Compare over 20 aluminum alloys to find the right material for you—all with material certificates for traceability.
Multipurpose 6061 Aluminum Sheets and Bars
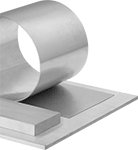
The most widely used aluminum, 6061 is fabricated into everything from pipe fittings and containers to automotive and aerospace parts. It is strong and corrosion resistant, plus it's easy to machine and weld.
Cold-rolled foil, sheets, and bars are cut from large pieces to the widths and lengths listed, so the edges may not be parallel.
Aluminum that meets ASTM B209 or ASTM B221 complies with standards for materials.
Aluminum that meets an SAE AMS standard conforms to the material and process needs of the aerospace industry.
If you don’t see the sheet or bar size you need, please specify dimensions under additional sheet sizes or additional bar lengths.
Certificates with a traceable lot number are available for these products. Download certificates from ORDER HISTORY after your order ships.
- Yield Strength: 35,000 psi
- Hardness: Brinell 95 (Soft)
- Temper: See table
- Fabrication: See table
- Specifications Met: See table
Thick. | Thick. Tolerance | Fabrication | Temper | Heat Treatment | Temp. Range, °F | Specifications Met | Each | |
2" × 12" | ||||||||
---|---|---|---|---|---|---|---|---|
0.063" | -0.004" to 0.004" | Cold Rolled | T6 | Hardened | -320° to 210° | ASTM B209, SAE AMS4027 | 000000000 | 00000 |
2" × 24" | ||||||||
0.063" | -0.004" to 0.004" | Cold Rolled | T6 | Hardened | -320° to 210° | ASTM B209, SAE AMS4027 | 000000000 | 0000 |
2" × 48" | ||||||||
0.063" | -0.004" to 0.004" | Cold Rolled | T6 | Hardened | -320° to 210° | ASTM B209, SAE AMS4027 | 00000000 | 00000 |
2" × 72" | ||||||||
0.063" | -0.004" to 0.004" | Cold Rolled | T6 | Hardened | -320° to 210° | ASTM B209, SAE AMS4027 | 000000000 | 00000 |
4" × 12" | ||||||||
0.063" | -0.004" to 0.004" | Cold Rolled | T6 | Hardened | -320° to 210° | ASTM B209, SAE AMS4027 | 000000000 | 0000 |
4" × 24" | ||||||||
0.063" | -0.004" to 0.004" | Cold Rolled | T6 | Hardened | -320° to 210° | ASTM B209, SAE AMS4027 | 000000000 | 00000 |
4" × 48" | ||||||||
0.063" | -0.004" to 0.004" | Cold Rolled | T6 | Hardened | -320° to 210° | ASTM B209, SAE AMS4027 | 00000000 | 00000 |
4" × 72" | ||||||||
0.063" | -0.004" to 0.004" | Cold Rolled | T6 | Hardened | -320° to 210° | ASTM B209, SAE AMS4027 | 000000000 | 00000 |
6" × 6" | ||||||||
0.063" | -0.004" to 0.004" | Cold Rolled | T6 | Hardened | -320° to 210° | ASTM B209, SAE AMS4027 | 000000000 | 0000 |
6" × 12" | ||||||||
0.063" | -0.004" to 0.004" | Cold Rolled | T6 | Hardened | -320° to 210° | ASTM B209, SAE AMS4027 | 000000000 | 0000 |
6" × 24" | ||||||||
0.063" | -0.004" to 0.004" | Cold Rolled | T6 | Hardened | -320° to 210° | ASTM B209, SAE AMS4027 | 000000000 | 00000 |
6" × 48" | ||||||||
0.063" | -0.004" to 0.004" | Cold Rolled | T6 | Hardened | -320° to 210° | ASTM B209, SAE AMS4027 | 00000000 | 00000 |
6" × 72" | ||||||||
0.063" | -0.004" to 0.004" | Cold Rolled | T6 | Hardened | -320° to 210° | ASTM B209, SAE AMS4027 | 000000000 | 00000 |
8" × 8" | ||||||||
0.063" | -0.004" to 0.004" | Cold Rolled | T6 | Hardened | -320° to 210° | ASTM B209, SAE AMS4027 | 000000000 | 0000 |
12" × 12" | ||||||||
0.063" | -0.004" to 0.004" | Cold Rolled | T6 | Hardened | -320° to 210° | ASTM B209, SAE AMS4027 | 00000000 | 00000 |
12" × 24" | ||||||||
0.063" | -0.004" to 0.004" | Cold Rolled | T6 | Hardened | -320° to 210° | ASTM B209, SAE AMS4027 | 00000000 | 00000 |
12" × 36" | ||||||||
0.063" | -0.004" to 0.004" | Cold Rolled | T6 | Hardened | -320° to 210° | ASTM B209, SAE AMS4027 | 000000000 | 00000 |
12" × 48" | ||||||||
0.063" | -0.004" to 0.004" | Cold Rolled | T6 | Hardened | -320° to 210° | ASTM B209, SAE AMS4027 | 000000000 | 00000 |
12" × 72" | ||||||||
0.063" | -0.004" to 0.004" | Cold Rolled | T6 | Hardened | -320° to 210° | ASTM B209, SAE AMS4027 | 000000000 | 00000 |
18" × 18" | ||||||||
0.063" | -0.004" to 0.004" | Cold Rolled | T6 | Hardened | -320° to 210° | ASTM B209, SAE AMS4027 | 000000000 | 00000 |
24" × 24" | ||||||||
0.063" | -0.004" to 0.004" | Cold Rolled | T6 | Hardened | -320° to 210° | ASTM B209, SAE AMS4027 | 00000000 | 00000 |
24" × 48" | ||||||||
0.063" | -0.004" to 0.004" | Cold Rolled | T6 | Hardened | -320° to 210° | ASTM B209, SAE AMS4027 | 00000000 | 00000 |
24" × 72" | ||||||||
0.063" | -0.004" to 0.004" | Cold Rolled | T6 | Hardened | -320° to 210° | ASTM B209, SAE AMS4027 | 000000000 | 000000 |
36" × 36" | ||||||||
0.063" | -0.004" to 0.004" | Cold Rolled | T6 | Hardened | -320° to 210° | ASTM B209, SAE AMS4027 | 00000000 | 00000 |
48" × 48" | ||||||||
0.063" | -0.004" to 0.004" | Cold Rolled | T6 | Hardened | -320° to 210° | ASTM B209, SAE AMS4027 | 00000000 | 000000 |
48" × 72" | ||||||||
0.063" | -0.004" to 0.004" | Cold Rolled | T6 | Hardened | -320° to 210° | ASTM B209, SAE AMS4027 | 000000000 | 000000 |
- Yield Strength: 35,000 psi
- Hardness: Brinell 95 (Soft)
- Temper:
Cold Rolled sheets: T6
Extruded sheets: T6511 - Fabrication: See table
- Specifications Met:
Cold Rolled sheets: ASTM B209, SAE AMS4027
Extruded sheets: ASTM B221, SAE AMS QQ-A-200/8
To Order: Please specify length and width in increments of 0.25" within the range listed.
Anodized Multipurpose 6061 Aluminum Sheets and Bars

- Yield Strength: 35,000 psi
- Hardness: Not Rated
- Temper: See table
- Fabrication: Extruded
- Specifications Met: See table
An anodized coating bonds to the aluminum surface to improve wear and corrosion resistance. The most widely used aluminum, 6061 is fabricated into everything from pipe fittings and containers to automotive and aerospace parts. It is strong and corrosion resistant, plus it's easy to machine and weld.
Gray finish is also known as hard anodized. The surface is so hard, it’s comparable to case-hardened steel, which makes these sheets and bars more difficult to machine than uncoated 6061 aluminum.
Corrosion-Resistant 3000 Series Aluminum Sheets and Bars
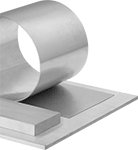
3000 series aluminum stands up to outdoor use, as well as exposure to chemicals. It offers a good combination of strength, formability, and weldability. It's often used for storage tanks, heat exchangers, garage doors, and general sheet metal work.
Certificates with a traceable lot number are available for these products. Download certificates from ORDER HISTORY after your order ships.
- Yield Strength: 16,500 psi
- Hardness: Brinell 40 (Soft)
- Temper: H14 (1/2 Hard)
- Fabrication: Cold Worked
- Specifications Met: ASTM B209
Thick. | Thick. Tolerance | Temperature Range, °F | Each | |
6" × 24" | ||||
---|---|---|---|---|
0.063" | -0.006" to 0.006" | -300° to 300° | 00000000 | 00000 |
6" × 48" | ||||
0.063" | -0.006" to 0.006" | -300° to 300° | 00000000 | 00000 |
12" × 12" | ||||
0.063" | -0.006" to 0.006" | -300° to 300° | 00000000 | 0000 |
12" × 24" | ||||
0.063" | -0.006" to 0.006" | -300° to 300° | 00000000 | 00000 |
12" × 36" | ||||
0.063" | -0.006" to 0.006" | -300° to 300° | 00000000 | 00000 |
12" × 48" | ||||
0.063" | -0.006" to 0.006" | -300° to 300° | 00000000 | 00000 |
24" × 24" | ||||
0.063" | -0.006" to 0.006" | -300° to 300° | 00000000 | 00000 |
24" × 36" | ||||
0.063" | -0.006" to 0.006" | -300° to 300° | 00000000 | 00000 |
36" × 48" | ||||
0.063" | -0.006" to 0.006" | -300° to 300° | 00000000 | 000000 |
36" × 96" | ||||
0.063" | -0.006" to 0.006" | -300° to 300° | 00000000 | 000000 |
Textured Corrosion-Resistant 3003 Aluminum Sheets
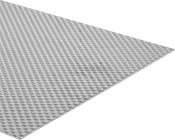
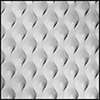
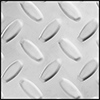
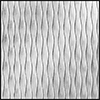
- Yield Strength: 17,000 psi
- Hardness: Brinell 40 (Soft)
- Temper: H14 (1/2 Hard)
- Fabrication: Cold Rolled
- Specifications Met: ASTM B209
The textured surface on these sheets increases rigidity and hides fingerprints and dents. They are intended for use in decorative applications, such as partitions and surface protectors, and should not be confused with traction floor plates. 3003 aluminum stands up to outdoor use, as well as exposure to chemicals. It offers a good combination of strength, formability, and weldability.
Certificates with a traceable lot number are available for these products. Download certificates from ORDER HISTORY after your order ships.
Diamond | Tread | Weave | |||||
---|---|---|---|---|---|---|---|
Thick. | Thick. Tolerance | Each | Each | Each | |||
12" × 12" | |||||||
0.063" | -0.004" to 0.004" | 00000000 | 000000 | 00000000 | 000000 | 00000000 | 000000 |
12" × 24" | |||||||
0.063" | -0.004" to 0.004" | 00000000 | 00000 | 00000000 | 00000 | 00000000 | 00000 |
24" × 24" | |||||||
0.063" | -0.004" to 0.004" | 00000000 | 00000 | 00000000 | 00000 | 00000000 | 00000 |
24" × 36" | |||||||
0.063" | -0.004" to 0.004" | 00000000 | 00000 | 00000000 | 00000 | 00000000 | 00000 |
24" × 48" | |||||||
0.063" | -0.004" to 0.004" | 00000000 | 000000 | 00000000 | 000000 | 00000000 | 000000 |
48" × 48" | |||||||
0.063" | -0.004" to 0.004" | 00000000 | 000000 | 00000000 | 000000 | 00000000 | 000000 |
Easy-to-Weld 5052 Aluminum Sheets and Bars
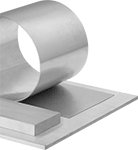
Known for being one of the easiest types of aluminum to weld, 5052 is also recognized for its ability to resist salt water. It's widely used for the bodies of boats, buses, trucks, and trailers, as well as for chemical drums.
Certificates with a traceable lot number are available for these products. Download certificates from ORDER HISTORY after your order ships.
- Yield Strength: 23,000 psi
- Hardness: Brinell 60 (Soft)
- Temper: H32 (1/4 Hard)
- Fabrication: Cold Rolled
- Specifications Met: ASTM B209
Thick. | Thick. Tolerance | Temperature Range, °F | Each | |
2" × 24" | ||||
---|---|---|---|---|
0.063" | -0.004" to 0.004" | -300° to 300° | 00000000 | 00000 |
2" × 48" | ||||
0.063" | -0.004" to 0.004" | -300° to 300° | 000000000 | 00000 |
4" × 24" | ||||
0.063" | -0.004" to 0.004" | -300° to 300° | 00000000 | 00000 |
4" × 48" | ||||
0.063" | -0.004" to 0.004" | -300° to 300° | 000000000 | 00000 |
6" × 6" | ||||
0.063" | -0.004" to 0.004" | -300° to 300° | 000000000 | 0000 |
6" × 12" | ||||
0.063" | -0.004" to 0.004" | -300° to 300° | 00000000 | 00000 |
6" × 24" | ||||
0.063" | -0.004" to 0.004" | -300° to 300° | 00000000 | 00000 |
6" × 48" | ||||
0.063" | -0.004" to 0.004" | -300° to 300° | 000000000 | 00000 |
12" × 12" | ||||
0.063" | -0.004" to 0.004" | -300° to 300° | 00000000 | 00000 |
12" × 24" | ||||
0.063" | -0.004" to 0.004" | -300° to 300° | 00000000 | 00000 |
12" × 48" | ||||
0.063" | -0.004" to 0.004" | -300° to 300° | 000000000 | 00000 |
24" × 24" | ||||
0.063" | -0.004" to 0.004" | -300° to 300° | 00000000 | 00000 |
24" × 48" | ||||
0.063" | -0.004" to 0.004" | -300° to 300° | 00000000 | 00000 |
24" × 72" | ||||
0.063" | -0.004" to 0.004" | -300° to 300° | 000000000 | 000000 |
48" × 48" | ||||
0.063" | -0.004" to 0.004" | -300° to 300° | 00000000 | 000000 |
48" × 72" | ||||
0.063" | -0.004" to 0.004" | -300° to 300° | 000000000 | 000000 |
Polished Easy-to-Weld 5052 Aluminum Sheets and Bars
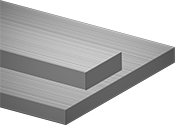
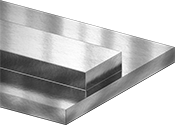
- Yield Strength: 20,000 psi
- Temper: H32 (1/4 Hard)
- Fabrication: Cold Rolled
- Specifications Met: ASTM B209
One side of these sheets and bars is polished to either a brushed finish or a mirror-like finish. The polished side is covered with a protective, peel-off film. Known for being one of the easiest types of aluminum to weld, 5052 is also recognized for its ability to resist salt water. It's widely used for the bodies of boats, buses, trucks, and trailers, as well as for chemical drums.
Brushed sheets and bars are polished to a #4 satin finish with grain lines running in one direction to mask fingerprints.
Mirror-like sheets and bars are polished to a #8 reflective finish and are free of grain lines.
Certificates with a traceable lot number are available for these products. Download certificates from ORDER HISTORY after your order ships.
Hardened Easy-to-Form Pure 1100 Aluminum Sheets
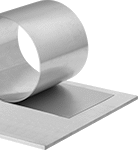
These sheets are tempered to a 1/2-hard or full-hard state to make them over twice as strong as standard 1100 aluminum. Because 1100 aluminum is 99% pure, it offers superior corrosion resistance and electrical conductivity.
Temper H14 sheets are used for heat exchangers, chemical equipment, and decorative trim.
Certificates with a traceable lot number are available for these products. Download certificates from ORDER HISTORY after your order ships.
- Yield Strength: 15,000 psi
- Hardness: Brinell 30 (Soft)
- Temper: H14 (1/2 Hard)
- Fabrication: Cold Worked
- Specifications Met: ASTM B209
Easy-to-Form Pure 1000 Series Aluminum Sheets and Bars
Made of 1000 series aluminum which is 99% pure, this aluminum offers superior formability, corrosion resistance, and electrical conductivity. It's frequently fabricated into raceways, decorative trim, and other parts where strength and hardness are not required. These temper O foil, sheets, and bars are annealed to the softest state possible, which is sometimes called “dead soft.”
Certificates with a traceable lot number are available for these products. Download certificates from ORDER HISTORY after your order ships.
- Yield Strength: 3,500 psi
- Hardness: Brinell 20 (Soft)
- Temper: O
- Fabrication: Cold Rolled
- Specifications Met: ASTM B209
Easy-to-Form Marine-Grade 5086 Aluminum Sheets and Bars
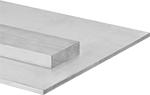
- Yield Strength: 28,000 psi
- Hardness: Not Rated
- Temper: H32 (1/4 Hard)
- Fabrication: Cold Worked
- Specifications Met: ASTM B209
5086 aluminum is used on ships, oil rigs, tanks, and pressure vessels because of its excellent saltwater resistance and formability.
Certificates with a traceable lot number are available for these products. Download certificates from ORDER HISTORY after your order ships.
Choose-a-Color 5005 Aluminum
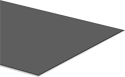

- Yield Strength: 15,000 psi
- Hardness: Not Rated
- Temper: H34 (1/2 Hard)
- Fabrication: Cold Rolled
A black, gold, or silver anodized finish protects this 5005 aluminum from wear and abrasion. These sheets are anodized on one side, then covered with a protective film. The black finish is matte, while the gold and silver finishes are brushed to mask fingerprints.
Certificates with a traceable lot number are available for these products. Download certificates from ORDER HISTORY after your order ships.
High-Strength 2024 Aluminum Sheets and Bars
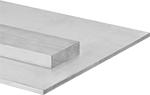
While 2024 aluminum was initially designed for structural components in aircraft, it's now widely used when a high strength-to-weight ratio is needed, such as for gears, shafts, and fasteners. It offers similar performance to 7075 aluminum, but it’s not as strong.
Cold-rolled sheets are cut from large pieces to the widths and lengths listed, so the edges may not be parallel.
Certificates with a traceable lot number are available for these products. Download certificates from ORDER HISTORY after your order ships.
- Yield Strength: 41,000 psi
- Hardness: Brinell 120 (Medium)
- Temper:
0.020" to 0.190" thick. sheets: T3
All other sizes: T351 - Fabrication: Cold Rolled
- Specifications Met: ASTM B209
Thick. | Thick. Tolerance | Heat Treatment | Temperature Range, °F | Each | |
6" × 6" | |||||
---|---|---|---|---|---|
0.063" | -0.002" to 0.002" | Hardened | -320° to 300° | 000000000 | 000000 |
8" × 8" | |||||
0.063" | -0.002" to 0.002" | Hardened | -320° to 300° | 000000000 | 00000 |
12" × 12" | |||||
0.063" | -0.002" to 0.002" | Hardened | -320° to 300° | 00000000 | 00000 |
12" × 24" | |||||
0.063" | -0.002" to 0.002" | Hardened | -320° to 300° | 00000000 | 00000 |
18" × 18" | |||||
0.063" | -0.002" to 0.002" | Hardened | -320° to 300° | 000000000 | 00000 |
24" × 24" | |||||
0.063" | -0.002" to 0.002" | Hardened | -320° to 300° | 00000000 | 000000 |
24" × 48" | |||||
0.063" | -0.002" to 0.002" | Hardened | -320° to 300° | 00000000 | 000000 |
48" × 48" | |||||
0.063" | -0.002" to 0.002" | Hardened | -320° to 300° | 00000000 | 000000 |
48" × 72" | |||||
0.063" | -0.002" to 0.002" | Hardened | -320° to 300° | 000000000 | 000000 |
Clad High-Strength 2024 Aluminum Sheets
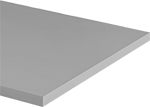
- Yield Strength:
6" × 6": 45,000 psi
All other sizes: 42,000 psi - Hardness: Not Rated
- Temper: T3
- Fabrication: Cold Rolled
- Specifications Met: ASTM B209, SAE AMS-QQ-A-250/5, SAE AMS4462
These sheets are clad in 1230 aluminum for an added layer of corrosion resistance. While 2024 aluminum was initially designed for structural components in aircraft, it's now widely used when a high strength-to-weight ratio is needed, such as for gears, shafts, and fasteners. It offers similar performance to 7075 aluminum, but it’s not as strong.
Certificates with a traceable lot number are available for these products. Download certificates from ORDER HISTORY after your order ships.
High-Strength 7075 Aluminum Sheets and Bars
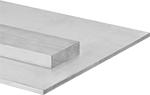
Originally developed for aircraft frames, uses for 7075 aluminum now include keys, gears, and other high-stress parts. It is often used as a replacement for 2024 aluminum because it’s stronger and provides similar performance in all other aspects.
Hot-rolled, cold-rolled, and cast sheets are cut from large pieces to the widths and lengths listed, so the edges may not be parallel.
Certificates with a traceable lot number are available for these products. Download certificates from ORDER HISTORY after your order ships.
- Yield Strength: 61,000 psi
- Hardness: Brinell 150 (Medium)
- Temper:
0.032" thick. to 0.190" thick.: T6
1/4" thick. and thicker.: T651 - Fabrication: See Table
- Specifications Met: ASTM B209, SAE AMS-QQ-A-250/12
Thick. | Thick. Tolerance | Fabrication | Heat Treatment | Temperature Range, °F | Each | |
6" × 6" | ||||||
---|---|---|---|---|---|---|
0.063" | -0.002" to 0.002" | Cast | Hardened | -320° to 210° | 00000000 | 00000 |
6" × 12" | ||||||
0.063" | -0.002" to 0.002" | Cast | Hardened | -320° to 210° | 00000000 | 00000 |
6" × 24" | ||||||
0.063" | -0.002" to 0.002" | Cast | Hardened | -320° to 210° | 00000000 | 00000 |
8" × 8" | ||||||
0.063" | -0.002" to 0.002" | Cast | Hardened | -320° to 210° | 00000000 | 00000 |
12" × 12" | ||||||
0.063" | -0.002" to 0.002" | Cast | Hardened | -320° to 210° | 0000000 | 00000 |
12" × 24" | ||||||
0.063" | -0.002" to 0.002" | Cast | Hardened | -320° to 210° | 0000000 | 00000 |
18" × 18" | ||||||
0.063" | -0.002" to 0.002" | Cast | Hardened | -320° to 210° | 00000000 | 00000 |
24" × 24" | ||||||
0.063" | -0.002" to 0.002" | Cast | Hardened | -320° to 210° | 0000000 | 00000 |
24" × 48" | ||||||
0.063" | -0.002" to 0.002" | Cast | Hardened | -320° to 210° | 0000000 | 000000 |
48" × 48" | ||||||
0.063" | -0.002" to 0.002" | Cast | Hardened | -320° to 210° | 0000000 | 000000 |