Compare over 30 copper, brass, and bronze alloys to find the right material for you—all with material certificates for traceability.
High-Strength 182 Copper Hex Bars
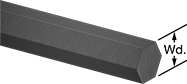
- Yield Strength: 40,000 psi
- Hardness: Rockwell B70 (Medium)
- Temper: H04 (Full Hard)
- Heat Treatable: Yes
182 copper is stronger, harder, and more wear resistant than 110 copper. Also known as RWMA Class 2 chromium copper, it's commonly used in resistance welding, for circuit-breaker parts, and for molds to make plastic parts.
Certificates with a traceable lot number are available for these products. Download certificates from ORDER HISTORY after your order ships.
Ultra-Machinable 360 Brass Hex Bars
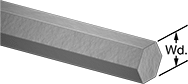
- Yield Strength:
Inch sizes: 25,000 psi
Metric size: 23,000 psi - Hardness:
Inch sizes: Rockwell B55-B80 (Medium)
Metric sizes: Rockwell B75 (Medium) - Temper:
Inch sizes: H02 (1/2 Hard)
Metric sizes: 1/2 Hard - Heat Treatable: No
- Specifications Met:
Inch sizes: ASTM B16
Metric sizes: European Standard EN 12164
With the highest lead content of all the brass alloys, 360 offers the best machinability. Often called free-machining and free-cutting brass, it stands up to high-speed drilling, milling, and tapping operations with minimal wear on your tools. It’s commonly used for gears, pinions, and lock components.
Certificates with a traceable lot number are available for these products. Download certificates from ORDER HISTORY after your order ships.
Wd. | Wd. Tolerance | 1/2 ft. Lg. | 1 ft. Lg. | 2 ft. Lg. | 3 ft. Lg. | 6 ft. Lg. | |
1/8" | -0.006" to 0.006" | 0000000 | |||||
3/16" | -0.006" to 0.006" | 0000000 | |||||
1/4" | -0.006" to 0.006" | 0000000 | |||||
5/16" | -0.006" to 0.006" | 0000000 | |||||
3/8" | -0.006" to 0.006" | 0000000 | |||||
7/16" | -0.006" to 0.006" | 0000000 | |||||
1/2" | -0.006" to 0.006" | 0000000 | |||||
9/16" | -0.006" to 0.006" | 0000000 | |||||
5/8" | -0.006" to 0.006" | 0000000 | |||||
11/16" | -0.006" to 0.006" | 0000000 | |||||
3/4" | -0.006" to 0.006" | 0000000 | |||||
13/16" | -0.006" to 0.006" | 0000000 | |||||
7/8" | -0.006" to 0.006" | 0000000 | |||||
15/16" | -0.006" to 0.006" | 0000000 | |||||
1" | -0.006" to 0.006" | 0000000 | |||||
1 1/8" | -0.006" to 0.006" | 0000000 | |||||
1 1/4" | -0.006" to 0.006" | 0000000 | |||||
1 3/8" | -0.009" to 0.009" | 0000000 | |||||
1 1/2" | -0.009" to 0.009" | 0000000 | |||||
1 5/8" | -0.009" to 0.009" | 0000000 | |||||
1 3/4" | -0.009" to 0.009" | 0000000 | |||||
2" | -0.009" to 0.009" | 0000000 | |||||
2 1/4" | -0.009" to 0.009" | 0000000 | |||||
2 1/2" | -0.009" to 0.009" | 0000000 |
1 m Lg. | |||
---|---|---|---|
Wd., mm | Wd. Tolerance, mm | Each | |
4 | -0.09 to 0.09 | 0000000 | 000000 |
5 | -0.09 to 0.09 | 0000000 | 00000 |
6 | -0.09 to 0.09 | 0000000 | 00000 |
7 | -0.09 to 0.09 | 0000000 | 00000 |
8 | -0.09 to 0.09 | 0000000 | 00000 |
10 | -0.11 to 0.11 | 0000000 | 00000 |
12 | -0.11 to 0.11 | 0000000 | 00000 |
14 | -0.11 to 0.11 | 0000000 | 000000 |
17 | -0.11 to 0.11 | 0000000 | 000000 |
19 | -0.13 to 0.13 | 0000000 | 000000 |
22 | -0.13 to 0.13 | 0000000 | 000000 |
24 | -0.13 to 0.13 | 0000000 | 000000 |