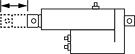
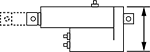
Electric Positioning Slides with Automated Controls
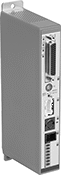
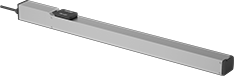
With an included controller and an integrated stepper motor, these slides are a complete precision motion control system. The stepper motor moves the low-friction ball screw and carriage smoothly at high speeds, similar to an inkjet printer head. To make sure the carriage is in the right place, the built-in encoder sends data to the controller. At ± 0.02 mm, these slides have a repeatability thinner than a single strand of hair, so the carriage hits the same spot every time. They work well in automated assemblies and other processes requiring accurate, repeatable motion.
For the initial setup, program the slides using the free, downloadable software, THK D-STEP. No coding necessary—simply enter the target position, speed, and acceleration for up to 16 different slides. This software also records position, speed, and motor current data, so you can monitor performance, optimize motion, and troubleshoot issues.
After the initial setup, the controller stores and runs sequences of up to 512 unique steps on its own. The controller also communicates with other devices such as PLCs, switches, and sensors. This means it can be integrated into a larger automated system to react to or trigger other processes as the carriage moves.
Travel distance per turn, also known as screw lead, is how far the carriage moves with one rotation of the ball screw.
Dynamic load capacity is the maximum load slides can move. If you increase the speed, the dynamic load capacity decreases. Use a load-speed chart to confirm which slides will work for your application. Click on a part number and select "Product Detail" to view the chart.
Dynamic Load Capacity, lbs. | Overall | Carriage | ||||||||||||||
---|---|---|---|---|---|---|---|---|---|---|---|---|---|---|---|---|
Horizontal | Vertical | Max. Speed, mm/s | Travel Distance per Turn, mm | Repeatability, mm | Lg., mm | Wd., mm | Ht., mm | Lg., mm | Wd., mm | Bearing Type | Base Material | Full Load Current | Voltage | Operating System Compatibility | Each | |
100 mm Stroke Length | ||||||||||||||||
2 | 1 | 300 | 6 | ±0.02 | 346 | 32 | 39 | 66.4 | 28 | Ball | Aluminum | 1.5A | 24V DC | Windows XP or Later | 0000000 | 000000000 |
13 | 4 | 500 | 12 | ±0.02 | 356 | 50 | 55 | 71 | 44 | Ball | Aluminum | 1.5A | 24V DC | Windows XP or Later | 0000000 | 00000000 |
22 | 11 | 300 | 6 | ±0.02 | 356 | 50 | 55 | 71 | 44 | Ball | Aluminum | 1.5A | 24V DC | Windows XP or Later | 0000000 | 00000000 |
200 mm Stroke Length | ||||||||||||||||
2 | 1 | 300 | 6 | ±0.02 | 446 | 32 | 39 | 66.4 | 28 | Ball | Aluminum | 1.5A | 24V DC | Windows XP or Later | 0000000 | 00000000 |
13 | 4 | 500 | 12 | ±0.02 | 456 | 50 | 55 | 71 | 44 | Ball | Aluminum | 1.5A | 24V DC | Windows XP or Later | 0000000 | 00000000 |
22 | 11 | 300 | 6 | ±0.02 | 456 | 50 | 55 | 71 | 44 | Ball | Aluminum | 1.5A | 24V DC | Windows XP or Later | 0000000 | 00000000 |
300 mm Stroke Length | ||||||||||||||||
2 | 1 | 300 | 6 | ±0.02 | 546 | 32 | 39 | 66.4 | 28 | Ball | Aluminum | 1.5A | 24V DC | Windows XP or Later | 0000000 | 00000000 |
13 | 4 | 500 | 12 | ±0.02 | 556 | 50 | 55 | 71 | 44 | Ball | Aluminum | 1.5A | 24V DC | Windows XP or Later | 0000000 | 00000000 |
22 | 11 | 300 | 6 | ±0.02 | 556 | 50 | 55 | 71 | 44 | Ball | Aluminum | 1.5A | 24V DC | Windows XP or Later | 0000000 | 00000000 |
400 mm Stroke Length | ||||||||||||||||
13 | 4 | 500 | 12 | ±0.02 | 656 | 50 | 55 | 71 | 44 | Ball | Aluminum | 1.5A | 24V DC | Windows XP or Later | 0000000 | 00000000 |
22 | 11 | 300 | 6 | ±0.02 | 656 | 50 | 55 | 71 | 44 | Ball | Aluminum | 1.5A | 24V DC | Windows XP or Later | 0000000 | 00000000 |
500 mm Stroke Length | ||||||||||||||||
13 | 4 | 500 | 12 | ±0.02 | 756 | 50 | 55 | 71 | 44 | Ball | Aluminum | 1.5A | 24V DC | Windows XP or Later | 0000000 | 00000000 |
22 | 11 | 300 | 6 | ±0.02 | 756 | 50 | 55 | 71 | 44 | Ball | Aluminum | 1.5A | 24V DC | Windows XP or Later | 0000000 | 00000000 |
600 mm Stroke Length | ||||||||||||||||
13 | 4 | 460 | 12 | ±0.02 | 862 | 60 | 60.5 | 75 | 53 | Ball | Aluminum | 1.5A | 24V DC | Windows XP or Later | 0000000 | 00000000 |
22 | 11 | 230 | 6 | ±0.02 | 862 | 60 | 60.5 | 75 | 53 | Ball | Aluminum | 1.5A | 24V DC | Windows XP or Later | 0000000 | 00000000 |
Electric Positioning Slides
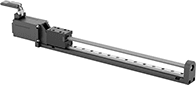
A built-in stepper motor moves the load on these slides smoothly and precisely at high speeds, similar to an inkjet printer head. They’re often used in automated assemblies and other jobs requiring accurate, repeatable motion. The motor moves in small, equal steps and holds its position when stationary, so you don’t need encoders, sensors, or other position feedback devices. With a repeatability thinner than a single sheet of paper, the carriage hits the same spot every time. The slippery coating on the drive screw acts as a permanent dry lubricant, so you won’t need to add lubricant.
All slides require a controller and driver (not included).
Anti-backlash slides minimize play, or how much space there is between the carriage and the drive screw. This keeps the carriage steady for precise positioning.
Dynamic load capacity is the maximum load slides can move. If you increase the speed, the dynamic load capacity decreases. Use a load-speed chart to confirm which slides will work for your application. Click on a part number and select "Product Detail" to view the chart.
Travel distance per full step determines the control you have over the slide's positioning. The smaller the measurement, the finer positioning control you have.
Dynamic Load Cap., lbs. | O'all | Carriage | ||||||||||||||
---|---|---|---|---|---|---|---|---|---|---|---|---|---|---|---|---|
Horizontal | Vertical | Max. Speed, in./sec. | Travel Distance per Full Step | Repeatability | Max. Current per Phase, A | Full Step Increment | No. of Wire Leads | Lg. | Wd. | Ht. | Lg. | Wd. | Bearing Type | Features | Each | |
4" Stroke Lg. | ||||||||||||||||
20 | 15 | 1.4 | 0.00125" | ±0.00125" | 0.75 | 1.8° | 4 | 8.2" | 1.1" | 1.1" | 1.4" | 0.7" | Ball | __ | 0000000 | 0000000 |
20 | 30 | 0.3 | 0.000125" | ±0.00012" | 0.75 | 1.8° | 4 | 8.2" | 1.1" | 1.1" | 1.4" | 0.7" | Ball | __ | 0000000 | 000000 |
6" Stroke Lg. | ||||||||||||||||
135 | 60 | 2 | 0.00125" | ±0.00125" | 1.3 | 1.8° | 4 | 11.4" | 1.7" | 1.7" | 2" | 1.1" | Ball | __ | 0000000 | 000000 |
135 | 75 | 0.4 | 0.00025" | ±0.00025" | 1.3 | 1.8° | 4 | 11.4" | 1.7" | 1.7" | 2" | 1.1" | Ball | __ | 0000000 | 000000 |
135 | 200 | 0.6 | 0.0005" | ±0.00050" | 2.5 | 1.8° | 4 | 12.9" | 2.3" | 2.3" | 2.7" | 1.6" | Ball | __ | 0000000 | 00000000 |
8" Stroke Lg. | ||||||||||||||||
20 | 15 | 1.4 | 0.00125" | ±0.00125" | 0.75 | 1.8° | 4 | 12.2" | 1.1" | 1.1" | 1.4" | 0.7" | Ball | __ | 0000000 | 00000000 |
20 | 30 | 0.3 | 0.000125" | ±0.00012" | 0.75 | 1.8° | 4 | 12.2" | 1.1" | 1.1" | 1.4" | 0.7" | Ball | __ | 0000000 | 00000000 |
12" Stroke Lg. | ||||||||||||||||
15 | 6 | 8 | 0.005" | ±0.001" | 0.7 | 1.8° | 4 | 15.1" | 1.7" | 1.7" | 0.9" | 1.1" | Ball | Anti Backlash | 0000000 | 000000 |
15 | 12 | 4 | 0.0025" | ±0.001" | 0.7 | 1.8° | 4 | 15.1" | 1.7" | 1.7" | 0.9" | 1.1" | Ball | Anti Backlash | 0000000 | 000000 |
135 | 60 | 2 | 0.00125" | ±0.00125" | 1.3 | 1.8° | 4 | 17.4" | 1.7" | 1.7" | 2" | 1.1" | Ball | __ | 0000000 | 00000000 |
135 | 75 | 0.4 | 0.00025" | ±0.00025" | 1.3 | 1.8° | 4 | 17.4" | 1.7" | 1.7" | 2" | 1.1" | Ball | __ | 0000000 | 00000000 |
135 | 85 | 2.9 | 0.0025" | ±0.00250" | 2.5 | 1.8° | 4 | 18.9" | 2.3" | 2.3" | 2.7" | 1.6" | Ball | __ | 0000000 | 00000000 |
135 | 200 | 0.6 | 0.0005" | ±0.00050" | 2.5 | 1.8° | 4 | 18.9" | 2.3" | 2.3" | 2.7" | 1.6" | Ball | __ | 0000000 | 00000000 |
24" Stroke Lg. | ||||||||||||||||
15 | 6 | 8 | 0.005" | ±0.001" | 0.7 | 1.8° | 4 | 27.1" | 1.7" | 1.7" | 0.9" | 1.1" | Ball | Anti Backlash | 0000000 | 00000000 |
15 | 12 | 4 | 0.0025" | ±0.001" | 0.7 | 1.8° | 4 | 27.1" | 1.7" | 1.7" | 0.9" | 1.1" | Ball | Anti Backlash | 0000000 | 00000000 |
Clean Room Electric Positioning Slides
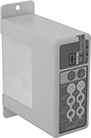
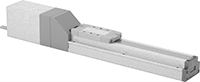
Prevent dust from circulating while precisely positioning parts for drilling, fastening, assembly, and measuring. These slides have a built-in vacuum port to remove fine particles that could damage electronics or contaminate batches in clean rooms. Because they have an integrated stepper motor with an included controller, you can adjust the speed, timing, and positioning with no extra software required. At ± 0.02 mm, these slides have a repeatability thinner than a single sheet of paper, so the carriage hits the same spot every time. Unlike air-powered actuators, they’ll hold their position even if power fails. They’re also more energy efficient.
Dynamic load capacity is the maximum load slides can move. If you increase the speed, the dynamic load capacity decreases. Use a load-speed chart to confirm which slides will work for your application. Click on a part number and select "Product Detail" to view the chart.
Maximum speed is how fast the slide will move under no-load conditions. If you increase the load, the slide speed will decrease.
Travel distance per full step determines the control you have over the slide’s positioning. The smaller the measurement, the finer positioning control you have.
Travel distance per turn, also known as screw lead, is how far the carriage moves with one rotation of the ball screw.
Dynamic Load Cap., lbs. | Travel Distance per | Overall | Carriage | ||||||||||||||
---|---|---|---|---|---|---|---|---|---|---|---|---|---|---|---|---|---|
Horizontal | Vertical | Max. Speed, mm/s | Full Step, mm | Turn, mm | Repeatability, mm | Lg., mm | Wd., mm | Ht., mm | Lg., mm | Wd., mm | Bearing Type | Base Material | Full Load Current | Voltage | Environmental Rating | Each | |
200 mm Stroke Length | |||||||||||||||||
110 | 44 | 250 | 0.08 | 8 | ±0.02 | 541 | 70 | 84 | 122 | 60 | Ball | Aluminum | 5A | 24V DC | Fed. Std. Class 10, ISO Class 4 | 0000000 | 000000000 |
143 | 50 | 250 | 0.1 | 10 | ±0.02 | 614.5 | 90 | 85.5 | 170 | 74 | Ball | Aluminum | 5A | 24V DC | Fed. Std. Class 10, ISO Class 4 | 0000000 | 00000000 |
300 mm Stroke Length | |||||||||||||||||
110 | 44 | 250 | 0.08 | 8 | ±0.02 | 641 | 70 | 84 | 122 | 60 | Ball | Aluminum | 5A | 24V DC | Fed. Std. Class 10, ISO Class 4 | 0000000 | 00000000 |
400 mm Stroke Length | |||||||||||||||||
110 | 44 | 250 | 0.08 | 8 | ±0.02 | 741 | 70 | 84 | 122 | 60 | Ball | Aluminum | 5A | 24V DC | Fed. Std. Class 10, ISO Class 4 | 0000000 | 00000000 |
143 | 50 | 250 | 0.1 | 10 | ±0.02 | 814.5 | 90 | 85.5 | 170 | 74 | Ball | Aluminum | 5A | 24V DC | Fed. Std. Class 10, ISO Class 4 | 0000000 | 00000000 |
600 mm Stroke Length | |||||||||||||||||
143 | 50 | 250 | 0.1 | 10 | ±0.02 | 1,014.5 | 90 | 85.5 | 170 | 74 | Ball | Aluminum | 5A | 24V DC | Fed. Std. Class 10, ISO Class 4 | 0000000 | 00000000 |
800 mm Stroke Length | |||||||||||||||||
143 | 50 | 250 | 0.1 | 10 | ±0.02 | 1,214.5 | 90 | 85.5 | 170 | 74 | Ball | Aluminum | 5A | 24V DC | Fed. Std. Class 10, ISO Class 4 | 0000000 | 00000000 |
Electric Actuators with Automated Controls
Automate precise push and pull movements in clamping, sorting, and ejecting tasks. These actuators come ready to use with a stepper motor and driver built in. At ±0.02 mm, their repeatability is thinner than a strand of hair, so the rod hits the same spot every time. Compared to air-powered systems, they have fewer parts to repair and replace.
These actuators have integrated controls for quick and easy setup, or you can program start and end positions remotely using digital IO or IO-Link. With IO-Link, you can move loads to a specific point along the stroke length, instead of just fully extending and retracting the rod. You can also back up your settings, configure parameters, and update firmware.
Power these actuators with a T-coded, 4-pole M12 connector. To send signals, use an A-coded, 8-pole M12 connector.
Use brackets to attach an actuator to your equipment. Support brackets have a groove for connecting to the side of the actuator body. Flange brackets connect to the bottom of the actuator and can be positioned anywhere along its length. Mounting, trunnion, and pivot brackets connect to the front of the actuator.
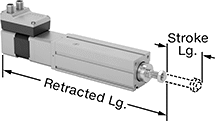
Extension Rod | ||||||||||
---|---|---|---|---|---|---|---|---|---|---|
Stroke Lg., mm | Voltage | Full Load Current, A | Max. Speed, in./sec. | Repeatability, mm | Extension Rod Type | Dia. | Thread Size | Retracted Lg. | Each | |
15 lbs. Dynamic Pull/Push Load | ||||||||||
50 | 24V DC | 3 | 8.267 | ±0.02 | Nonrotating | 0.4" | M8 × 1.25 mm | 10 1/8" | 0000000 | 000000000 |
100 | 24V DC | 3 | 8.267 | ±0.02 | Nonrotating | 0.4" | M8 × 1.25 mm | 12" | 0000000 | 00000000 |
200 | 24V DC | 3 | 8.267 | ±0.02 | Nonrotating | 0.4" | M8 × 1.25 mm | 16" | 0000000 | 00000000 |
50 lbs. Dynamic Pull/Push Load | ||||||||||
50 | 24V DC | 3 | 2.913 | ±0.02 | Nonrotating | 0.48" | M10 × 1.25 mm | 10 7/8" | 0000000 | 00000000 |
100 | 24V DC | 3 | 2.913 | ±0.02 | Nonrotating | 0.48" | M10 × 1.25 mm | 12 7/8" | 0000000 | 00000000 |
150 | 24V DC | 3 | 2.913 | ±0.02 | Nonrotating | 0.48" | M10 × 1.25 mm | 14 7/8" | 0000000 | 00000000 |
200 | 24V DC | 3 | 2.913 | ±0.02 | Nonrotating | 0.48" | M10 × 1.25 mm | 16 3/4" | 0000000 | 00000000 |
300 | 24V DC | 3 | 2.913 | ±0.02 | Nonrotating | 0.48" | M10 × 1.25 mm | 20 3/4" | 0000000 | 00000000 |
100 lbs. Dynamic Pull/Push Load | ||||||||||
50 | 24V DC | 5.3 | 3.543 | ±0.02 | Nonrotating | 0.63" | M12 × 1.25 mm | 12 1/8" | 0000000 | 00000000 |
100 | 24V DC | 5.3 | 3.543 | ±0.02 | Nonrotating | 0.63" | M12 × 1.25 mm | 14 1/8" | 0000000 | 00000000 |
150 | 24V DC | 5.3 | 3.543 | ±0.02 | Nonrotating | 0.63" | M12 × 1.25 mm | 16" | 0000000 | 00000000 |
200 | 24V DC | 5.3 | 3.543 | ±0.02 | Nonrotating | 0.63" | M12 × 1.25 mm | 18" | 0000000 | 00000000 |
300 | 24V DC | 5.3 | 3.543 | ±0.02 | Nonrotating | 0.63" | M12 × 1.25 mm | 22" | 0000000 | 00000000 |
400 | 24V DC | 5.3 | 3.543 | ±0.02 | Nonrotating | 0.63" | M12 × 1.25 mm | 25 7/8" | 0000000 | 00000000 |
500 | 24V DC | 5.3 | 3.543 | ±0.02 | Nonrotating | 0.63" | M12 × 1.25 mm | 29 7/8" | 0000000 | 00000000 |





For Rod Dia. | Material | Mounting Hardware Included | Each | |
Support Brackets | ||||
---|---|---|---|---|
0.4" | Anodized Aluminum | __ | 0000000 | 000000 |
0.48", 0.63" | Anodized Aluminum | __ | 0000000 | 00000 |
Flange Bracket | ||||
0.4" | Galvanized Steel | Yes | 0000000 | 00000 |
0.48" | Galvanized Steel | Yes | 0000000 | 00000 |
0.63" | Galvanized Steel | Yes | 0000000 | 000000 |
Mounting Bracket | ||||
0.4" | Galvanized Steel | Yes | 0000000 | 000000 |
0.48" | Galvanized Steel | Yes | 0000000 | 000000 |
0.63" | Galvanized Steel | Yes | 0000000 | 000000 |
Trunnion Brackets | ||||
0.4" | Anodized Aluminum | __ | 0000000 | 000000 |
0.48" | Anodized Aluminum | __ | 0000000 | 000000 |
0.63" | Anodized Aluminum | __ | 0000000 | 000000 |
Pivot Bracket | ||||
0.4" | Galvanized Steel | Yes | 0000000 | 000000 |
0.48" | Galvanized Steel | Yes | 0000000 | 000000 |
0.63" | Galvanized Steel | Yes | 0000000 | 000000 |
Low-Temperature Electric Positioning Slides
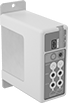
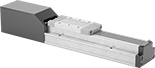
Precisely position parts in conditions as cold as -90° F. These slides contain a grease that lubricates even in low temperatures. With an integrated stepper motor, they’re a complete motion control system for automated assemblies. A controller is included, so you can adjust the speed, timing, and positioning with no extra software required. These slides are often used in actions that require fine, repeatable movement, such as drilling, fastening, assembly, and measuring. The carriage extends the same distance every time within ±0.02 mm, a margin thinner than a sheet of paper.
Dynamic load capacity is the maximum load slides can move. If you increase the speed, the dynamic load capacity decreases. Use a load-speed chart to confirm which slides will work for your application. Click on a part number and select "Product Detail" to view the chart.
Travel distance per full step determines the control you have over the slide’s positioning. The smaller the measurement, the finer positioning control you have.
Travel distance per turn, also known as screw lead, is how far the carriage moves with one rotation of the ball screw.
Dynamic Load Capacity, lbs. | Travel Distance per | Overall | Carriage | |||||||||||||
---|---|---|---|---|---|---|---|---|---|---|---|---|---|---|---|---|
Horizontal | Vertical | Max. Speed, mm/s | Full Step, mm | Turn, mm | Repeatability, mm | Lg., mm | Wd., mm | Ht., mm | Lg., mm | Wd., mm | Bearing Type | Base Material | Full Load Current | Voltage | Each | |
100 mm Stroke Length | ||||||||||||||||
44 | 16 | 500 | 0.06 | 12 | ±0.02 | 336 | 60 | 57.5 | 102 | 50 | Roller | Aluminum | 2.4A | 24V DC | 0000000 | 000000000 |
200 mm Stroke Length | ||||||||||||||||
44 | 16 | 500 | 0.06 | 12 | ±0.02 | 436 | 60 | 57.5 | 102 | 50 | Roller | Aluminum | 2.4A | 24V DC | 0000000 | 00000000 |
88 | 22 | 250 | 0.08 | 16 | ±0.02 | 482 | 70 | 79 | 122 | 60 | Roller | Aluminum | 5.2A | 24V DC | 0000000 | 00000000 |
300 mm Stroke Length | ||||||||||||||||
44 | 16 | 500 | 0.06 | 12 | ±0.02 | 536 | 60 | 57.5 | 102 | 50 | Roller | Aluminum | 2.4A | 24V DC | 0000000 | 00000000 |
400 mm Stroke Length | ||||||||||||||||
88 | 22 | 250 | 0.08 | 16 | ±0.02 | 682 | 70 | 79 | 122 | 60 | Roller | Aluminum | 5.2A | 24V DC | 0000000 | 00000000 |
600 mm Stroke Length | ||||||||||||||||
88 | 22 | 250 | 0.08 | 16 | ±0.02 | 882 | 70 | 79 | 122 | 60 | Roller | Aluminum | 5.2A | 24V DC | 0000000 | 00000000 |
Miniature Electric Actuators with Automated Controls
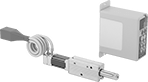
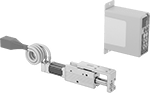
Smaller than any other actuator in our offering, these actuators’ short stroke length makes them good for automating fine, precise adjustments. They’re often used for aligning, pressing, and diverting. They come with an all-in-one motion control system to set the speed, timing, and position with buttons—no programming is required.
Rod-style actuators have threads on the front of the rod.
Slide table-style actuators give you setup flexibility, since you can mount equipment on top or in front. Mount on top to reduce the space you need to move a full stroke length.
Lg. | Dynamic Load Capacity, lbs. | Extension Rod | |||||||||||||
---|---|---|---|---|---|---|---|---|---|---|---|---|---|---|---|
Stroke | Retracted | Voltage | Full Load Current, A | Horizontal | Vertical | Max. Speed, in./sec. | Repeatability, mm | Extension Rod Type | End Type | Dia. | Thread Size | Thread Pitch, mm | Environmental Rating | Each | |
Rod Actuator Style | |||||||||||||||
1" | 5 3/8" | 24V DC | 0.9 | 2 | 1 | 5.91 | ±0.05 | Nonrotating | Threaded | 0.47" | M4 | 0.7 | IP40 | 0000000 | 0000000 |
1" | 5 7/8" | 24V DC | 2.2 | 4 | 3 | 7.87 | ±0.05 | Nonrotating | Threaded | 0.55" | M5 | 0.8 | IP40 | 0000000 | 000000 |
2" | 6 1/2" | 24V DC | 0.9 | 2 | 1 | 5.91 | ±0.05 | Nonrotating | Threaded | 0.47" | M4 | 0.7 | IP40 | 0000000 | 000000 |
2" | 6 7/8" | 24V DC | 2.2 | 4 | 3 | 7.87 | ±0.05 | Nonrotating | Threaded | 0.55" | M5 | 0.8 | IP40 | 0000000 | 000000 |
3" | 7 7/8" | 24V DC | 0.9 | 2 | 1 | 5.91 | ±0.05 | Nonrotating | Threaded | 0.47" | M4 | 0.7 | IP40 | 0000000 | 000000 |
3" | 8 1/4" | 24V DC | 2.2 | 4 | 3 | 7.87 | ±0.05 | Nonrotating | Threaded | 0.55" | M5 | 0.8 | IP40 | 0000000 | 000000 |
Slide Table Actuator Style | |||||||||||||||
1" | 5 1/2" | 24V DC | 0.9 | 2 | 1 | 5.91 | ±0.05 | Nonrotating | Unthreaded | 0.47" | __ | __ | IP40 | 0000000 | 000000 |
1" | 6" | 24V DC | 2.2 | 4 | 3 | 7.87 | ±0.05 | Nonrotating | Unthreaded | 0.55" | __ | __ | IP40 | 0000000 | 000000 |
2" | 6 5/8" | 24V DC | 0.9 | 2 | 1 | 5.91 | ±0.05 | Nonrotating | Unthreaded | 0.47" | __ | __ | IP40 | 0000000 | 000000 |
2" | 9" | 24V DC | 2.2 | 4 | 3 | 7.87 | ±0.05 | Nonrotating | Unthreaded | 0.55" | __ | __ | IP40 | 0000000 | 000000 |
Low-Profile Electric Positioning Slides with Automated Controls
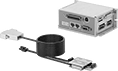
Less than one-third the height of standard electric positioning slides, these slides push and pull small parts in electronics manufacturing, robotics, and other automated processes. They have a magnetic linear motor to generate fast and precise motion while taking up only a tiny footprint. With a controller and driver also included, they’re an all-in-one actuation system. Use them where extreme precision is needed—they have a repeatability of ±0.5 microns, which is 1/50,000th of an inch.
Download free CME2 software during initial setup for easy, point-and-click programming. Controllers using CME2 can store and run sequences of up to 32 steps. For added speed and flexibility, these slides are also compatible with CPL, used to write advanced custom programs.
Dynamic load capacity is the maximum load slides can move. If you increase the speed, the dynamic load capacity decreases. Use a load-speed chart to confirm which slides will work for your application. Click on a part number and select "Product Detail" to view the chart.
Overall | Carriage | ||||||||||||||
---|---|---|---|---|---|---|---|---|---|---|---|---|---|---|---|
Lg., mm | Wd., mm | Ht., mm | Lg., mm | Wd., mm | Bearing Type | Dynamic Horizontal Load Capacity, lbs. | Max. Speed, mm/s | Travel Distance per Full Step, mm | Repeatability, microns | Base Material | Full Load Current | Voltage | Operating System Compatibility | Each | |
10 mm Stroke Length | |||||||||||||||
62 | 38 | 11 | 38 | 26 | Ball | 1 | 500 | 0.0005 | ±0.5 | Nickel-Plated Steel | 3A | 24V DC | Windows 10 or Later | 0000000 | 000000000 |
18 mm Stroke Length | |||||||||||||||
86 | 38 | 11 | 54 | 26 | Ball | 1 | 500 | 0.0005 | ±0.5 | Nickel-Plated Steel | 3A | 24V DC | Windows 10 or Later | 0000000 | 00000000 |
25 mm Stroke Length | |||||||||||||||
120 | 55 | 14 | 80 | 48 | Ball | 11 | 1,300 | 0.0005 | ±0.5 | Nickel-Plated Steel | 1.2A | 48V DC | Windows 10 or Later | 0000000 | 00000000 |
120 | 80 | 16 | 80 | 68 | Ball | 11 | 1,300 | 0.0005 | ±0.5 | Nickel-Plated Steel | 1A | 48V DC | Windows 10 or Later | 0000000 | 00000000 |
65 mm Stroke Length | |||||||||||||||
160 | 55 | 14 | 80 | 48 | Ball | 11 | 1,300 | 0.0005 | ±0.5 | Nickel-Plated Steel | 2.4A | 48V DC | Windows 10 or Later | 0000000 | 00000000 |
160 | 80 | 16 | 80 | 68 | Ball | 11 | 1,300 | 0.0005 | ±0.5 | Nickel-Plated Steel | 2.1A | 48V DC | Windows 10 or Later | 0000000 | 00000000 |
120 mm Stroke Length | |||||||||||||||
280 | 80 | 16 | 140 | 68 | Ball | 11 | 1,300 | 0.0005 | ±0.5 | Nickel-Plated Steel | 2.1A | 48V DC | Windows 10 or Later | 0000000 | 00000000 |
Positioning Slides for Universal Robots
![]() Shown with Robot Arm (Not Included) | ![]() |
![]() |
Extend the horizontal reach of your Universal Robots’ arm to operate your robot at multiple positions along an assembly line, or transport workpieces from a conveyor to your CNC. All of these slides have a carriage, slide controller, and software plug-in for connecting, operating, and programming your robot’s arm. The slides become an extension of the arm, so you can program how they glide back and forth on the rail as part of the robot's work cycle. A cable management system keeps your cables from tangling while the slides are in motion.
These slides are all Universal Robots+ (UR+) certified products, and have been validated by Universal Robots for compatibility and simple integration with UR robot arms. Pair them with Telescoping Bases for Universal Robots to also extend the vertical reach of your robot’s arm.
Overall | Carriage | Load Capacity, lbs. | Robot Mount. Location | Floor Mount. Location | |||||||||||
---|---|---|---|---|---|---|---|---|---|---|---|---|---|---|---|
Lg., mm | Wd., mm | Ht., mm | Travel Lg., mm | Position Accuracy, mm | Lg., mm | Wd., mm | Dynamic | Static | Mount. Hole Dia. (No. of Holes) | Mount. Fasteners Included | Mount. Hole Dia. (No. of Holes) | Mount. Fasteners Included | Includes | Each | |
For UR3e, UR5e, UR10e, UR16e Series | |||||||||||||||
Aluminum | |||||||||||||||
1,245 | 150 | 190 | 700 | ±0.1 | 170 | 200 | 2,450 | 2,700 | 6mm, 8mm (4) | Yes | 6mm (10) | No | Slide Controller, Software Plug-In for Universal Robots | 0000000 | 0000000000 |
1,550 | 150 | 190 | 1,000 | ±0.1 | 170 | 200 | 2,450 | 2,700 | 6mm, 8mm (4) | Yes | 6mm (10) | No | Slide Controller, Software Plug-In for Universal Robots | 0000000 | 000000000 |
1,855 | 150 | 190 | 1,300 | ±0.1 | 170 | 200 | 2,450 | 2,700 | 6mm, 8mm (4) | Yes | 6mm (10) | No | Slide Controller, Software Plug-In for Universal Robots | 0000000 | 000000000 |
2,160 | 150 | 190 | 1,600 | ±0.1 | 170 | 200 | 2,450 | 2,700 | 6mm, 8mm (4) | Yes | 6mm (10) | No | Slide Controller, Software Plug-In for Universal Robots | 0000000 | 000000000 |
2,337 | 150 | 190 | 1,800 | ±0.1 | 170 | 200 | 2,450 | 2,700 | 6mm, 8mm (4) | Yes | 6mm (10) | No | Slide Controller, Software Plug-In for Universal Robots | 0000000 | 000000000 |