About Paint and Protective Coatings
More
Coatings for Electronics
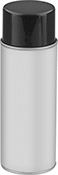
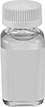
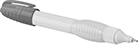
Also known as conformal coatings, these coatings protect circuit boards and other electronics from moisture, dust, and static. They’re thinner than potting compounds, so they flow into the smallest contours of your components to cover them completely. Apply these coatings without needing a potting box or other container. You can remove them if necessary.
Acrylic and acrylic lacquer coatings are our thinnest option, so they’re the easiest to apply. They’ll also come off the easiest when you have to rework or repair your component—just use a solvent. These coatings dry in a day or less. Acrylic lacquer coatings dry in just 30 minutes, the quickest of our conformal coatings. They resist grease, oil, and alkalies. Ideal for metal parts, they prevent rusting. Along with circuit boards, they’re often used on batteries.
Silicone coatings protect components over a wide range of temperatures. They’re also the most flexible of our conformal coatings, so they won’t crack from vibration. However, they’re thicker than acrylic coatings, so they’re more difficult to apply and remove.
Silicone/acrylic coatings combine the flexibility and temperature resistance of silicone with the thinness of acrylic for easy application. Use them in the environments you’d use silicone coatings, such as high-vibration and high-temperature areas.
Urethane coatings are the best choice for harsh environments. They have the best chemical resistance in our offering, and they’re extra hard for the best resistance to scrapes. Plus, they won’t crack in low temperatures. However, they aren’t as flexible as silicone coatings, so they’re worse at handling vibration. They’re also harder to apply than acrylic coatings because they’re thicker.
Coatings in a bottle come with a brush for touch-ups. Coatings in a pen are best for precise application. Use them to repair scratches and chips on components, or touch up areas you missed while coating. They’re also good for blocking off areas you don’t want solder to flow into.
Coatings with ultraviolet visibility show up under a black light, so you can easily check if you’ve applied them evenly.
Coatings that meet IPC-CC-830 are certified for use on circuit boards. Coatings that meet UL 94 V-0 have passed a test for flame retardance.
Coatings that cannot be sold to the listed areas are restricted due to VOCs (volatile organic compounds) regulations.
Dry Time | Temp. Range, °F | ||||||||||||
---|---|---|---|---|---|---|---|---|---|---|---|---|---|
Container Size, fl. oz. | Container Net Wt., oz. | Touch, min. | O'all | Color | Visibility | Dielectric Strength, V/mil | Min. | Max. | Specifications Met | For Use On | Cannot Be Sold To | Each | |
Acrylic Coatings | |||||||||||||
Aerosol Can | |||||||||||||
__ | 12 | 3 | 24 hrs. | Clear | Ultraviolet | 1,000 | -85° | 250° | IPC-CC-830, UL 94 V-0 | Aluminum, Brass, Bronze, Copper, Steel, Stainless Steel | Outside United States and Canada | 0000000 | 000000 |
Bottle | |||||||||||||
1.8 | __ | 10 | 24 hrs. | Clear | Ultraviolet | 1,000 | -85° | 255° | IPC-CC-830, UL 94 V-0 | Plastic | Canada | 00000000 | 00000 |
Pen—0.03" Dia. Point | |||||||||||||
0.16 | __ | 10 | 24 hrs. | Black | Ultraviolet | 1,000 | -85° | 255° | __ | Plastic | Canada | 00000000 | 00000 |
0.16 | __ | 10 | 24 hrs. | Clear | Ultraviolet | 1,000 | -85° | 255° | IPC-CC-830, UL 94 V-0 | Plastic | Canada | 00000000 | 00000 |
0.16 | __ | 10 | 24 hrs. | Green | Ultraviolet | 1,000 | -85° | 255° | __ | Plastic | Canada | 00000000 | 00000 |
0.16 | __ | 10 | 24 hrs. | White | Ultraviolet | 1,000 | -85° | 255° | __ | Plastic | Canada | 00000000 | 00000 |
Acrylic Lacquer Coatings—Sprayon EL2000 | |||||||||||||
Aerosol Can | |||||||||||||
__ | 11 | 10 | 30 min. | Clear | __ | 8,000 | Not Rated | 150° | Fed. Spec. TT-L-50 | Aluminum, Brass, Bronze, Copper, Steel, Stainless Steel | __ | 0000000 | 00000 |
Silicone Coatings—Hard | |||||||||||||
Aerosol Can | |||||||||||||
__ | 12 | 60 | 72 hrs. | Clear | Ultraviolet | 1,100 | -85° | 390° | IPC-CC-830, UL 94 V-0 | Aluminum, Brass, Bronze, Copper, Steel, Stainless Steel | Outside United States and Canada | 0000000 | 00000 |
Silicone/Acrylic Coatings | |||||||||||||
Aerosol Can | |||||||||||||
__ | 12 | 8 | 48 hrs. | Clear | Ultraviolet | 1,000 | -40° | 390° | UL 94 V-0 | Plastic | Canada | 00000000 | 00000 |
Bottle | |||||||||||||
1.8 | __ | 8 | 48 hrs. | Clear | Ultraviolet | 1,000 | -40° | 390° | UL 94 V-0 | Plastic | Canada | 00000000 | 00000 |
Pen—0.03" Dia. Point | |||||||||||||
0.16 | __ | 10 | 48 hrs. | Clear | Ultraviolet | 1,000 | -40° | 390° | UL 94 V-0 | Plastic | Canada | 00000000 | 00000 |
Urethane Coatings | |||||||||||||
Aerosol Can | |||||||||||||
__ | 12 | 15 | 24 hrs. | Clear | Ultraviolet | 380 | -85° | 255° | IPC-CC-830, UL 94 V-0 | Aluminum, Brass, Bronze, Copper, Steel, Stainless Steel | Outside North America | 00000000 | 00000 |
Bottle | |||||||||||||
1.8 | __ | 15 | 30 days | Clear | Ultraviolet | 1,000 | -85° | 255° | IPC-CC-830, UL 94 V-0 | Aluminum, Copper, Stainless Steel | Canada | 00000000 | 00000 |
Heavy Duty Light-Activated Coatings for Electronics
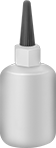
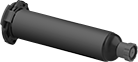
Thinner than potting compounds, these coatings flow easily into small spaces between electrical components. They require an ultraviolet curing lamp to reach full strength. Use them to secure and insulate hardware on printed circuit boards.
Syringe coatings require a gun (sold separately) to dispense.
Dry Time | |||||||||||||
---|---|---|---|---|---|---|---|---|---|---|---|---|---|
Mfr. | Mfr. Model No. | Container Size, fl. oz. | Consistency | Touch, sec. | Overall | Hardness Rating | Dielectric Strength, V/mil | Temp. Range, °F | Light Intensity Requirements to Reach Full Strength | For Use On | Color | Each | |
Bottle Coatings | |||||||||||||
__ | __ | 1 4/5 | Thin Liquid | 10 | 60 sec. | Not Rated | 34,000 | -65° to 350° | 10 seconds @ 7 mW/cm 2 | Aluminum, Brass, Copper, Steel, Stainless Steel, Silver, Titanium, Fiberglass | Amber | 00000000 | 000000 |
Syringe Coatings | |||||||||||||
Loctite® | 3751 | 4/5 | Thin Liquid | 10 | 2 min. | Extra Hard | 730 | -65° to 270° | 10 seconds @ 100 mW/cm 2 | Aluminum, Brass, Bronze, Copper, Steel, Stainless Steel, Silver, Titanium, Plastic, Composites, Fiberglass | Yellow | 00000000 | 00000 |
Dispensing Guns for Syringes | 0000000 | Each | 000000 |
Harsh Environment Coatings for Electronics
High humidity, harsh chemicals, water submersions, and salt are no match for these electronic coatings. They also resist UV light, so they’ll work outdoors. Use them on circuit boards, sensors, and LED drivers in heavy machinery. Also known as conformal coatings, they’re thinner than potting compounds, so they flow into the smallest contours of your components to cover them completely.
PVDF coatings are more flexible than epoxy coatings. They’re IPC certified for use on circuit boards. You can also use them to protect against corrosion on metal joints. To apply, brush or spray them on, or dip your components in.
Epoxy coatings resist impact and wear better than PVDF coatings, and they work in higher temperatures. You can also use them as an adhesive. For controlled pouring, they’re thickened with silicate. These coatings are autoclavable, and they’ll even cure underwater. Dispense them with a mixer nozzle and a gun (each sold separately).
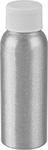
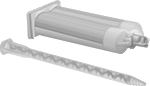
Dry Time | |||||||||||||||
---|---|---|---|---|---|---|---|---|---|---|---|---|---|---|---|
Container Size, fl. oz. | Consistency | Touch | Overall | Mixing Required | Mix Ratio | Mixer Nozzle Included | Dielectric Strength, V/mil | Thermal Conductivity, W/m-K | Temp. Range, °F | Specifications Met | For Use On | Color | Autoclavable | Each | |
PVDF Plastic Coatings—Hard | |||||||||||||||
Bottle | |||||||||||||||
1 | Thick Liquid | 5 min. | 30 min. | No | __ | __ | 750 | 0.2 | -65° to 255° | IPC-CC-830 | Aluminum, Brass, Bronze, Steel, Stainless Steel, Titanium, Cast Iron, Iron, Silver, Plastic, Rubber, Composites, Fiberglass | Clear | Yes | 0000000 | 000000 |
Epoxy Coatings—Extra Hard | |||||||||||||||
Cartridge | |||||||||||||||
1.69 | Thick Liquid | 12 hrs. | 24 hrs. | Yes | 2:1 | No | 500 | Not Rated | -50° to 350° | __ | Aluminum, Brass, Bronze, Steel, Stainless Steel, Titanium, Cast Iron, Iron, Silver, Plastic, Rubber, Composites, Fiberglass | Clear | Yes | 0000000 | 00000 |
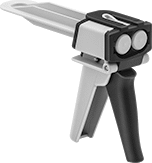
For Cartridge Size | Each | |
1.69 oz. | 00000000 | 000000 |
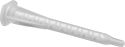
For Cartridge Size | Each | |
1.69 oz. | 00000000 | 00000 |
Heavy Duty High-Purity Coatings for Electronics
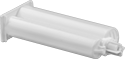
This coating is formulated for use in sensitive applications such as manufacturing semiconductors. Thinner than potting compounds, the coating flows easily into small spaces between electrical components. Use it to secure and insulate hardware on printed circuit boards. Rigid and wear resistant, has excellent chemical and moisture resistance, withstands a wide range of temperatures, and provides excellent electrical insulation. It requires a gun and a mixer nozzle (each sold separately) to dispense.
Certificates with a traceable lot number and product shelf life are available for these products. Download certificates from ORDER HISTORY after your order ships.
Dry Time | ||||||||||
---|---|---|---|---|---|---|---|---|---|---|
Mfr. Model No. | Container Size | Consistency | Touch, min. | Overall, hrs. | Dielectric Strength, V/mil | Temp. Range, °F | For Use On | Color | Each | |
Loctite® Coatings—Extra Hard | ||||||||||
M-21HP | 1.7 fl. oz. | Paste | 20 | 24 | 500 | -65° to 300° | Aluminum, Brass, Bronze, Copper, Steel, Stainless Steel, Titanium, Silver, Plastic, Composites, Fiberglass | Off-White | 0000000 | 000000 |
Heavy Duty High-Purity Light-Activated Coatings for Electronics
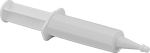
This coating is formulated for use in sensitive applications such as manufacturing semiconductors. Thinner than potting compounds, it flows easily into small spaces between electrical components. The coating begins to harden when exposed to UV light. Use it to secure and insulate hardware on printed circuit boards. It requires a gun (sold separately) to dispense.
Dry Time | |||||||||||
---|---|---|---|---|---|---|---|---|---|---|---|
Mfr. Model No. | Container Size, fl. oz. | Consistency | Touch, sec. | Overall, hrs. | Dielectric Strength, V/mil | Temp. Range, °F | Light Intensity Requirements to Reach Full Strength | For Use On | Color | Each | |
Loctite® Coatings—Medium Soft | |||||||||||
5240 | 0.85 | Thick Liquid | 10 | 72 | 533.4 | -65° to 195° | 60 seconds per side @ 70 mW/cm2 | Aluminum, Brass, Bronze, Copper, Steel, Stainless Steel, Silver, Titanium, Fiberglass, Composites | Green | 0000000 | 000000 |
Dispensing Guns for Syringes | 0000000 | Each | 000000 |
Heavy Duty Heat-Transfer Coatings for Electronics
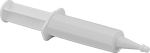
This thermally conductive coating keeps electrical components cool by dissipating heat. Use it to bond transformers, transistors, and other heat-generating components to printed circuit boards and heat sinks. It requires a gun (sold separately) to dispense.
Dry Time | ||||||||||
---|---|---|---|---|---|---|---|---|---|---|
Container Size, fl. oz. | Consistency | Touch, min. | Overall, hrs. | Dielectric Strength, V/mil | Thermal Conductivity, W/m-K | Temp. Range, °F | For Use On | Color | Each | |
1 | Paste | 5 | 2 | 750 | 0.864 | -85° to 347° | Aluminum, Brass, Bronze, Copper, Steel, Stainless Steel, Cast Iron, Iron, Silver, Plastic, Rubber, Composites, Fiberglass | White | 0000000 | 000000 |
Dispensing Guns for Syringes | 0000000 | Each | 000000 |
High-Temperature Coatings for Electronics
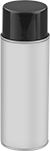
Even in furnace-like heat, these coatings protect your electronics from moisture, dust, and static. They withstand temperatures up to 270° higher than standard silicone coatings while remaining flexible enough to not crack and peel from vibration. Whether your circuit board is in a hot, humid shop or inside heavy machinery that heats up and vibrates, these coatings keep it protected. Made of silicone, they won’t cloud from humidity.
Also known as conformal coatings, they’re thinner than potting compounds, so they flow into the smallest contours of your components to cover them completely. Simply spray these coatings on your device without needing a potting box or other container. They contain a UV indicator, so you can use a blacklight to check if they’ve been applied evenly. You can remove these coatings if necessary.
These coatings are IPC certified for use with circuit boards. For flame retardance, they meet UL 94 V-0. They cannot be sold in California or outside North America due to regulatory limits on VOCs.
Dry Time | ||||||||||||
---|---|---|---|---|---|---|---|---|---|---|---|---|
Container Net Weight, oz. | Touch, min. | Overall, hrs. | Dielectric Strength, V/mil | Temp. Range, °F | Specifications Met | For Use Outdoors | For Use On | Color | Visibility | Cannot Be Sold To | Each | |
Silicone Coatings—Extra Hard | ||||||||||||
12 | 45 | 24 | 560 | -40° to 660° | IPC-CC-830, UL 94 V-0 | No | Aluminum, Copper, Fiberglass | Clear | Ultraviolet | CA, Outside North America | 0000000 | 000000 |
Component-Concealing Coatings for Electronics
Hide proprietary information on electrical components while also protecting them from moisture, dust, and static. All it takes is a single thin layer of these black coatings. They’re often used to protect custom parts while prototyping. Place them under a UV curing lamp to fully harden them in just 5 seconds. Made of urethane, they resist chemicals and scratches and won’t crack in low temperatures. That means they’re great for harsh environments. These coatings meet UL 94 V-0 for flame retardance.
Also known as conformal coatings, they’re thinner than potting compounds, so they flow into the smallest contours to cover your parts completely. They also don’t require a potting box or other container. Dispense these coatings with a gun (sold separately).
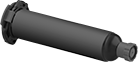
Dry Time | ||||||||||||
---|---|---|---|---|---|---|---|---|---|---|---|---|
Container Size, fl. oz. | Consistency | Touch, sec. | Overall, sec. | Dielectric Strength, V/mil | Temp. Range, °F | Light Intensity Requirements to Reach Full Strength | Cure Type | Specifications Met | For Use On | Color | Each | |
1 | Thick Liquid | 5 | 5 | 1,200 | -40° to 300° | 5 seconds @ 50 mW/cm 2 | UV Light | UL 94 V-0 | Aluminum, Brass, Copper, Steel, Stainless Steel, Silver, Titanium, Fiberglass | Black | 0000000 | 000000 |
Dispensing Guns for Syringes | 0000000 | Each | 000000 |
Optically Clear Coatings for Electronics
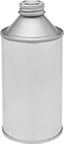
Protect LEDs, solar cells, and fiber optics with a coating that’s clear enough to see through. These coatings let optimal light pass through and repel dust and moisture, so they won’t distort your view of what’s underneath. Made of silicone, they won’t cloud in hot, humid environments. That means they’re great for use outdoors, such as on signs and instrumentation panels. Also known as conformal coatings, these coatings are thinner than potting compounds, flowing into the smallest contours on your device to cover it completely. Silicone conformal coatings are the most flexible kind of conformal coating, so they won’t crack or peel from vibration. To protect sensitive equipment, these coatings also prevent static discharge.
Simply spray these coatings on your device without needing a potting box or other container. Since they cure at room temperature, you won’t need UV lights or cure ovens either. You can remove them if necessary.
These coatings are IPC certified for use with circuit boards. They also meet UL 94 V-0 for flame retardance.
These coatings cannot be sold outside of North America due to regulatory limits on VOCs (volatile organic compounds).
Dry Time | |||||||||||
---|---|---|---|---|---|---|---|---|---|---|---|
Container Size, fl. oz. | Consistency | Touch, min. | Overall, hrs. | Dielectric Strength, V/mil | Temp. Range, °F | Specifications Met | For Use On | Color | Cannot Be Sold To | Each | |
19 | Thin Liquid | 30 | 72 | 720 | -75° to 390° | UL 94 V-0, IPC-CC-830 | Aluminum, Brass, Bronze, Copper, Steel, Stainless Steel, Titanium, Fiberglass, Ceramic, Glass, Composites, Plastic, Rubber, Silver | Clear | Outside North America | 0000000 | 000000 |
Parylene Coatings for Electronics
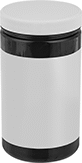
Protect sensitive electronics at the molecular level—these ultra-thin, ultra-conformal coatings cover every inch of your components for applications where failure isn’t an option. They’ve even been trusted on satellites and medical devices. Use them to insulate current, prevent arcs and short circuits, and shield against moisture, chemicals, and gases. They’re better insulators than epoxy, urethane, and silicone coatings. Deposited as vapor in a vacuum chamber, they’re 90% lighter than spray and dip coatings. That means they’ll keep your items lightweight and won’t damage complex geometries. These coatings meet ASTM E595, a standard used by NASA, so they produce almost no volatile emissions that could damage sensitive electronics, even in a vacuum.
Note: These coatings must be applied using special parylene deposition equipment.
Parylene C coatings are the most widely used. They contain chlorine, so they shield against moisture, chemicals, and corrosive gases better than Parylene N coatings. Plus, they’re stronger and quicker to apply.
Parylene N coatings are better electrical insulators than Parylene C coatings. They also penetrate deeper into crevices on your components for more complete coverage. However, they’re slower to apply.
Container Net Weight, lbs. | Consistency | Mixing Required | Dielectric Strength, V/mil | Thermal Conductivity, W/m-K | Max. Temp., °F | Melting Temp., °F | Cure Type | Specifications Met | For Use Outdoors | For Use On | Color | Each | |
Parylene C Coatings—Hard | |||||||||||||
---|---|---|---|---|---|---|---|---|---|---|---|---|---|
1 | Film | No | 5,600 | 0.084 | 175° | 550° | Non-Hardening | ASTM E595 | Yes | Aluminum, Brass, Bronze, Copper, Steel, Stainless Steel | White | 00000000 | 0000000 |
Parylene N Coatings—Hard | |||||||||||||
1 | Film | No | 7,000 | 0.126 | 140° | 785° | Non-Hardening | ASTM E595 | Yes | Aluminum, Brass, Bronze, Copper, Steel, Stainless Steel | White | 00000000 | 000000 |
Heavy Duty EMI/RFI Shielding Coatings for Electronics
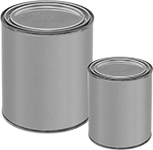
Coat electronics for durability in tough conditions while blocking EMI/RFI signals. Made of epoxy mixed with silver-coated copper, these coatings are stronger than acrylic EMI/RFI coatings. They are rigid enough to withstand the wear of access panels and industrial cabinets. You can also use them in engine compartments because they resist damage from high temperatures and chemicals. Also known as conductive paint, they shield your parts from interference that could cause circuit malfunction and data loss. Mix the two parts of these compounds together and paint them on components. These coatings cannot be sold to Canada due to product labeling requirements.
Dry Time | ||||||||||||
---|---|---|---|---|---|---|---|---|---|---|---|---|
Container Size, fl. oz. | Consistency | Touch, min. | Overall, hrs. | Interference Reduction @ Frequency | Surface Resistivity | Temperature Range, °F | Heating Requirements to Reach Full Strength | For Use On | Color | Cannot Be Sold To | Each | |
27 | Thin Liquid | 5 | 4 | 55 dB @ 1 GHz | 0.31 ohms/sq. | -40° to 245° | 4 hrs. @ 150° F | Aluminum, Steel, Stainless Steel, Ceramic, Glass, Plastic, Chrome, Galvanized Steel | Brown | Canada | 0000000 | 0000000 |
EMI/RFI Shielding Coatings for Electronics
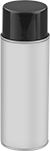
Protect sensitive electronic parts, enclosures, and prototypes from electromagnetic interference (EMI) and radio frequency interference (RFI) with these coatings. Also known as conductive paint, these coatings block EMI and RFI from disrupting electrical, data, and radio signals, which can cause circuit malfunctioning and data loss.
For best adhesion, apply to clean, oil-free surfaces. If applying to highly chemical-resistant plastics such as PVC and PTFE, use a primer first.
Carbon acrylic coatings are made with ground carbon powder mixed with acrylic. They're best for RFI and low-frequency shielding applications, such as protecting jumpers and resistors in initial prototypes, since they're not as conductive as nickel and silver acrylic coatings. They don’t contain metal, so they’re also great for electronics where metal-filled coatings could cause malfunction, such as metal detectors.
Nickel acrylic coatings are made with nickel flakes mixed with acrylic. They’re the best in our offering for protecting magnetic components, since they absorb and redirect magnetic fields. While not as conductive as silver acrylic coatings, they still protect against a broad spectrum of EMI and RFI frequencies. Use them to repair small circuits on circuit boards and to coat devices such as meter and scanner housings. They have good corrosion resistance.
Silver acrylic coatings are made with silver flakes mixed with acrylic. They’re the most conductive coatings in our offering, so they protect against the broadest spectrum of EMI and RFI frequencies. They’re also the most corrosion resistant. Use them to coat portable electronics, access panels, industrial cabinets, and engine control modules.
Coatings that cannot be sold to the listed areas are restricted by product labeling requirements.
Dry Time | Temp. Range, °F | ||||||||||||
---|---|---|---|---|---|---|---|---|---|---|---|---|---|
Container Net Weight, oz. | Consistency | Touch, min. | Overall, hrs. | Interference Reduction @ Frequency | Surface Resistivity, ohms/sq. | Min. | Max. | For Use On | For Use Outdoors | Color | Cannot Be Sold To | Each | |
Carbon Acrylic | |||||||||||||
12 | Thin Liquid | 5 | 24 | 10 dB @ 1 GHz | 100 | -40° | 245° | Plastic | Yes | Black | Canada | 000000000 | 000000 |
Nickel Acrylic | |||||||||||||
12 | Thin Liquid | 5 | 24 | 55 dB @ 1 GHz | 0.49 | -40° | 245° | Plastic | Yes | Gray | Canada | 000000000 | 00000 |
Silver Acrylic | |||||||||||||
12 | Thin Liquid | 30 | 24 | 70 dB @ 1 GHz | 0.10 | Not Rated | 185° | Plastic | No | Silver | __ | 00000000 | 000000 |