Additives and Reinforcements for Composites
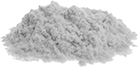
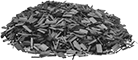
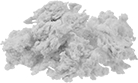
Mix these additives with melted plastic, epoxies, or adhesives to make parts stronger and more wear resistant without adding much weight. You can use them in batches to tackle repairs and small parts instead of machining your part from a sheet, bar, or other shape.
Fiberglass
These additives increase a part’s strength and ability to withstand frequent blows. But, they’re not as strong or as lightweight as carbon fiber additives. They also block electric currents from passing through. Their short fibers are best for castings and foams to prevent cracking as resin shrinks. The amount you use to start should equal about 10-35% of your composite’s weight.
Carbon Fiber and Recycled Carbon Fiber
Often used in vehicles to increase fuel efficiency, these additives can double your composite’s strength to make stiff pieces that are stronger and lighter in weight than aluminum. The more you add to your mixture, the stronger it becomes. These additives also carry electric currents, so they’re good for directing electromagnetic energy away from electrical devices. However, they don’t direct electricity as well as metal. They’re made of chopped fibers, which makes them ideal for repairs and intricate parts. But, they’re not as strong or as stiff as materials with continuous fibers, such as fabric and tow.
The size of carbon fiber’s particles affects its ease of use and strength. The smaller the particle size, the less effort it requires to mix. On the other hand, larger particles make parts stronger and stiffer. Choose carbon fiber with smaller particle sizes when making intricate parts and repairs.
Recycled carbon fiber additives have a low carbon footprint to help you meet environmental goals. But, they’re not as strong or as stiff as standard carbon fiber additives.
Carbon fiber additives for thermoplastics bond with most melted plastic pellets, except PVDF. Shape your mixture into parts with compression and injection molding or 3D printing. You can shape your finished product multiple times without losing its strength. Start by adding 10% by volume to your mixture. Carbon fiber additives for thermosets mix with epoxies, adhesives, vinyl compounds, and phenolic. Use compression molding to turn your mixture into parts, or fill in cavities after curing without adding weight. You can’t shape your product once it’s cured. Begin with 5% by volume in your mixture.
Kevlar
Choose these additives when your application is likely to wear down your finished part—they improve a part’s ability to stand up to corrosion, bangs, bumps, and scrapes. They’re also used to reinforce points where honeycomb cores connect to fabric. To start, mix in 1 part Kevlar to 15 parts composite.
Container | |||||||||
---|---|---|---|---|---|---|---|---|---|
Compatible With | Concentration | Net Weight | Type | Material | Form | Particle Size | CAS Number | Each | |
Fiberglass | |||||||||
Thermoplastics, Thermosets | 98% | 10 lbs. | Jug | Plastic | Loose Fiber | 840 microns | 65997-17-3 | 0000000 | 000000 |
Carbon Fiber | |||||||||
Thermoplastics | 91% | 1 lbs. | Box | Cardboard | Flake | 6350 microns | 7440-44-0 | 0000000 | 00000 |
Thermoplastics | 91% | 5 lbs. | Box | Cardboard | Flake | 6350 microns | 7440-44-0 | 0000000 | 000000 |
Thermosets | 91% | 1 lbs. | Box | Cardboard | Flake | 3175 microns | 7440-44-0 | 0000000 | 00000 |
Thermosets | 91% | 1 lbs. | Box | Cardboard | Flake | 6350 microns | 7440-44-0 | 0000000 | 00000 |
Thermosets | 91% | 5 lbs. | Box | Cardboard | Flake | 3175 microns | 7440-44-0 | 0000000 | 000000 |
Thermosets | 91% | 5 lbs. | Box | Cardboard | Flake | 6350 microns | 7440-44-0 | 0000000 | 000000 |
Recycled Carbon Fiber | |||||||||
Thermoplastics | 91% | 1 lbs. | Box | Cardboard | Flake | 6350 microns | 7440-44-0 | 0000000 | 00000 |
Thermoplastics | 91% | 5 lbs. | Box | Cardboard | Flake | 6350 microns | 7440-44-0 | 0000000 | 00000 |
Kevlar | |||||||||
Thermoplastics | 80% | 1 lbs. | Box | Cardboard | Loose Fiber | 1050 microns | 26125-61-1 | 0000000 | 000000 |
Thermoplastics | 80% | 2 oz. | Tube | Cardboard | Loose Fiber | 1050 microns | 26125-61-1 | 0000000 | 00000 |
Easy-to-Machine Aluminum-Nitride Ceramic Rods
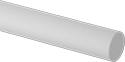
- Color: Beige
- Max. Temperature: 3,400° F
- Fabrication: Hot Rolled, Sintered
- Electrical Properties: Electrical Insulating
- Dielectric Strength: 1,650 V/mil
- Porosity: 0%
- Compressive Strength: 140,000 psi
Turn and drill intricate components such as heat sinks, fixture parts, and other electronics parts where thermal stability is important. Aluminum nitride both draws heat away from hot spots and block electrical currents. Also known as Shapal Hi-M, this blend includes boron nitride, so these rods are easier to machine than standard aluminum nitride. The addition of boron nitride slightly decreases heat transfer and electrical insulating properties; but this material still performs better than other ceramics.
Aluminum nitride won’t expand or contract as it heats up and cools down—its size and shape remains stable. Braze or solder this material to metal—it won't corrode from molten metal. You can use this material near lithium batteries and other chlorides without it corroding.