Casting Metals
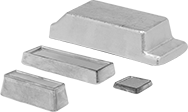
Melt and pour these alloys into molds to create metal parts and prototypes.
Bismuth and indium alloys expand slightly as they solidify, pushing into the crevices of a mold to produce detailed replicas. These alloys are useful for repairing dies, creating fusible links, and holding delicate parts for machining. Indium alloys have a low melting temperature so they can be cast in molds made from glass, quartz, mica, and ceramic.
Lead can be used for caulking, castings, and hot-dipped coatings.
Lead-base babbitt is a soft alloy. Use it to cast light-load bearings. It has superior antifriction properties.
Lead-base coppered babbitt is able to withstand shock and vibration and requires less lubrication than other types of babbitt. Use it to cast bearings for low-speed, heavy-load applications.
Lead hammer metal is commonly used to cast nonmarring hammer heads. This ductile material is hard and won't chip.
Lead-free pewter alloy can be used as an alternative to lead. This alloy has less copper than standard pewter, which makes it easier to pour when melted.
Tin-base babbitt is used to cast bearings for high-speed, high-wear applications and can withstand heavy, sustained loads. It has a higher melting temperature than lead-base babbitt.
Zinc alloy is nonshrinking and corrosion resistant. Parts cast from this material are easy to machine.
Silicon-bronze alloy is often used to cast gears, propellers, bells, and plaques. It renders an excellent surface finish.
Aluminum alloy has good castability, weldability, and corrosion resistance. Castings made from aluminum can be heat treated to increase hardness and strength.
Material Composition | Approximate | ||||||||||
---|---|---|---|---|---|---|---|---|---|---|---|
Melting Temperature, °F | Bismuth | Lead | Tin | Cadmium | Thick. | Wd. | Lg. | Wt., lbs. | Each | ||
158° | 50% | 27% | 13% | 10% | 1/2" | 3" | __ | 1 | Hex Ingot | 0000000 | 000000 |
160° | 43% | 38% | 11% | 8% | 1/2" | 1 1/2" | 4 1/2" | 1 | Sheet and Bar | 0000000 | 00000 |
203° | 53% | 32% | 15% | __ | 3/4" | 1" | 3" | 1 | Sheet and Bar | 0000000 | 00000 |
255° | 56% | 44% | __ | __ | 1/2" | 3" | 3" | 1 | Sheet and Bar | 0000000 | 00000 |
281° | 40% | __ | 60% | __ | 1/2" | 1 1/2" | 4 1/2" | 1 | Sheet and Bar | 0000000 | 00000 |
281° | 58% | __ | 42% | __ | 1/2" | 1 1/2" | 5 1/2" | 1 | Sheet and Bar | 0000000 | 00000 |
Material Composition | Approximate | ||||||||||||
---|---|---|---|---|---|---|---|---|---|---|---|---|---|
Melting Temperature, °F | Bismuth | Lead | Indium | Tin | Cadmium | Thick. | Wd. | Lg. | Dia. | Wt., lbs. | Each | ||
117° | 45% | 23% | 19% | 8% | 5% | 1/4" | 2" | 4 1/2" | __ | 1/2 | Sheet and Bar | 0000000 | 0000000 |
136° | 49% | 18% | 21% | 12% | __ | 1/4" | 1 7/8" | 4 1/2" | __ | 1/2 | Sheet and Bar | 0000000 | 000000 |
140° | 48% | 25% | 5% | 13% | 9% | 1/2" | __ | __ | 3 1/2" | 1 | Rod and Disc | 00000000 | 000000 |
147° | 48% | 25% | 4% | 13% | 10% | 1/2" | __ | __ | 3 1/2" | 1 | Rod and Disc | 00000000 | 000000 |
Approximate | |||||||||
---|---|---|---|---|---|---|---|---|---|
Melting Temperature, °F | Material Composition, Lead | Thick. | Wd. | Lg. | Wt., lbs. | Specifications Met | Each | ||
621° | 99.9% | 1" | 2" | 8 3/4" | 5 | Ingot | ASTM B29 | 000000 | 000000 |
Material Composition | Approximate | |||||||||
---|---|---|---|---|---|---|---|---|---|---|
Melting Temperature, °F | Lead | Tin | Antimony | Thick. | Wd. | Lg. | Wt., lbs. | Each | ||
459° | 80% | 5% | 15% | 1 1/8" | 1 5/8" | 7 1/2" | 5 | Sheet and Bar | 0000000 | 0000000 |
Material Composition | Approximate | ||||||||||
---|---|---|---|---|---|---|---|---|---|---|---|
Melting Temperature, °F | Lead | Tin | Antimony | Copper | Arsenic | Thick. | Dia. | Wt., lbs. | Each | ||
625° | 75% | 10% | 14% | 0.3% | 0.5% | 1 1/2" | 3 3/4" | 4 1/2 | Rod and Disc | 0000000 | 0000000 |
Material Composition | Approximate | ||||||||
---|---|---|---|---|---|---|---|---|---|
Melting Temperature, °F | Lead | Antimony | Thick. | Wd. | Lg. | Wt., lbs. | Each | ||
430° | 94% | 6% | 1 1/8" | 1 5/8" | 6 5/8" | 5 | Sheet and Bar | 0000000 | 000000 |
Material Composition | Approximate | |||||||||
---|---|---|---|---|---|---|---|---|---|---|
Melting Temperature, °F | Tin | Antimony | Copper | Thick. | Wd. | Lg. | Wt., lbs. | Each | ||
525° | 92% | 7% | 0.3% | 1/2" | 1" | 11 1/2" | 1 | Sheet and Bar | 0000000 | 000000 |
Material Composition | Approximate | |||||||||
---|---|---|---|---|---|---|---|---|---|---|
Melting Temperature, °F | Tin | Antimony | Copper | Thick. | Wd. | Lg. | Wt., lbs. | Each | ||
669° | 89% | 7% | 4% | 1 1/2" | 2" | 5 1/2" | 4 1/2 | Sheet and Bar | 0000000 | 0000000 |
Material Composition | Approximate | |||||||||
---|---|---|---|---|---|---|---|---|---|---|
Melting Temperature, °F | Zinc | Copper | Aluminum | Thick. | Wd. | Lg. | Wt., lbs. | Each | ||
740° | 95% | 0.1% | 4% | 1 1/4" | 2 3/4" | 6 1/4" | 4 1/2 | Ingot | 000000 | 000000 |
Material Composition | |||||||
---|---|---|---|---|---|---|---|
Melting Temperature, °F | Zinc | Copper | Silicon | Approximate Wt., lbs. | Each | ||
1,780° | 4% | 92% | 4% | 1 | Ingot | 0000000 | 000000 |
Material Composition | Approximate | |||||||||
---|---|---|---|---|---|---|---|---|---|---|
Melting Temperature, °F | Aluminum | Silicon | Iron | Thick. | Wd. | Lg. | Wt., lbs. | Each | ||
1,035° | 92.5% | 7% | 0.3% | 4" | 4" | 18" | 20 | Ingot | 00000000 | 0000000 |