About Paint and Protective Coatings
More
Parylene Coatings for Electronics
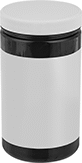
Protect sensitive electronics at the molecular level—these ultra-thin, ultra-conformal coatings cover every inch of your components for applications where failure isn’t an option. They’ve even been trusted on satellites and medical devices. Use them to insulate current, prevent arcs and short circuits, and shield against moisture, chemicals, and gases. They’re better insulators than epoxy, urethane, and silicone coatings. Deposited as vapor in a vacuum chamber, they’re 90% lighter than spray and dip coatings. That means they’ll keep your items lightweight and won’t damage complex geometries. These coatings meet ASTM E595, a standard used by NASA, so they produce almost no volatile emissions that could damage sensitive electronics, even in a vacuum.
Note: These coatings must be applied using special parylene deposition equipment.
Parylene C coatings are the most widely used. They contain chlorine, so they shield against moisture, chemicals, and corrosive gases better than Parylene N coatings. Plus, they’re stronger and quicker to apply.
Parylene N coatings are better electrical insulators than Parylene C coatings. They also penetrate deeper into crevices on your components for more complete coverage. However, they’re slower to apply.
Container Net Weight, lbs. | Consistency | Mixing Required | Dielectric Strength, V/mil | Thermal Conductivity, W/m-K | Max. Temp., °F | Melting Temp., °F | Cure Type | Specifications Met | For Use Outdoors | For Use On | Color | Each | |
Parylene C Coatings—Hard | |||||||||||||
---|---|---|---|---|---|---|---|---|---|---|---|---|---|
1 | Film | No | 5,600 | 0.084 | 175° | 550° | Non-Hardening | ASTM E595 | Yes | Aluminum, Brass, Bronze, Copper, Steel, Stainless Steel | White | 00000000 | 0000000 |
Parylene N Coatings—Hard | |||||||||||||
1 | Film | No | 7,000 | 0.126 | 140° | 785° | Non-Hardening | ASTM E595 | Yes | Aluminum, Brass, Bronze, Copper, Steel, Stainless Steel | White | 00000000 | 000000 |
Low-Outgassing Optically Clear Two-Part Silicone Potting Compounds
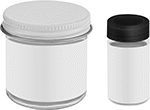
Tested to meet ASTM E595, a standard used by NASA, these compounds produce almost no volatile emissions that could damage sensitive electronics, even in a vacuum. Light passes through them easily, so they’re ideal for protecting solar cells and fiber optics. Made of silicone, these compounds are softer and more flexible than epoxy and urethane compounds. That means they’re better at protecting against shocks and vibration. They also withstand a wider range of temperatures, so you can use them with electronics that heat and cool rapidly. These compounds are excellent electrical insulators, and they’ll shield your components from moisture and dust. However, they don’t hold up well to chemicals or scrapes. They’re also known as RTV (room-temperature vulcanizing).
These compounds are easy to apply in high volumes. Just mix the two parts together and pour them over components inside a container, such as a potting box.
Dry Time | ||||||||||||
---|---|---|---|---|---|---|---|---|---|---|---|---|
Container Size, oz. | Consistency | Touch, hrs. | Overall, hrs. | Hardness Rating | Dielectric Strength, V/mil | Thermal Conductivity, W/m-K | Temp. Range, °F | Specifications Met | For Use On | Color | Each | |
4.1 | Thick Liquid | 3 | 24 | Medium Soft | 475 | 0.2 | -45° to 390° | ASTM E595 | Aluminum, Brass, Bronze, Copper, Steel, Iron, Silver, Fiberglass, Glass | Clear | 0000000 | 000000000 |
Low-Outgassing Heat-Transfer Epoxy Potting Compounds
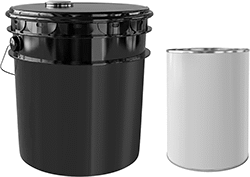
Tested to meet ASTM E595, a standard used by NASA, these potting compounds release almost no volatile emissions that could damage sensitive electronics, even in a vacuum. Use them to draw heat away from your components—they conduct heat better than standard potting compounds. Made of epoxy, they’re the strongest of the potting compounds, so they’re rigid and wear resistant. They’ll also resist breaking down from chemicals and moisture. These compounds are excellent at insulating current, and they’ll shield against dust, vibration, and shock.
To apply, mix the two parts together and pour them over components inside a container, such as a potting box.
Dry Time | ||||||||||||
---|---|---|---|---|---|---|---|---|---|---|---|---|
Container Size, fl. oz. | Consistency | Touch | Overall | Dielectric Strength, V/mil | Thermal Conductivity, W/m-K | Temp. Range, °F | Heating Requirements to Reach Full Strength | Specifications Met | For Use On | Color | Each | |
Pail and Can Compounds—Extra Hard | ||||||||||||
32 | Thick Liquid | 45 min. | 24 hrs. | 365 | 1.25 | -40° to 265° | __ | ASTM E595 | Aluminum, Brass, Bronze, Copper, Steel, Stainless Steel, Plastic | Black | 0000000 | 0000000 |
32 | Thick Liquid | 4 hrs. | 12 hrs. | 450 | 0.55 | -65° to 310° | 12 hrs. @ 175° F | ASTM E595 | Aluminum, Brass, Bronze, Copper, Steel, Stainless Steel, Plastic | Black | 0000000 | 000000 |