Selecting Compatible Lead Screws and Nuts
More
About Linear Bearings
More
Ultra-Thin Linear Sleeve Bearings

Thinner than standard linear sleeve bearings, these bearings fit where clearance is a concern. Pair them with round end-supported shafts. They have fixed alignment, so they’re best for applications where shaft misalignment is unlikely. The PTFE lining stands up to chemicals and won’t scratch the shaft. To install, slide them into a housing (not included).
For Shaft Diameter, mm | Overall Length, mm | For Housing ID, mm | With Retaining Ring Grooves | Dynamic Load Capacity | Static Load Capacity, lbs. | Shaft Clearance, mm | Temperature Range, °F | For Shaft Material | Each | |
Fixed Alignment | ||||||||||
---|---|---|---|---|---|---|---|---|---|---|
PTFE-Lined 6061 Aluminum Bearings | ||||||||||
6 | 22 | 12.000 to 12.018 | No | 70 lbs. @ 100 fpm | 760 | 0.038 | -400° to 375° | Stainless Steel, Steel | 0000000 | 000000 |
8 | 24 | 15.000 to 15.018 | No | 80 lbs. @ 100 fpm | 1,100 | 0.038 | -400° to 375° | Stainless Steel, Steel | 0000000 | 00000 |
10 | 26 | 17.000 to 17.018 | No | 250 lbs. @ 100 fpm | 1,500 | 0.038 | -400° to 375° | Stainless Steel, Steel | 0000000 | 00000 |
12 | 28 | 19.000 to 19.021 | No | 250 lbs. @ 100 fpm | 1,950 | 0.038 | -400° to 375° | Stainless Steel, Steel | 0000000 | 00000 |
14 | 28 | 21.000 to 21.021 | No | 300 lbs. @ 100 fpm | 2,250 | 0.038 | -400° to 375° | Stainless Steel, Steel | 0000000 | 00000 |
16 | 30 | 24.000 to 24.021 | No | 350 lbs. @ 100 fpm | 2,750 | 0.05 | -400° to 375° | Stainless Steel, Steel | 0000000 | 00000 |
20 | 30 | 28.000 to 28.021 | No | 450 lbs. @ 100 fpm | 3,450 | 0.05 | -400° to 375° | Stainless Steel, Steel | 0000000 | 00000 |
25 | 40 | 35.000 to 35.025 | No | 600 lbs. @ 100 fpm | 5,800 | 0.05 | -400° to 375° | Stainless Steel, Steel | 0000000 | 00000 |
50 | 70 | 62.000 to 62.023 | No | 2,000 lbs. @ 100 fpm | 20,300 | 0.0625 | -400° to 375° | Stainless Steel, Steel | 0000000 | 00000 |
Linear Bearings for Ball Splines
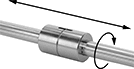

Combine these bearings with a ball spline to create a compact linear and rotary motion system for applications with fast, complex movements, such as robotics. These bearings move smoothly and precisely even at high speeds along ball splines while grooves on the ball spline transmit rotary power. Clip a retaining ring into the groove on these bearings to position them in your system. Use the keyway and included machine key for attaching your load.
Stainless steel bearings are more corrosion resistant than steel bearings.
Splines are alloy steel for high strength and wear resistance. They're hardened only on the outside, so they stand up to repeated motion while keeping their center soft enough to absorb stress from shifting loads. Those with a step-down end have a shoulder near the end to stop gears, sprockets, and bearings.
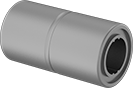

Groove | Keyway | ||||||||||||||||
---|---|---|---|---|---|---|---|---|---|---|---|---|---|---|---|---|---|
For Spline Dia., mm | For No. of Splines | Overall Lg., mm | OD, mm | Dynamic Load Capacity, lbs. | Static Load Capacity, lbs. | Max. Dynamic Torque, in.-lbs. | Max. Static Torque, in.-lbs. | Max. Temp., °F | With Retaining Ring Grooves | Wd., mm | Dia., mm | Includes | Lg., mm | Wd., mm | Dp., mm | Each | |
6 | 4 | 25 | 14 | 270 | 510 | 13 | 21 | 176° | Yes | 1.3 | 13.3 | Machine Key | 10.5 | 2.5 | 1.2 | 00000000 | 000000 |
8 | 4 | 25 | 16 | 325 | 645 | 18 | 32 | 176° | Yes | 1.3 | 15.3 | Machine Key | 10.5 | 2.5 | 1.2 | 00000000 | 00000 |
10 | 4 | 33 | 21 | 610 | 1,100 | 38 | 72 | 176° | Yes | 1.7 | 20 | Machine Key | 13 | 3 | 1.5 | 00000000 | 00000 |
13 | 4 | 36 | 24 | 600 | 1,050 | 185 | 346 | 176° | Yes | 1.3 | 22.7 | Machine Key | 15 | 3 | 1.5 | 00000000 | 00000 |
16 | 4 | 50 | 31 | 1,350 | 2,500 | 531 | 973 | 176° | Yes | 1.6 | 29.4 | Machine Key | 17.5 | 3.5 | 2 | 00000000 | 00000 |
18.2 | 4 | 60 | 32 | 1,750 | 2,500 | 734 | 1,177 | 176° | Yes | 3.1 | 30.2 | Machine Key | 26 | 4 | 2.5 | 00000000 | 000000 |
25 | 4 | 71 | 42 | 2,850 | 5,250 | 1,672 | 3,062 | 176° | Yes | 2.5 | 39.5 | Machine Key | 36 | 4 | 2.5 | 00000000 | 000000 |
28 | 4 | 80 | 45 | 4,150 | 5,200 | 2,557 | 3,646 | 176° | Yes | 4.15 | 42.6 | Machine Key | 41 | 7 | 4 | 00000000 | 000000 |
30 | 4 | 80 | 47 | 4,150 | 5,200 | 2,716 | 3,885 | 176° | Yes | 3 | 44 | Machine Key | 42 | 4 | 2.5 | 00000000 | 000000 |
40 | 4 | 100 | 64 | 6,900 | 8,400 | 5,964 | 8,266 | 176° | Yes | 4 | 60 | Machine Key | 52 | 6 | 3.5 | 00000000 | 000000 |
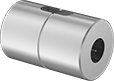

Groove | Keyway | ||||||||||||||||
---|---|---|---|---|---|---|---|---|---|---|---|---|---|---|---|---|---|
For Spline Dia., mm | For No. of Splines | Overall Lg., mm | OD, mm | Dynamic Load Capacity, lbs. | Static Load Capacity, lbs. | Max. Dynamic Torque, in.-lbs. | Max. Static Torque, in.-lbs. | Max. Temp., °F | With Retaining Ring Grooves | Wd., mm | Dia., mm | Includes | Lg., mm | Wd., mm | Dp., mm | Each | |
6 | 4 | 25 | 14 | 270 | 510 | 13 | 21 | 176° | Yes | 0.6 | 13.4 | Machine Key | 10.5 | 2.5 | 1.2 | 00000000 | 0000000 |
13 | 4 | 36 | 24 | 600 | 1,050 | 185 | 346 | 176° | Yes | 1.3 | 22.7 | Machine Key | 15 | 3 | 1.5 | 00000000 | 000000 |
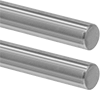
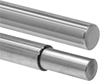

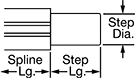
Step | |||||||||
---|---|---|---|---|---|---|---|---|---|
Dia., mm | No. of Splines | Lg., mm | Spline Lg., mm | Root Dia., mm | Dia., mm | Lg., mm | Material | Each | |
Splined on Both Ends | |||||||||
6 | 4 | 150 | 150 | 5.3 | __ | __ | 52100 Alloy Steel | 00000000 | 0000000 |
6 | 4 | 200 | 200 | 5.3 | __ | __ | 52100 Alloy Steel | 000000000 | 000000 |
6 | 4 | 300 | 300 | 5.3 | __ | __ | 52100 Alloy Steel | 000000000 | 000000 |
8 | 4 | 150 | 150 | 7.2 | __ | __ | 52100 Alloy Steel | 00000000 | 000000 |
8 | 4 | 200 | 200 | 7.2 | __ | __ | 52100 Alloy Steel | 000000000 | 000000 |
10 | 4 | 200 | 200 | 9 | __ | __ | 52100 Alloy Steel | 00000000 | 000000 |
10 | 4 | 300 | 300 | 9 | __ | __ | 52100 Alloy Steel | 000000000 | 000000 |
10 | 4 | 600 | 600 | 9 | __ | __ | 52100 Alloy Steel | 000000000 | 000000 |
13 | 4 | 200 | 200 | 11.7 | __ | __ | 52100 Alloy Steel | 000000000 | 00000 |
13 | 4 | 500 | 500 | 11.7 | __ | __ | 52100 Alloy Steel | 000000000 | 000000 |
13 | 4 | 700 | 700 | 11.7 | __ | __ | 52100 Alloy Steel | 000000000 | 000000 |
16 | 4 | 200 | 200 | 14.2 | __ | __ | 52100 Alloy Steel | 000000000 | 000000 |
16 | 4 | 700 | 700 | 14.2 | __ | __ | 52100 Alloy Steel | 000000000 | 000000 |
25 | 4 | 200 | 200 | 22.4 | __ | __ | 52100 Alloy Steel | 000000000 | 000000 |
25 | 4 | 500 | 500 | 22.4 | __ | __ | 52100 Alloy Steel | 000000000 | 000000 |
30 | 4 | 300 | 300 | 26.8 | __ | __ | 52100 Alloy Steel | 000000000 | 000000 |
30 | 4 | 1,000 | 1,000 | 26.8 | __ | __ | 52100 Alloy Steel | 000000000 | 000000 |
30 | 4 | 2,000 | 2,000 | 26.8 | __ | __ | 52100 Alloy Steel | 000000000 | 00000000 |
40 | 4 | 400 | 400 | 35.5 | __ | __ | 52100 Alloy Steel | 000000000 | 000000 |
40 | 4 | 700 | 700 | 35.5 | __ | __ | 52100 Alloy Steel | 000000000 | 000000 |
Splined End × Step-Down End | |||||||||
18.2 | 4 | 350 | 200 | 16.4 | 15 | 150 | 52100 Alloy Steel | 00000000 | 000000 |
28 | 4 | 450 | 300 | 24.8 | 25 | 150 | 52100 Alloy Steel | 00000000 | 000000 |
High-Load Mounted Linear Sleeve Bearings
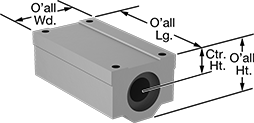
With two bearings mounted in one housing, these sleeve bearings can handle heavier loads than standard mounted linear sleeve bearings. All have an anodized aluminum housing that’s lightweight and stands up to corrosion. They also have a slippery, chemical-resistant PTFE liner, so there’s no need for added lubrication. Use these fixed-alignment bearings with round end-supported shafts where shaft misalignment is unlikely.
Overall, mm | Mounting Holes | ||||||||||||
---|---|---|---|---|---|---|---|---|---|---|---|---|---|
For Shaft Diameter, mm | Shaft Clearance, mm | Length | Width | Height | Center Height, mm | Dynamic Load Capacity | Static Load Capacity, lbs. | Temperature Range, °F | For Shaft Material | Number of | Diameter, mm | Each | |
Fixed Alignment | |||||||||||||
PTFE-Lined Ceramic-Coated 6061 Aluminum Bearings with Anodized 6063 Aluminum Housing | |||||||||||||
12 | 0.0127 | 77 | 44 | 30 | 15 | 300 lbs. @ 100 fpm | 4,450 | -400° to 385° | Aluminum, Stainless Steel, Steel | 4 | 5 | 0000000 | 000000 |
16 | 0.0127 | 89 | 50 | 38.5 | 19 | 400 lbs. @ 100 fpm | 6,650 | -400° to 385° | Aluminum, Stainless Steel, Steel | 4 | 5 | 0000000 | 00000 |
25 | 0.0127 | 136 | 76 | 51.5 | 26 | 1,000 lbs. @ 100 fpm | 16,850 | -400° to 385° | Aluminum, Stainless Steel, Steel | 4 | 8 | 0000000 | 000000 |
Mounted Linear Bearings for Ball Splines
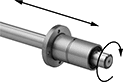
A flange with mounting holes makes it easy to attach a load to these bearings. Create a compact linear and rotary motion system for robots and other applications requiring complex, fast movements, by combining them with ball splines. These bearings move smoothly and precisely even at high speeds along ball splines while grooves on the ball spline transmit rotary power. Clip a retaining ring (not included) into the groove on these bearings to position them in your system.
Splines are alloy steel for high strength and wear resistance. They're hardened only on the outside, so they stand up to repeated motion while keeping their center soft enough to absorb stress from shifting loads. Those with a step-down end have a shoulder near the end to stop gears, sprockets, and bearings.
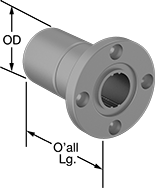
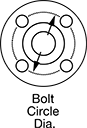

Groove | ||||||||||||||||
---|---|---|---|---|---|---|---|---|---|---|---|---|---|---|---|---|
For Spline Dia., mm | For No. of Splines | Overall Lg., mm | Flange OD, mm | Bolt Circle Dia., mm | OD, mm | Dynamic Load Capacity, lbs. | Static Load Capacity, lbs. | Max. Dynamic Torque, in.-lbs. | Max. Static Torque, in.-lbs. | Max. Temperature, ° F | With Retaining Ring Grooves | Wd., mm | Dia., mm | Number of Mounting Holes | Each | |
6 | 4 | 25 | 30 | 22 | 14 | 270 | 510 | 13 | 21 | 176° | Yes | 1.25 | 13.7 | 4 | 00000000 | 000000 |
8 | 4 | 25 | 32 | 24 | 16 | 325 | 645 | 18 | 32 | 176° | Yes | 1.25 | 15.6 | 4 | 00000000 | 00000 |
10 | 4 | 33 | 42 | 32 | 21 | 610 | 1,100 | 38 | 72 | 176° | Yes | 1.65 | 20.5 | 4 | 00000000 | 000000 |
13 | 4 | 36 | 43 | 33 | 24 | 600 | 1,050 | 185 | 346 | 176° | Yes | 1.3 | 22.7 | 4 | 000000000 | 00000 |
16 | 4 | 50 | 50 | 40 | 31 | 1,350 | 2,500 | 531 | 973 | 176° | Yes | 1.6 | 29.4 | 4 | 000000000 | 000000 |
18.2 | 4 | 60 | 51 | 40 | 32 | 1,750 | 2,500 | 734 | 1,177 | 176° | Yes | 3 | 31.3 | 4 | 00000000 | 000000 |
20 | 4 | 63 | 58 | 45 | 35 | 2,000 | 3,650 | 929 | 1,717 | 176° | Yes | 2 | 33 | 4 | 000000000 | 000000 |
23 | 4 | 70 | 60 | 47 | 37 | 2,750 | 3,600 | 1,433 | 2,115 | 176° | Yes | 3.5 | 36.1 | 4 | 00000000 | 000000 |
25 | 4 | 71 | 65 | 52 | 42 | 2,850 | 5,250 | 1,672 | 3,062 | 176° | Yes | 2.5 | 39.5 | 4 | 000000000 | 000000 |
28 | 4 | 80 | 70 | 54 | 45 | 4,150 | 5,200 | 2,557 | 3,646 | 176° | Yes | 4 | 43.9 | 4 | 00000000 | 000000 |
30 | 4 | 80 | 75 | 60 | 47 | 4,150 | 5,200 | 2,716 | 3,885 | 176° | Yes | 3 | 44 | 4 | 000000000 | 000000 |
37.4 | 4 | 100 | 90 | 72 | 60 | 6,900 | 8,400 | 5,637 | 7,806 | 176° | Yes | 5 | 58.6 | 4 | 00000000 | 000000 |
40 | 4 | 100 | 100 | 82 | 64 | 6,900 | 8,400 | 5,964 | 8,266 | 176° | Yes | 4 | 60 | 4 | 000000000 | 000000 |
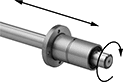
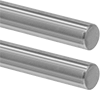
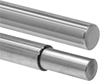

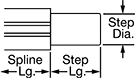
Step | |||||||||
---|---|---|---|---|---|---|---|---|---|
Dia., mm | No. of Splines | Lg., mm | Spline Lg., mm | Root Dia., mm | Dia., mm | Lg., mm | Material | Each | |
Splined on Both Ends | |||||||||
6 | 4 | 150 | 150 | 5.3 | __ | __ | 52100 Alloy Steel | 00000000 | 0000000 |
6 | 4 | 200 | 200 | 5.3 | __ | __ | 52100 Alloy Steel | 000000000 | 000000 |
6 | 4 | 300 | 300 | 5.3 | __ | __ | 52100 Alloy Steel | 000000000 | 000000 |
8 | 4 | 150 | 150 | 7.2 | __ | __ | 52100 Alloy Steel | 00000000 | 000000 |
8 | 4 | 200 | 200 | 7.2 | __ | __ | 52100 Alloy Steel | 000000000 | 000000 |
10 | 4 | 200 | 200 | 9 | __ | __ | 52100 Alloy Steel | 00000000 | 000000 |
10 | 4 | 300 | 300 | 9 | __ | __ | 52100 Alloy Steel | 000000000 | 000000 |
10 | 4 | 600 | 600 | 9 | __ | __ | 52100 Alloy Steel | 000000000 | 000000 |
13 | 4 | 200 | 200 | 11.7 | __ | __ | 52100 Alloy Steel | 000000000 | 00000 |
13 | 4 | 500 | 500 | 11.7 | __ | __ | 52100 Alloy Steel | 000000000 | 000000 |
13 | 4 | 700 | 700 | 11.7 | __ | __ | 52100 Alloy Steel | 000000000 | 000000 |
16 | 4 | 200 | 200 | 14.2 | __ | __ | 52100 Alloy Steel | 000000000 | 000000 |
16 | 4 | 700 | 700 | 14.2 | __ | __ | 52100 Alloy Steel | 000000000 | 000000 |
20 | 4 | 200 | 200 | 17.9 | __ | __ | 52100 Alloy Steel | 000000000 | 000000 |
20 | 4 | 2,000 | 2,000 | 17.9 | __ | __ | 52100 Alloy Steel | 000000000 | 000000 |
25 | 4 | 200 | 200 | 22.4 | __ | __ | 52100 Alloy Steel | 000000000 | 000000 |
25 | 4 | 500 | 500 | 22.4 | __ | __ | 52100 Alloy Steel | 000000000 | 000000 |
30 | 4 | 300 | 300 | 26.8 | __ | __ | 52100 Alloy Steel | 000000000 | 000000 |
30 | 4 | 1,000 | 1,000 | 26.8 | __ | __ | 52100 Alloy Steel | 000000000 | 000000 |
30 | 4 | 2,000 | 2,000 | 26.8 | __ | __ | 52100 Alloy Steel | 000000000 | 00000000 |
40 | 4 | 400 | 400 | 35.5 | __ | __ | 52100 Alloy Steel | 000000000 | 000000 |
40 | 4 | 700 | 700 | 35.5 | __ | __ | 52100 Alloy Steel | 000000000 | 000000 |
Splined End × Step-Down End | |||||||||
18.2 | 4 | 350 | 200 | 16.4 | 15 | 150 | 52100 Alloy Steel | 00000000 | 000000 |
23 | 4 | 350 | 200 | 20.6 | 20 | 150 | 52100 Alloy Steel | 00000000 | 000000 |
28 | 4 | 450 | 300 | 24.8 | 25 | 150 | 52100 Alloy Steel | 00000000 | 000000 |
37.4 | 4 | 550 | 400 | 33.1 | 30 | 150 | 52100 Alloy Steel | 00000000 | 000000 |
Threadless Lead Screw Nuts
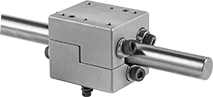

Install these nuts on a rotary shaft to create a linear positioning system without a lead screw. Instead of threads, a set of angled ball bearings drives the nut along a shaft as it spins. Nuts move towards you when the shaft rotates clockwise and away from you when the shaft rotates counterclockwise. To prevent overload damage, these nuts can be adjusted to slip and stop travelling at a given thrust load. Thrust loads are loads that are applied parallel to the shaft. Bearings are permanently lubricated to save maintenance time and effort.
Travel distance per turn is the distance the nut moves with one revolution of the shaft.
Overall | Mounting Hole | ||||||||||||
---|---|---|---|---|---|---|---|---|---|---|---|---|---|
For Shaft Dia. | Travel Distance per Turn | Max. Thrust Cap. Before Slip, lbs. | Lg. | Wd. | Ht. | Ctr. Ht. | Ctr.-to-Ctr. Lg. | Thread Size | No. of | Construction | Temperature Range, °F | Each | |
Aluminum | |||||||||||||
1/2" | 0.2" | 60 | 3 27/64" | 2" | 2 11/16" | 1 1/64" | 1 1/4" | 1/4"-20 | 2 | Two Piece | -10° to 180° | 0000000 | 0000000 |
1/2" | 0.5" | 60 | 3 27/64" | 2" | 2 11/16" | 1 1/64" | 1 1/4" | 1/4"-20 | 2 | Two Piece | -10° to 180° | 0000000 | 000000 |
3/4" | 0.75" | 60 | 3 27/64" | 2" | 2 11/16" | 1 1/64" | 1 1/4" | 1/4"-20 | 2 | Two Piece | -10° to 180° | 0000000 | 000000 |
Ball Screw/Splines and Bearings
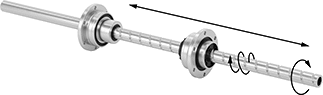
From one compact system, transmit linear or rotary motion or both at once (sometimes called spiral motion). Because of these different motions, these ball screw/splines and bearings create efficient, fluid movements in complex automated applications, such as pick-and-place robots.
The ball bearings move smoothly and precisely, even at high speeds. They're powered independently, so you can drive one bearing at a time or both together to coordinate movements.
The ball screw/splines are hardened on the surface, so they stand up to repeated motion. They’re also hollow, so you can run electrical wiring, compressed air tubing, coolants, or lubricant through their center.
Spline | Thread | Ball Screw Bearing | Ball Spline Bearing | |||||||||||||||
---|---|---|---|---|---|---|---|---|---|---|---|---|---|---|---|---|---|---|
Lg. | No. of | Lg. | Direction | ID, mm | Lg., mm | Root Dia., mm | OD, mm | Overall Lg., mm | Dynamic Load Cap., lbs. | Static Load Cap., lbs. | OD, mm | Overall Lg., mm | Dynamic Load Cap., lbs. | Static Load Cap., lbs. | Max. Dynamic Torque, in.-lbs. | Temp. Range, ° F | Each | |
Metric—1055 Carbon Steel | ||||||||||||||||||
8mm Dia. (Tolerance: -0.015mm to 0mm) | ||||||||||||||||||
200 mm | 4 | 180 mm | Right Hand | 3 | 200 | 7.44 | 19 | 28.5 | 240 | 400 | 16 | 25 | 330 | 580 | 17 | 5° to 176° | 0000000 | 000000000 |
10mm Dia. (Tolerance: -0.015mm to 0mm) | ||||||||||||||||||
300 mm | 4 | 270 mm | Right Hand | 4 | 300 | 9.27 | 23 | 34.5 | 380 | 600 | 21 | 33 | 600 | 1,100 | 34 | 5° to 176° | 0000000 | 00000000 |
16mm Dia. (Tolerance: -0.018mm to 0mm) | ||||||||||||||||||
500 mm | 6 | 360 mm | Right Hand | 11 | 500 | 15.15 | 32 | 40 | 870 | 1,610 | 31 | 50 | 1,590 | 2,830 | 277 | 5° to 176° | 0000000 | 00000000 |