0000000 | 0000000 |
High-Temperature Epoxy Potting Compounds
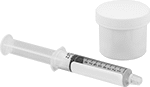
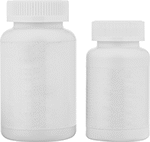
Protect circuit boards and other electronics where high heat is a concern but you don’t need to transfer that heat elsewhere. These compounds are a good middle ground between standard epoxy compounds and heat-transfer compounds. They work at temperatures twice as high as standard epoxy compounds. However, they don't conduct heat as well as heat-transfer compounds so they're not the best choice for circuit boards that run for long periods of time. Harden these compounds at room temperature—they don’t require an oven to harden like heat-transfer compounds do.
Since they’re an epoxy compound, they won’t break down from chemicals or moisture. They’re also excellent electrical insulators and withstand a wide range of temperatures. Use them to shield components from dust, moisture, chemicals, mechanical shock, and vibration.
Jar and syringe compounds are the consistency of honey once they’re mixed, so they’ll seep into the crevices of a circuit board and encapsulate intricate components. Use the syringe for precise application.
Bottle compounds are easier to apply in higher volumes than jar and syringe compounds. Mix them together and pour them over components inside containers, such as a potting box. If air bubbles occur after mixing, you can put the mixture in a vacuum chamber to remove them. They cannot be sold to Canada due to product labeling requirements.
Dry Time | |||||||||||
---|---|---|---|---|---|---|---|---|---|---|---|
Container Size, fl. oz. | Consistency | Viscosity, cP | Touch | Overall, hrs. | Dielectric Strength, V/mil | Thermal Conductivity, W/m-K | Max. Temp., °F | For Use On | Cannot Be Sold To | Each | |
Jar and Syringe Compounds—Extra Hard | |||||||||||
1 | Thick Liquid | 3,600 | 12 hrs. | 24 | 450 | 0.22 | 500° | Aluminum, Brass, Bronze, Copper, Steel, Stainless Steel, Plastic, Rubber, Composites, Fiberglass, Ceramic, Glass | __ | 0000000 | 000000 |
Bottle Compounds—Extra Hard | |||||||||||
12.6 | Paste | 22,000 | 60 min. | 24 | 470 | 0.3 | 435° | Aluminum, Brass, Bronze, Copper, Steel, Stainless Steel, Plastic, Rubber, Composites, Fiberglass, Ceramic, Glass | Canada | 0000000 | 00000 |
Epoxy Potting Compounds
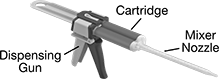
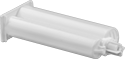
Encase electronic assemblies in a layer of epoxy for protection from dust, chemicals, moisture, mechanical shock, and vibration. The strongest of the potting compounds, epoxies are rigid and wear resistant. They have excellent chemical and moisture resistance, withstand a wide range of temperatures, and provide excellent electrical insulation. All require a mixer nozzle and gun to dispense.
Compounds that cannot be sold to Canada are restricted by product labeling requirements.
Dry Time | |||||||||||
---|---|---|---|---|---|---|---|---|---|---|---|
Mfr. Model No. | Container Size, fl. oz. | Consistency | Touch, min. | Overall, hrs. | Dielectric Strength, V/mil | Thermal Conductivity, W/m-K | Temp. Range, °F | For Use On | Color | Each | |
E-60NC | 1.7 | Thick Liquid | 60 | 24 | 550 | Not Rated | -65° to 250° | Aluminum, Brass, Bronze, Copper, Steel, Stainless Steel, Silver, Titanium, Plastic, Composites, Fiberglass | Black | 0000000 | 000000 |
E-60NC | 6.8 | Thick Liquid | 60 | 24 | 550 | Not Rated | -65° to 250° | Aluminum, Brass, Bronze, Copper, Steel, Stainless Steel, Silver, Titanium, Plastic, Composites, Fiberglass | Black | 0000000 | 00000 |
E-60NC | 13.5 | Thick Liquid | 60 | 24 | 550 | Not Rated | -65° to 250° | Aluminum, Brass, Bronze, Copper, Steel, Stainless Steel, Silver, Titanium, Plastic, Composites, Fiberglass | Black | 0000000 | 00000 |
Dispensing Gun for 1.7 fl. oz. Cartridges | 00000000 | Each | 000000 |
Mixer Nozzle for 1.7 fl. oz. E-60NC Cartridges | 00000000 | Each | 0000 |
Mixer Nozzle for 6.8 fl. oz. and 13.5 fl. oz. Cartridges | 0000000 | Each | 0000 |
Dispensing Gun for 6.8 fl. oz. Cartridges | 0000000 | Each | 000000 |
Dispensing Gun for 13.5 fl. oz. Cartridges | 0000000 | Each | 000000 |
Dry Time | |||||||||||
---|---|---|---|---|---|---|---|---|---|---|---|
Container Size, fl. oz. | Consistency | Touch, min. | Overall, hrs. | Dielectric Strength, V/mil | Thermal Conductivity, W/m-K | Temp. Range, °F | For Use On | Color | Cannot Be Sold To | Each | |
1.69 | Thick Liquid | 45 | 24 | 400 | 0.3 | -40° to 300° | Aluminum, Brass, Bronze, Copper, Steel, Stainless Steel, Silver, Plastic, Rubber, Composites, Fiberglass, Ceramic, Glass | Black | Canada | 0000000 | 000000 |
Light-Activated Epoxy Potting Compounds
Handle potted items within minutes—these potting compounds dry quickly when exposed to UV light. For added strength and durability, cure them with heat. Since they’re epoxy, they won’t break down from chemicals or moisture. They’re also excellent electrical insulators and withstand a wide range of temperatures. Use them to shield components from dust, moisture, chemicals, mechanical shock, and vibration. You need a mixer nozzle (not included) and a gun and plunger (both sold separately) to dispense. The nozzle lets you apply these compounds precisely.
For maximum effectiveness, these compounds need to be heat cured after they’re cured with UV light. Overall dry time includes heat curing at 149° F.
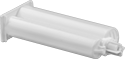
Dry Time | |||||||||||
---|---|---|---|---|---|---|---|---|---|---|---|
Mfr. Model No. | Container Size, fl. oz. | Consistency | Touch, min. | Overall, hrs. | Light Intensity Requirements to Reach Full Strength | Cure Type | Temp. Range, °F | For Use On | Color | Each | |
Loctite® Compounds—Extra Hard | |||||||||||
3336 | 1.4 | Thick Liquid | 5 | 16 | 60 seconds @ 30 mW/cm2 | UV Light | -65° to 350° | Aluminum, Brass, Bronze, Copper, Steel, Stainless Steel, Titanium, Fiberglass, Composites, Plastic, Silver | Amber | 0000000 | 000000 |
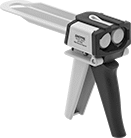
For Cartridge Size | Each | |
1.4 fl. oz. | 0000000 | 000000 |
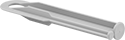
For Cartridge Size | Each | |
1.4 fl oz. | 00000000 | 00000 |
Optically Clear Epoxy Potting Compounds
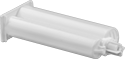
Clear enough to read through, these UV-resistant potting compounds allow optimal light transmission for use with LEDs, solar cells, and fiber optics. Use them to encase electronic assemblies for protection from dust, chemicals, moisture, mechanical shock, and vibration. Rigid and wear resistant, epoxies are the strongest of the potting compounds. They have excellent chemical and moisture resistance, withstand a wide range of temperatures, and provide excellent electrical insulation. All require a mixer nozzle and gun to dispense.
Dry Time | ||||||||||
---|---|---|---|---|---|---|---|---|---|---|
Container Size, fl. oz. | Consistency | Touch, min. | Overall, hrs. | Dielectric Strength, V/mil | Thermal Conductivity, W/m-K | Temp. Range, °F | For Use On | Color | Each | |
Optically Clear Epoxy Potting Compounds—Extra Hard | ||||||||||
1.7 | Thick Liquid | 40 | 24 | 500 | 0.24 | -65° to 275° | Aluminum, Brass, Bronze, Copper, Steel, Stainless Steel, Cast Iron, Iron, Silver, Plastic, Rubber, Composites, Fiberglass, Ceramic, Glass | Amber | 0000000 | 000000 |
Two-Part Adhesive Dispensing Guns | |||
---|---|---|---|
Dispensing Gun for 1.7 fl. oz. Cartridges | 00000000 | Each | 000000 |
Mixer Nozzles for Two-Part Adhesive Cartridges | |||
---|---|---|---|
Mixer Nozzle for 1.7 fl. oz. Cartridges | 00000000 | Each | 00000 |
Flame-Retardant Epoxy Potting Compounds
Protect circuit boards and other electronics from fire and heat. These self-extinguishing compounds meet UL 94V-0 for flame retardance and withstand temperatures up to nearly 400° F. Use them to shield components from dust, moisture, chemicals, mechanical shock, and vibration. Since they’re epoxies, they won’t break down from chemicals or moisture. They’re also excellent electrical insulators. These compounds have the consistency of honey once they’re mixed, so they seep into crevices to encase intricate components. They’re not for sale in Canada.
Cartridge compounds dispense through a mixer nozzle for precise application. Use them with a dispensing gun.
Can compounds are easier to apply in high volumes than cartridge compounds. Mix them together and pour them over components inside containers, such as a potting box. If you see air bubbles after mixing, put the mixture in a vacuum chamber to remove them.
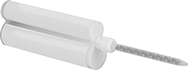
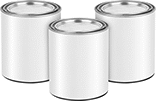
Dry Time | ||||||||||||
---|---|---|---|---|---|---|---|---|---|---|---|---|
Container Size | Consistency | Touch, hrs. | Overall, hrs. | Mixer Nozzle Included | Dielectric Strength, V/mil | Thermal Conductivity, W/m-K | Temp. Range, °F | Specifications Met | For Use On | Cannot Be Sold To | Each | |
Cartridge Compounds—Extra Hard | ||||||||||||
15.2 oz. | Thick Liquid | 2 | 48 | Yes | 395 | 0.5 | -110° to 390° | UL 94 V-0 | Aluminum, Brass, Bronze, Copper, Steel, Stainless Steel, Fiberglass, Ceramic, Glass, Composites, Plastic, Rubber, Silver | Canada | 0000000 | 000000 |
Can Compounds—Extra Hard | ||||||||||||
3 qt. | Thick Liquid | 2 | 48 | __ | 395 | 0.5 | -110° to 390° | UL 94 V-0 | Aluminum, Brass, Bronze, Copper, Steel, Stainless Steel, Fiberglass, Ceramic, Glass, Composites, Plastic, Rubber, Silver | Canada | 0000000 | 000000 |
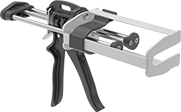
For Cartridge Size, oz. | Includes | Each | |
15.2 | Built-In Plunger for 1:1 and 2:1 Mix Ratios | 0000000 | 0000000 |
Flexible Epoxy Potting Compounds
Combine the flexibility of silicone with the durability of standard epoxy—these compounds are great for protecting sensitive electronics that need to flex or expand and contract. Because they’re an epoxy, they still have excellent moisture, chemical, and abrasion resistance. They withstand a wide range of temperatures, and this formulation won’t crack or split as components heat up and cool down. These compounds are excellent electrical insulators, and they’ll shield your components from moisture and dust. You can also use them as an adhesive since they’re also tacky.
They come in a cartridge, so you can apply them precisely. To dispense, they require a mixer nozzle and gun (both sold separately).
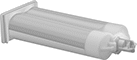
Dry Time | ||||||||
---|---|---|---|---|---|---|---|---|
Container Size, fl. oz. | Consistency | Touch, hrs. | Overall, hrs. | Hardness Rating | Temp. Range, °F | For Use On | Each | |
1.69 | Thick Liquid | 24 | 72 | Soft | -85° to 275° | Aluminum, Brass, Bronze, Copper, Steel, Stainless Steel, Titanium, Plastic, Rubber, Composites, Fiberglass, Ceramic, Glass | 0000000 | 000000 |
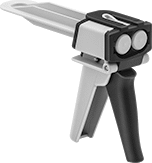
For Cartridge Size | Each | |
1.69 fl. oz. | 00000000 | 000000 |
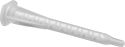
For Cartridge Size | Each | |
1.69 fl. oz. | 00000000 | 00000 |
Low-Outgassing Thermal Control Coatings
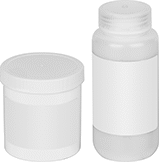
Ideal for use with sensitive electronics and optics, these coatings give off almost no volatile emissions and maintain a stable temperature. They’ve been tested to meet ASTM E595, a low-outgassing standard used by NASA. Originally developed as a coating for spacecrafts, they release internal heat and reflect external heat. Since these coatings are inorganic, you can store them at room temperature. They’ll also last longer on your equipment than organic coatings.
Dry Time | ||||||||||||||
---|---|---|---|---|---|---|---|---|---|---|---|---|---|---|
Container Net Weight, oz. | Consistency | Touch, hrs. | Overall, days | Mixing Required | Mix Ratio | Temp. Range, °F | Emissivity | Solar Absorptance | Specifications Met | For Use Outdoors | For Use On | Color | Each | |
Silicate Coatings | ||||||||||||||
16 | Thick Liquid | 48 | 7 | Yes | 1:1.1 | -295° to 2550° | 0.91 | 0.15 | ASTM E595 | Yes | Aluminum, Stainless Steel, Titanium, Gold, Silver, Nickel, Polyimide Plastic, Ceramic, Composites, Glass | White | 0000000 | 0000000 |
Harsh Environment Coatings for Electronics
High humidity, harsh chemicals, water submersions, and salt are no match for these electronic coatings. They also resist UV light, so they’ll work outdoors. Use them on circuit boards, sensors, and LED drivers in heavy machinery. Also known as conformal coatings, they’re thinner than potting compounds, so they flow into the smallest contours of your components to cover them completely.
PVDF coatings are more flexible than epoxy coatings. They’re IPC certified for use on circuit boards. You can also use them to protect against corrosion on metal joints. To apply, brush or spray them on, or dip your components in.
Epoxy coatings resist impact and wear better than PVDF coatings, and they work in higher temperatures. You can also use them as an adhesive. For controlled pouring, they’re thickened with silicate. These coatings are autoclavable, and they’ll even cure underwater. Dispense them with a mixer nozzle and a gun (each sold separately).
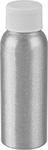
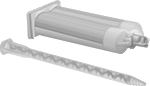
Dry Time | |||||||||||||||
---|---|---|---|---|---|---|---|---|---|---|---|---|---|---|---|
Container Size, fl. oz. | Consistency | Touch | Overall | Mixing Required | Mix Ratio | Mixer Nozzle Included | Dielectric Strength, V/mil | Thermal Conductivity, W/m-K | Temp. Range, °F | Specifications Met | For Use On | Color | Autoclavable | Each | |
PVDF Plastic Coatings—Hard | |||||||||||||||
Bottle | |||||||||||||||
1 | Thick Liquid | 5 min. | 30 min. | No | __ | __ | 750 | 0.2 | -65° to 255° | IPC-CC-830 | Aluminum, Brass, Bronze, Steel, Stainless Steel, Titanium, Cast Iron, Iron, Silver, Plastic, Rubber, Composites, Fiberglass | Clear | Yes | 0000000 | 000000 |
Epoxy Coatings—Extra Hard | |||||||||||||||
Cartridge | |||||||||||||||
1.69 | Thick Liquid | 12 hrs. | 24 hrs. | Yes | 2:1 | No | 500 | Not Rated | -50° to 350° | __ | Aluminum, Brass, Bronze, Steel, Stainless Steel, Titanium, Cast Iron, Iron, Silver, Plastic, Rubber, Composites, Fiberglass | Clear | Yes | 0000000 | 00000 |
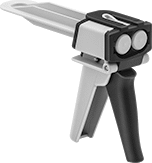
For Cartridge Size | Each | |
1.69 oz. | 00000000 | 000000 |
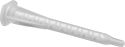
For Cartridge Size | Each | |
1.69 oz. | 00000000 | 00000 |
Heavy Duty High-Purity Coatings for Electronics
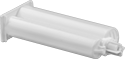
This coating is formulated for use in sensitive applications such as manufacturing semiconductors. Thinner than potting compounds, the coating flows easily into small spaces between electrical components. Use it to secure and insulate hardware on printed circuit boards. Rigid and wear resistant, has excellent chemical and moisture resistance, withstands a wide range of temperatures, and provides excellent electrical insulation. It requires a gun and a mixer nozzle (each sold separately) to dispense.
Certificates with a traceable lot number and product shelf life are available for these products. Download certificates from ORDER HISTORY after your order ships.
Dry Time | ||||||||||
---|---|---|---|---|---|---|---|---|---|---|
Mfr. Model No. | Container Size | Consistency | Touch, min. | Overall, hrs. | Dielectric Strength, V/mil | Temp. Range, °F | For Use On | Color | Each | |
Loctite® Coatings—Extra Hard | ||||||||||
M-21HP | 1.7 fl. oz. | Paste | 20 | 24 | 500 | -65° to 300° | Aluminum, Brass, Bronze, Copper, Steel, Stainless Steel, Titanium, Silver, Plastic, Composites, Fiberglass | Off-White | 0000000 | 000000 |
Heavy Duty Coatings for Electronics
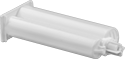
Thinner than potting compounds, these coatings flow easily into small spaces between electrical components. Use them to secure and insulate hardware on printed circuit boards. Rigid and wear resistant, epoxies have excellent chemical and moisture resistance, withstand a wide range of temperatures, and provide excellent electrical insulation. Dispense with a mixer nozzle and a gun (each sold separately).
Certificates with a traceable lot number and product shelf life are available for these products. Download certificates from ORDER HISTORY after your order ships.
Dry Time | ||||||||||
---|---|---|---|---|---|---|---|---|---|---|
Mfr. Model No. | Container Size, fl. oz. | Consistency | Touch, min. | Overall, hrs. | Dielectric Strength, V/mil | Temp. Range, °F | For Use On | Color | Each | |
Loctite® Coatings—Extra Hard | ||||||||||
E-00CL | 1.7 | Thick Liquid | 5 | 24 | 400 | -65° to 180° | Aluminum, Brass, Bronze, Copper, Steel, Stainless Steel, Titanium, Silver, Plastic, Composites, Fiberglass | Clear | 0000000 | 000000 |
E-00CL | 6.8 | Thick Liquid | 5 | 24 | 400 | -65° to 180° | Aluminum, Brass, Bronze, Copper, Steel, Stainless Steel, Titanium, Silver, Plastic, Composites, Fiberglass | Clear | 0000000 | 00000 |
Heavy Duty Light-Activated Coatings for Electronics
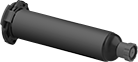
Thinner than potting compounds, these coatings flow easily into small spaces between electrical components. They require an ultraviolet curing lamp to reach full strength. Use them to secure and insulate hardware on printed circuit boards.
Syringe coatings require a gun (sold separately) to dispense.
Dry Time | |||||||||||||
---|---|---|---|---|---|---|---|---|---|---|---|---|---|
Mfr. | Mfr. Model No. | Container Size, fl. oz. | Consistency | Touch, sec. | Overall | Hardness Rating | Dielectric Strength, V/mil | Temp. Range, °F | Light Intensity Requirements to Reach Full Strength | For Use On | Color | Each | |
Syringe Coatings | |||||||||||||
Loctite® | 3751 | 4/5 | Thin Liquid | 10 | 2 min. | Extra Hard | 730 | -65° to 270° | 10 seconds @ 100 mW/cm 2 | Aluminum, Brass, Bronze, Copper, Steel, Stainless Steel, Silver, Titanium, Plastic, Composites, Fiberglass | Yellow | 00000000 | 000000 |
Dispensing Guns for Syringes | 0000000 | Each | 000000 |
Heavy Duty High-Purity Light-Activated Coatings for Electronics
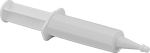
This coating is formulated for use in sensitive applications such as manufacturing semiconductors. Thinner than potting compounds, it flows easily into small spaces between electrical components. The coating begins to harden when exposed to UV light. Use it to secure and insulate hardware on printed circuit boards. It requires a gun (sold separately) to dispense.
Dry Time | |||||||||||
---|---|---|---|---|---|---|---|---|---|---|---|
Mfr. Model No. | Container Size, fl. oz. | Consistency | Touch, sec. | Overall, hrs. | Dielectric Strength, V/mil | Temp. Range, °F | Light Intensity Requirements to Reach Full Strength | For Use On | Color | Each | |
Loctite® Coatings—Medium Soft | |||||||||||
5240 | 0.85 | Thick Liquid | 10 | 72 | 533.4 | -65° to 195° | 60 seconds per side @ 70 mW/cm2 | Aluminum, Brass, Bronze, Copper, Steel, Stainless Steel, Silver, Titanium, Fiberglass, Composites | Green | 0000000 | 000000 |
Dispensing Guns for Syringes | 0000000 | Each | 000000 |
Heavy Duty Heat-Transfer Coatings for Electronics
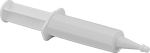
This thermally conductive coating keeps electrical components cool by dissipating heat. Use it to bond transformers, transistors, and other heat-generating components to printed circuit boards and heat sinks. It requires a gun (sold separately) to dispense.
Dry Time | ||||||||||
---|---|---|---|---|---|---|---|---|---|---|
Container Size, fl. oz. | Consistency | Touch, min. | Overall, hrs. | Dielectric Strength, V/mil | Thermal Conductivity, W/m-K | Temp. Range, °F | For Use On | Color | Each | |
1 | Paste | 5 | 2 | 750 | 0.864 | -85° to 347° | Aluminum, Brass, Bronze, Copper, Steel, Stainless Steel, Cast Iron, Iron, Silver, Plastic, Rubber, Composites, Fiberglass | White | 0000000 | 000000 |
Dispensing Guns for Syringes | 0000000 | Each | 000000 |
Optically Clear Coatings for Electronics
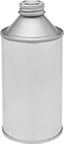
Protect LEDs, solar cells, and fiber optics with a coating that’s clear enough to see through. These coatings let optimal light pass through and repel dust and moisture, so they won’t distort your view of what’s underneath. Made of silicone, they won’t cloud in hot, humid environments. That means they’re great for use outdoors, such as on signs and instrumentation panels. Also known as conformal coatings, these coatings are thinner than potting compounds, flowing into the smallest contours on your device to cover it completely. Silicone conformal coatings are the most flexible kind of conformal coating, so they won’t crack or peel from vibration. To protect sensitive equipment, these coatings also prevent static discharge.
Simply spray these coatings on your device without needing a potting box or other container. Since they cure at room temperature, you won’t need UV lights or cure ovens either. You can remove them if necessary.
These coatings are IPC certified for use with circuit boards. They also meet UL 94 V-0 for flame retardance.
These coatings cannot be sold outside of North America due to regulatory limits on VOCs (volatile organic compounds).
Dry Time | |||||||||||
---|---|---|---|---|---|---|---|---|---|---|---|
Container Size, fl. oz. | Consistency | Touch, min. | Overall, hrs. | Dielectric Strength, V/mil | Temp. Range, °F | Specifications Met | For Use On | Color | Cannot Be Sold To | Each | |
19 | Thin Liquid | 30 | 72 | 720 | -75° to 390° | UL 94 V-0, IPC-CC-830 | Aluminum, Brass, Bronze, Copper, Steel, Stainless Steel, Titanium, Fiberglass, Ceramic, Glass, Composites, Plastic, Rubber, Silver | Clear | Outside North America | 0000000 | 000000 |
Moisture-Resistant Reflective Silicone Coatings for Roofs
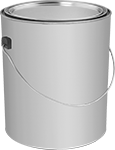
Made from silicone, these coatings are more durable than acrylic coatings for roofs and have better resistance to pooling water. They reflect up to 90% of the sun's rays to reduce cooling costs. Coatings are self-leveling and have excellent adhesion to most roof surfaces. They begin to protect against rain in as few as 60 minutes after application. Apply to a dry surface with a squeegee or brush.
Dry Time | ||||||||||
---|---|---|---|---|---|---|---|---|---|---|
Container Size, gal. | Composition | Surface Reflectivity | Touch, min. | Overall, hrs. | Approx. Coverage, sq. ft. | Application Temp. Range, °F | For Use On | Color | Each | |
1 | Solvent Based | 90% | 60 | 72 | 50 | 45° to 95° | Aluminum, Steel, Iron, Masonry, Concrete, Asphalt, Composites, Foam | White | 0000000 | 0000000 |
5 | Solvent Based | 90% | 60 | 72 | 250 | 45° to 95° | Aluminum, Steel, Iron, Masonry, Concrete, Asphalt, Composites, Foam | White | 0000000 | 000000 |
Reflective Asphalt Coatings for Roofs
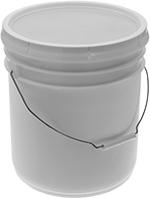
These coatings reflect up to 60% of the sun's rays. They also restore and reinforce your roof by forming a water-resistant seal. Apply to a dry surface with a sprayer or brush. They cannot be sold to the listed areas due to VOC regulations.
Dry Time | |||||||||||||
---|---|---|---|---|---|---|---|---|---|---|---|---|---|
Container Size, gal. | Composition | Surface Reflectivity | Touch, hrs. | Overall, hrs. | Approx. Coverage @ Thick. | Max. Temp., °F | Application Temp. Range, °F | Specifications Met | For Use On | Color | Cannot Be Sold To | Each | |
4 3/4 | Solvent Based | 60% | 4 | 24 | 235 sq. ft. @ 24 mil | 100° | 50° to 100° | ASTM D2824 Type 3 | Steel, Iron, Asphalt, Composites | Aluminum | CA, CO, CT, DE, MD, MI, NY, OH, RI, UT, Canada | 0000000 | 0000000 |
Reflective Acrylic Coatings for Roofs
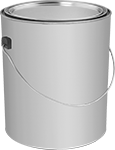
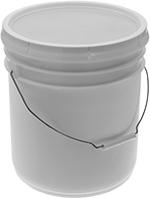
Reflect at least 85% of the sun's rays to reduce cooling costs. These coatings also restore and reinforce your roof by filling cracks and forming a water-resistant seal. Apply to a dry surface with a brush, roller, or sprayer.
Primer (sold separately) extends the life of the coating. It’s required for use on bare rubberized and aged asphalt roofs.
Dry Time | ||||||||||||
---|---|---|---|---|---|---|---|---|---|---|---|---|
Container Size, gal. | Composition | Surface Reflectivity | Touch, hrs. | Overall | Approx. Coverage, sq. ft. | Max. Temp., °F | Application Temp. Range, °F | For Use On | Primer Required For Use On | Color | Each | |
0.9 | Water Based | 85% | 6 | 30 days | 70 | __ | 50° to 70° | Steel, Iron, Rubber, Masonry, Concrete, Asphalt, Composites, Foam | Asphalt, Rubber | White | 0000000 | 000000 |
1 | Water Based | 85% | 2 | 24 hrs. | 100 | 375° | 60° to 200° | Aluminum, Galvanized Steel, Galvanized Iron, Masonry, Concrete, Wood, Composites | __ | White | 000000 | 00000 |
4.7 | Water Based | 85% | 6 | 30 days | 330 | __ | 50° to 70° | Steel, Iron, Rubber, Masonry, Concrete, Asphalt, Composites, Foam | Asphalt, Rubber | White | 0000000 | 000000 |
Primer for Ultra-Reflective Coatings for Roofs—0.9 Gal. Can | 000000 | Each | 000000 |
Stain-Resistant Primers
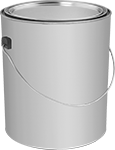
Cover stains from smoke, water, and ink to prevent them from bleeding through your topcoat, extending the life of paint and coatings.
Acrylic primer can be applied directly to metal. It resists corrosion, mold, and mildew. Apply with a brush, pad, roller, or sprayer.
Dry Time | ||||||||||
---|---|---|---|---|---|---|---|---|---|---|
Container Size, gal. | Composition | Touch, min. | Overall | Approx. Coverage @ Thick. | Max. Temp., °F | For Topcoat Composition | For Use On | Color | Each | |
Acrylic Primers | ||||||||||
1 | Water Based | 30 | 7 days | 300 sq. ft. @ 2 mil | 90° | Solvent Based, Water Based | Aluminum, Brass, Bronze, Copper, Steel, Plastic, Composites, Fiberglass, Concrete, Drywall | Gray | 000000 | 000000 |
Filling Primers
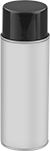
These primers fill surface cracks and are sandable for a smooth basecoat. Use them to prepare your surface to extend the life of paint and coatings. Choose gray for light-color topcoats; red for medium-color topcoats; and black for dark topcoats.
Dry Time | |||||||||||
---|---|---|---|---|---|---|---|---|---|---|---|
Container Net Weight, oz. | Composition | Touch, min. | Overall, min. | Approx. Coverage @ Thick. | Max. Temp., °F | For Topcoat Composition | For Use On | Color | Pkg. Qty. | Each | |
Each | |||||||||||
11 | Solvent Based | 30 | 60 | 14 sq. ft. @ 1 mil | 250° | Solvent Based | Steel, Iron, Composites, Fiberglass, Wood | Black | 6 | 0000000 | 000000 |
11 | Solvent Based | 30 | 60 | 12 sq. ft. @ 1 mil | 200° | Solvent Based | Steel, Iron, Composites, Fiberglass, Wood | Gray | 6 | 0000000 | 00000 |
11 | Solvent Based | 30 | 60 | 14 sq. ft. @ 1 mil | 200° | Solvent Based | Steel, Iron, Composites, Fiberglass, Wood | Red | 6 | 0000000 | 00000 |
Pkg. | |||||||||||
Pkg. | |||||||||||
11 | Solvent Based | 30 | 60 | 14 sq. ft. @ 1 mil | 250° | Solvent Based | Steel, Iron, Composites, Fiberglass, Wood | Black | 6 | 00000000 | 00000 |
11 | Solvent Based | 30 | 60 | 12 sq. ft. @ 1 mil | 200° | Solvent Based | Steel, Iron, Composites, Fiberglass, Wood | Gray | 6 | 00000000 | 00000 |
11 | Solvent Based | 30 | 60 | 14 sq. ft. @ 1 mil | 200° | Solvent Based | Steel, Iron, Composites, Fiberglass, Wood | Red | 6 | 00000000 | 00000 |