Filter by
Display Type
Connection Location
Gender
Pipe Size
Measurement Unit
For Use With
Connection Material
Accuracy Scale
Thread Type
Measures
Fitting Connection
Connects To
System of Measurement
RoHS
Height
REACH
Mounting Position
Battery Size
Maximum Pressure
Case Color
Accuracy Grade
Minimum Environment Temperature
Minimum Process Temperature
Export Control Classification Number (ECCN)
DFARS Specialty Metals
About Pipe Size
More
About Pressure Gauges
More
Digital High-Accuracy Pressure Gauges
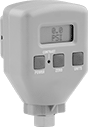
Polycarbonate
Plastic Case With
Bottom Connection
Plastic Case With
Bottom Connection
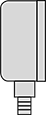
Bottom Connection
A four-digit LCD display allows for easy reading of measurements. The LCD shuts off automatically to extend battery life. Gauges are commonly used with pneumatic regulators, compressors, and in critical processes that require high accuracy, such as hydraulic and laboratory applications.
Polycarbonate Plastic Case with 17-4 PH Stainless Steel Connection—(psi, atm, bar, kg/cm2)
- For Use With: Air
- Accuracy: ±0.5% Full Scale (Not Graded)
Available Pressure Ranges | ||||
---|---|---|---|---|
psi | atm | bar | kg/cm2 | Resolution, psi |
0 to 100 | 0 to 6.8 | 0 to 6.8 | 0 to 7 | 0.1 |
0 to 1,000 | 0 to 68 | 0 to 68.9 | 0 to 70.3 | 1 |
Gauge with Bottom Connection | 9V Alkaline Disposable Battery | ||||||||||||||
---|---|---|---|---|---|---|---|---|---|---|---|---|---|---|---|
Ht. | Wd. | Dp. | Pipe Size | Environment Temp. Range, °F | Process Temp. Range, °F | Batteries Included | Battery Size | Number of Batteries Required | Mounting Orientation | Features | Each | Pkg. Qty. | Pkg. | ||
NPT Female | |||||||||||||||
4 1/16" | 2 11/16" | 1 7/8" | 1/8 | -40° to 150° | 35° to 130° | No | 9V | 1 | Any | 1-hr. Automatic Shut-Off | 00000000 | 0000000 | 1 | 00000000 | 00000 |