High-Strength Impact-Resistant Polycarbonate 3D Printer Filaments
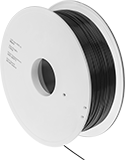
Create strong, durable parts that carry heavy loads and absorb blows and other impact without cracking or breaking. Made of polycarbonate, these filaments are stronger and resist heat better than other impact-resistant filaments, such as those made from ABS or ASA.
Use with a fused filament fabrication (FFF) 3D printer. These filaments have a high melting point and must be printed onto a heated bed. Without it, parts will cool too quickly and warp. These filaments also release fumes as they are printed, so use an enclosed printer or a fume exhauster to ventilate them.
Carbon-fiber-filled polycarbonate filaments make rigid parts that are difficult to bend and break. Parts made from these filaments can also be threaded and machined more easily than parts made from polycarbonate filaments without a filler. Fiberglass-filled polycarbonate filaments make parts that are less likely to warp or shrink than parts made from polycarbonate filaments without a filler. Both carbon-fiber- and fiberglass-filled filaments are abrasive, so you should use them with an abrasion-resistant nozzle.
Static-dissipative filaments make parts that protect equipment from electrostatic shocks by diverting electrostatic discharges in a controlled way. Use them to create tool handles, tote trays, enclosures, and other parts that are used near sensitive electronics. To adjust the surface resistivity of your printed part, change the temperature of your printer’s extruder. As the extruder’s temperature increases, the printed part’s resistivity will decrease.
UL 94 V-0 rated filaments meet strict flammability standards. Use them to create holders, guards, housings, and other parts that protect sensitive, flammable equipment and machinery.
Tensile strength is the best measure of a filament's overall strength. Similar to the stress applied on a rope during a game of tug-of-war, it's the amount of pulling force a material can handle before breaking. A higher rating means a stronger filament. A tensile strength of 5,000 psi and above is considered good; 12,000 psi and above is excellent.
Maximum exposure temperature is the point at which a printed part will begin to deform. Above this temperature, your printed parts will start to lose structural integrity.
Spool | |||||||||||||
---|---|---|---|---|---|---|---|---|---|---|---|---|---|
Dia., mm | Printing Temp. | For Printer Bed Temp. | Tensile Strength | Surface Resistivity, ohms/sq. | Hardness | Max. Exposure Temp. | For Min. Nozzle Opening Dia., mm | Dia., mm | Dp., mm | Wt., g | Color | Each | |
Polycarbonate Plastic | |||||||||||||
1.75 | 280° to 310° C 536° to 590° F | 110° to 120° C 230° to 248° F | 8,990 psi (Good) | __ | Durometer 84D (Hard) | 135° C 275° F | 0.4 | 195 | 40 | 500 | Black | 00000000 | 000000 |
Carbon-Fiber-Filled Polycarbonate Plastic | |||||||||||||
1.75 | 260° to 280° C 500° to 535° F | 80° to 100° C 175° to 210° F | 10,580 psi (Good) | __ | Not Rated | 115° C 245° F | 0.4 | 195 | 55 | 750 | Black | 00000000 | 00000 |
2.85 | 260° to 280° C 500° to 535° F | 80° to 100° C 175° to 210° F | 10,580 psi (Good) | __ | Not Rated | 115° C 245° F | 0.4 | 195 | 55 | 750 | Black | 00000000 | 00000 |
Polycarbonate Plastic—Static-Dissipative | |||||||||||||
1.75 | 260° to 300° C 500° to 572° F | 110° to 120° C 230° to 248° F | 9,860 psi (Good) | 107-109 | Rockwell R125 (Hard) | 135° C 275° F | 0.4 | 200 | 75 | 750 | Black | 0000000 | 000000 |
Fiberglass-Filled Polycarbonate Plastic—UL 94 V-0 | |||||||||||||
1.75 | 280° to 330° C 536° to 626° F | 80° to 100° C 176° to 212° F | 5,300 psi (Good) | __ | Not Rated | 124° C 255° F | 0.6 | 200 | 55 | 700 | Black | 0000000 | 000000 |
2.85 | 280° to 330° C 536° to 626° F | 80° to 100° C 176° to 212° F | 5,300 psi (Good) | __ | Not Rated | 124° C 255° F | 0.6 | 200 | 55 | 700 | Black | 0000000 | 000000 |