About Structural Adhesives
More
About Paint and Protective Coatings
More
Heat Sink Bonding Compounds
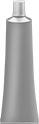
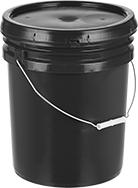

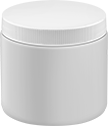
Bond heat sinks to surfaces, eliminating air gaps for maximum heat transfer. These compounds are commonly used with transistors, diodes, rectifiers, and transformers. Product regulations restrict sales to the listed jurisdictions/areas.
Zinc-oxide compounds create a more secure bond than silicone compounds.
Container | ||||||||||
---|---|---|---|---|---|---|---|---|---|---|
Thermal Conductivity | Temp. Range, °F | Type | Size, fl. oz. | Net Weight, lbs. | Manufacturer | Manufacturer Model Number | Specifications Met | Cannot Be Sold To | Each | |
Silicone | ||||||||||
0.68 W/m-K @ 97° F | -40° to 390° | Tube | 5 | __ | Dow Corning | 340 | __ | __ | 00000000 | 000000 |
0.75 W/m-K @ 97° F | -40° to 400° | Tube | 8 | __ | __ | __ | __ | __ | 00000000 | 00000 |
0.75 W/m-K @ 97° F | -40° to 400° | Pail | __ | 80 | __ | __ | __ | __ | 000000000 | 00000000 |
Zinc Oxide | ||||||||||
0.92 W/m-K @ 97° F | -40° to 320° | Tube | 2 | __ | __ | __ | MIL-C-47113 | __ | 0000000 | 00000 |
0.92 W/m-K @ 97° F | -40° to 320° | Syringe | 1 | __ | __ | __ | MIL-C-47113 | __ | 00000000 | 00000 |
0.92 W/m-K @ 97° F | -40° to 390° | Tube | 4 | __ | __ | __ | ASTM D5470 | Outside United States and Canada | 00000000 | 00000 |
0.92 W/m-K @ 97° F | -40° to 390° | Jar | 16 | __ | __ | __ | ASTM D5470 | Outside United States and Canada | 00000000 | 00000 |
5 W/m-K @ 97° F | -40° to 500° | Tube | 2 | __ | __ | __ | __ | __ | 00000000 | 00000 |
5 W/m-K @ 97° F | -40° to 500° | Tube | 4 | __ | __ | __ | __ | __ | 00000000 | 00000 |
5 W/m-K @ 97° F | -40° to 500° | Jar | 16 | __ | __ | __ | __ | __ | 00000000 | 00000 |
5 W/m-K @ 97° F | -40° to 500° | Syringe | 1 | __ | __ | __ | __ | __ | 00000000 | 00000 |
Heat-Transfer Compounds
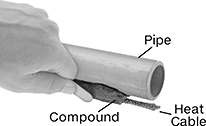
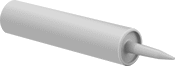
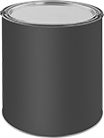
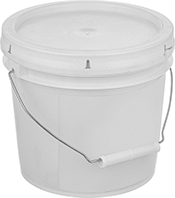
Eliminate air gaps that cause heat loss and premature heater failure. These compounds mold around heat cable so it makes direct contact with pipes, pumps, and other parts.
Compounds with a 450° F maximum temperature don’t harden, so they maintain a tight seal even as the surface you’re heating expands and contracts. Since they’re waterproof, they also shield the surface from corrosion.
Compounds with a 750° F maximum temperature are often used with steam, hot oil, and glycol heat trace lines.
Compounds with a 1250° F or 2200° F maximum temperature are often used with steam heat trace lines, strip heaters, and ring heaters.
Container | |||||||
---|---|---|---|---|---|---|---|
Size | Type | Begins to Harden, hrs. | Reaches Full Strength, hrs. | For Surface Material | For Use Outdoors | Each | |
450° F Max. Temp. | |||||||
114 W/m^2 × °C | |||||||
10 fl. oz. | Cartridge | __ | __ | Ceramic, Glass, Metal, Plastic | Yes | 0000000 | 000000 |
32 fl. oz. | Cartridge | __ | __ | Ceramic, Glass, Metal, Plastic | Yes | 0000000 | 00000 |
1 qt. | Can | __ | __ | Ceramic, Glass, Metal, Plastic | Yes | 0000000 | 00000 |
1 gal. | Can | __ | __ | Ceramic, Glass, Metal, Plastic | Yes | 0000000 | 00000 |
5 gal. | Can | __ | __ | Ceramic, Glass, Metal, Plastic | Yes | 0000000 | 000000 |
750° F Max. Temp. | |||||||
114 W/m^2 × °C | |||||||
10 fl. oz. | Cartridge | 1 | 24 | Ceramic, Glass, Metal, Plastic | No | 0000000 | 00000 |
32 fl. oz. | Cartridge | 1 | 24 | Ceramic, Glass, Metal, Plastic | No | 0000000 | 00000 |
1 qt. | Can | 1 | 24 | Ceramic, Glass, Metal, Plastic | No | 0000000 | 00000 |
151 W/m^2 × °C | |||||||
1 gal. | Can | 6 | 24 | Ceramic, Glass, Metal | No | 000000 | 00000 |
5 gal. | Can | 6 | 24 | Ceramic, Glass, Metal | No | 000000 | 000000 |
1,250° F Max. Temp. | |||||||
114 W/m^2 × °C | |||||||
10 fl. oz. | Cartridge | 1 | 24 | Ceramic, Glass, Metal, Plastic | No | 0000000 | 00000 |
32 fl. oz. | Cartridge | 1 | 24 | Ceramic, Glass, Metal, Plastic | No | 0000000 | 00000 |
1 qt. | Can | 1 | 24 | Ceramic, Glass, Metal, Plastic | No | 0000000 | 00000 |
1 gal. | Can | 1 | 24 | Ceramic, Glass, Metal, Plastic | No | 0000000 | 000000 |
5 gal. | Can | 1 | 24 | Ceramic, Glass, Metal, Plastic | No | 0000000 | 000000 |
2,200° F Max. Temp. | |||||||
85 W/m^2 × °C | |||||||
1 gal. | Pail | 1 | 24 | Metal | Yes | 0000000 | 000000 |
Heat-Transfer Epoxy Potting Compounds
Formulated to draw heat away from sensitive electronic components, these potting compounds have higher thermal conductivity than standard potting compounds. Use them to encase electronic assemblies for protection from dust, chemicals, moisture, mechanical shock, and vibration. Rigid and wear resistant, epoxies are the strongest of the potting compounds. They have excellent chemical and moisture resistance, withstand a wide range of temperatures, and provide excellent electrical insulation.
Cartridge potting compound requires a gun and mixer nozzle (each sold separately) to dispense.
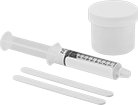
Dry Time | |||||||||||
---|---|---|---|---|---|---|---|---|---|---|---|
Container Size, fl. oz. | Consistency | Touch | Overall, hrs. | Dielectric Strength, V/mil | Thermal Conductivity, W/m-K | Max. Temp., °F | Heating Requirements to Reach Full Strength | For Use On | Color | Each | |
0.9 | Thick Liquid | 25 min. | 24 | 450 | 1.87 | 500° | 1 hr. @ 250° F then 1 hr. @ 350° F | Aluminum, Brass, Bronze, Copper, Steel, Stainless Steel, Cast Iron, Iron, Silver, Titanium, Plastic, Composites, Ceramic, Glass | Black | 0000000 | 000000 |
1 | Gel | 4 hrs. | 6 | Not Rated | 1.87 | 600° | 4 hrs. @ 250° F then 2 hrs. @ 350° F | Aluminum, Brass, Bronze, Copper, Steel, Stainless Steel, Cast Iron, Iron, Silver, Titanium, Plastic, Composites, Ceramic, Glass | Black | 0000000 | 00000 |
1.5 | Thin Liquid | 30 min. | 26 | 450 | 0.21 | 500° | 1 hr. @ 250° F then 1 hr. @ 350° F | Aluminum, Brass, Bronze, Copper, Steel, Stainless Steel, Cast Iron, Iron, Silver, Titanium, Plastic, Composites, Ceramic, Glass | Amber | 0000000 | 00000 |
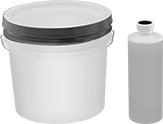
Dry Time | ||||||||||
---|---|---|---|---|---|---|---|---|---|---|
Container Size, gal. | Consistency | Touch, min. | Overall, hrs. | Dielectric Strength, V/mil | Thermal Conductivity, W/m-K | Max. Temp., °F | For Use On | Color | Each | |
1 | Thick Liquid | 25 | 24 | 450 | 1.87 | 500° | Steel, Ceramic, Glass | Black | 0000000 | 0000000 |
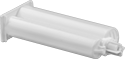
Dry Time | ||||||||||
---|---|---|---|---|---|---|---|---|---|---|
Container Size, fl. oz. | Consistency | Touch, min. | Overall, hrs. | Dielectric Strength, V/mil | Thermal Conductivity, W/m-K | Temp. Range, °F | For Use On | Color | Each | |
1.7 | Thick Liquid | 15 | 8 | 520 | 1.01 | -40° to 210° | Aluminum, Brass, Bronze, Copper, Steel, Stainless Steel, Silver, Titanium, Plastic, Composites, Fiberglass | Black | 0000000 | 000000 |
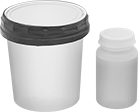
Dry Time | |||||||||||
---|---|---|---|---|---|---|---|---|---|---|---|
Container Size, fl. oz. | Consistency | Touch | Overall, hrs. | Dielectric Strength, V/mil | Thermal Conductivity, W/m-K | Max. Temp., °F | Heating Requirements to Reach Full Strength | For Use On | Color | Each | |
16 | Thin Liquid | 30 min. | 26 | 450 | 0.21 | 500° | 1 hr. @ 250° F then 1 hr. @ 350° F | Aluminum, Brass, Bronze, Copper, Steel, Stainless Steel, Cast Iron, Iron, Silver, Titanium, Plastic, Composites, Ceramic, Glass | Amber | 0000000 | 0000000 |
19 | Thick Liquid | 25 min. | 24 | 450 | 1.87 | 500° | __ | Steel, Ceramic, Glass | Black | 0000000 | 000000 |
20 | Gel | 4 hrs. | 6 | Not Rated | 1.87 | 600° | 4 hrs. @ 250° F then 2 hrs. @ 350° F | Steel, Ceramic, Glass | Black | 0000000 | 000000 |
Adjustable-Flexibility Heat-Transfer Epoxy Potting Compounds
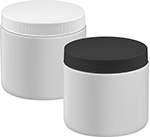
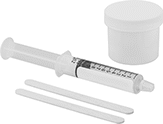
Mixing required—resin and hardener come in two separate jars or in a jar and syringe and must be combined before applying. Change the mix ratio of these heat-transfer potting compounds to achieve the right hardness for your application. They're formulated to draw heat away from sensitive electronic components, so they have higher thermal conductivity than standard potting compounds. Use them to encase electronic assemblies for protection from dust, chemicals, moisture, mechanical shock, and vibration. Rigid and wear resistant, epoxies are the strongest of the potting compounds. They have excellent chemical and moisture resistance, withstand a wide range of temperatures, and provide excellent electrical insulation.
The size listed is the combined total of the two parts.
Dry Time | ||||||||||||
---|---|---|---|---|---|---|---|---|---|---|---|---|
Container Size, fl. oz. | Consistency | Touch, min. | Overall, hrs. | Hardness Rating | Dielectric Strength, V/mil | Thermal Conductivity, W/m-K | Temp. Range, °F | Heating Requirements to Reach Full Strength | For Use On | Color | Each | |
Jar Compounds | ||||||||||||
12 | Thick Liquid | 30 | 24 | Extra Hard, Medium Hard, Medium Soft, Soft | 450 | 1 | -100° to 450° | __ | Aluminum, Brass, Bronze, Copper, Steel, Stainless Steel, Plastic, Ceramic, Glass | Tan | 000000 | 0000000 |
24 | Thick Liquid | 30 | 24 | Extra Hard, Medium Hard, Medium Soft, Soft | 450 | 1 | -100° to 450° | __ | Aluminum, Brass, Bronze, Copper, Steel, Stainless Steel, Plastic, Ceramic, Glass | Tan | 000000 | 000000 |
Jar and Syringe Compounds | ||||||||||||
1.6 | Thick Liquid | 30 | 26 | Extra Hard, Medium Hard, Medium Soft, Soft | 450 | 1.01 | -100° to 450° | 2 hrs. @ 250° F | Aluminum, Brass, Bronze, Copper, Steel, Stainless Steel, Plastic, Ceramic, Glass | Tan | 000000 | 00000 |
Low-Outgassing Heat-Transfer Epoxy Potting Compounds
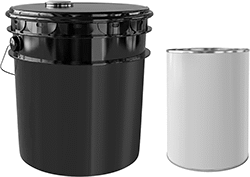
Tested to meet ASTM E595, a standard used by NASA, these potting compounds release almost no volatile emissions that could damage sensitive electronics, even in a vacuum. Use them to draw heat away from your components—they conduct heat better than standard potting compounds. Made of epoxy, they’re the strongest of the potting compounds, so they’re rigid and wear resistant. They’ll also resist breaking down from chemicals and moisture. These compounds are excellent at insulating current, and they’ll shield against dust, vibration, and shock.
To apply, mix the two parts together and pour them over components inside a container, such as a potting box.
Dry Time | ||||||||||||
---|---|---|---|---|---|---|---|---|---|---|---|---|
Container Size, fl. oz. | Consistency | Touch | Overall | Dielectric Strength, V/mil | Thermal Conductivity, W/m-K | Temp. Range, °F | Heating Requirements to Reach Full Strength | Specifications Met | For Use On | Color | Each | |
Pail and Can Compounds—Extra Hard | ||||||||||||
32 | Thick Liquid | 45 min. | 24 hrs. | 365 | 1.25 | -40° to 265° | __ | ASTM E595 | Aluminum, Brass, Bronze, Copper, Steel, Stainless Steel, Plastic | Black | 0000000 | 0000000 |
32 | Thick Liquid | 4 hrs. | 12 hrs. | 450 | 0.55 | -65° to 310° | 12 hrs. @ 175° F | ASTM E595 | Aluminum, Brass, Bronze, Copper, Steel, Stainless Steel, Plastic | Black | 0000000 | 000000 |
High-Temperature Epoxy Potting Compounds
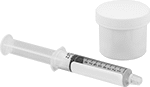
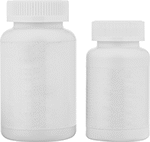
Protect circuit boards and other electronics where high heat is a concern but you don’t need to transfer that heat elsewhere. These compounds are a good middle ground between standard epoxy compounds and heat-transfer compounds. They work at temperatures twice as high as standard epoxy compounds. However, they don't conduct heat as well as heat-transfer compounds so they're not the best choice for circuit boards that run for long periods of time. Harden these compounds at room temperature—they don’t require an oven to harden like heat-transfer compounds do.
Since they’re an epoxy compound, they won’t break down from chemicals or moisture. They’re also excellent electrical insulators and withstand a wide range of temperatures. Use them to shield components from dust, moisture, chemicals, mechanical shock, and vibration.
Jar and syringe compounds are the consistency of honey once they’re mixed, so they’ll seep into the crevices of a circuit board and encapsulate intricate components. Use the syringe for precise application.
Bottle compounds are easier to apply in higher volumes than jar and syringe compounds. Mix them together and pour them over components inside containers, such as a potting box. If air bubbles occur after mixing, you can put the mixture in a vacuum chamber to remove them. They cannot be sold to Canada due to product labeling requirements.
Dry Time | |||||||||||
---|---|---|---|---|---|---|---|---|---|---|---|
Container Size, fl. oz. | Consistency | Viscosity, cP | Touch | Overall, hrs. | Dielectric Strength, V/mil | Thermal Conductivity, W/m-K | Max. Temp., °F | For Use On | Cannot Be Sold To | Each | |
Jar and Syringe Compounds—Extra Hard | |||||||||||
1 | Thick Liquid | 3,600 | 12 hrs. | 24 | 450 | 0.22 | 500° | Aluminum, Brass, Bronze, Copper, Steel, Stainless Steel, Plastic, Rubber, Composites, Fiberglass, Ceramic, Glass | __ | 0000000 | 000000 |
Bottle Compounds—Extra Hard | |||||||||||
12.6 | Paste | 22,000 | 60 min. | 24 | 470 | 0.3 | 435° | Aluminum, Brass, Bronze, Copper, Steel, Stainless Steel, Plastic, Rubber, Composites, Fiberglass, Ceramic, Glass | Canada | 0000000 | 00000 |
Conductive Adhesives for Electronics
An alternative to solder, these flexible, silver-filled adhesives accommodate joint movement. Use them to bond electrical components and repair circuits.
Epoxy adhesives are two-part adhesives that need to be mixed together. The size listed is the combined total of the two parts.
Thermoplastic adhesives are one-part adhesives that don’t need to be mixed. Dry to the touch and faster and easier to apply than two-part adhesives, they’re best for use on automated assembly lines. Often used to join solar cells in solar panels, these adhesives make instant electrical connections without flux at lower temperatures than soldering. Since they attach to solar cells with heat and slight pressure, they limit stress cracks that can form when soldering. These adhesives can also be used as a bridge between multiple solar panels.
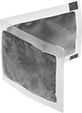
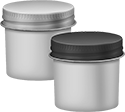
Container | |||||||||||
---|---|---|---|---|---|---|---|---|---|---|---|
Size, fl. oz. | Net Weight, oz. | Begins to Harden | Reaches Full Strength | Thermal Conductivity, W/m-K | Surface Resistivity, ohms-cm | Mix Ratio | Consistency | Temp. Range, °F | For Joining | Each | |
One-Time-Use Packet | |||||||||||
__ | 0.09 | 3 hrs. | 24 hrs. | 1.55 | 0.05 | 1:1.15 | Paste | -75° to 230° | Ceramic, Glass, Metal | 0000000 | 000000 |
Can | |||||||||||
0.5 | __ | 4 hrs. | 5 days | 7.93 | 0.0004 | 1:1 | Paste | 80° to 265° | Metal | 0000000 | 000000 |
1 | __ | 4 hrs. | 5 days | 7.93 | 0.0004 | 1:1 | Paste | 80° to 265° | Metal | 0000000 | 000000 |
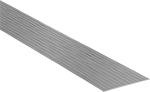
Lg. | Wd. | Thick. | Melting Temp., °F | Max. Temp., °F | Begins to Harden | Reaches Full Strength | Thermal Conductivity, W/m-K | Surface Resistivity, ohms-cm | Consistency | For Joining | Each | |
Strip with Adhesive on One Side | ||||||||||||
---|---|---|---|---|---|---|---|---|---|---|---|---|
12" | 1/16" | 0.002" | 250° | 300° | 5 sec. | 5 sec. | 12 | 0.0001 | Film | Metal | 00000000 | 00000 |
Ceramic Adhesives
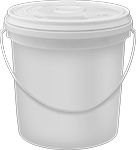
Often used for bonding and repair on exhaust systems, diesel engines, and gas turbines, these adhesives withstand high temperatures and provide excellent electrical insulation. Pastes will not drip or sag while hardening on a vertical surface, while thick liquids flow into small spaces and are easy to spread.
Container | ||||||||||||
---|---|---|---|---|---|---|---|---|---|---|---|---|
Size, fl. oz. | Type | Begins to Harden | Reaches Full Strength | Thermal Conductivity, W/m-K | Mix Ratio | Consistency | Viscosity, cP | Max. Temp., °F | Color | For Joining | Each | |
8 | Pail | 20 min. | 48 hrs. | 0.865 | __ | Thick Liquid | 90,000 | 2300° | Gray | Ceramic, Metal | 0000000 | 000000 |
8 | Pail | 20 min. | 48 hrs. | 0.865 | __ | Paste | 130,000 | 2300° | Gray | Ceramic, Metal | 0000000 | 00000 |
8 | Pail | 20 min. | 48 hrs. | 0.865 | __ | Paste | 190,000 | 2300° | Gray | Ceramic, Metal | 0000000 | 00000 |
16 | Pail | 10 min. | 16 hrs. | 1.2 | 2:1 | Thick Liquid | 12,000 | 1800° | Beige | Ceramic, Glass | 0000000 | 00000 |
16 | Pail | 15 min. | 24 hrs. | 1.44 | __ | Thick Liquid | 22,500 | 4000° | Beige | Ceramic, Masonry | 0000000 | 000000 |
20 | Pail | 10 min. | 24 hrs. | 0.721 | 2.3:1 | Thick Liquid | 20,000 | 2500° | White | Ceramic, Glass | 0000000 | 00000 |
23 | Pail | 10 min. | 16 hrs. | 1.15 | 4:1 | Thick Liquid | 20,000 | 2000° | Beige | Ceramic, Glass | 0000000 | 00000 |
24 | Pail | 20 min. | 2 hrs. | 5.77 | 2.4:1 | Thick Liquid | 6,000 | 3000° | White | Ceramic, Metal | 0000000 | 000000 |
32 | Pail | 15 min. | 24 hrs. | 1.44 | __ | Thick Liquid | 22,500 | 4000° | Beige | Ceramic, Masonry | 0000000 | 000000 |
32 | Pail | 20 min. | 24 hrs. | 0.288 | __ | Thick Liquid | 35,000 | 2300° | White | Ceramic | 0000000 | 000000 |
64 | Pail | 20 min. | 48 hrs. | 0.865 | __ | Paste | 130,000 | 2300° | Gray | Ceramic, Metal | 0000000 | 000000 |
64 | Pail | 20 min. | 48 hrs. | 0.865 | __ | Paste | 190,000 | 2300° | Gray | Ceramic, Metal | 0000000 | 000000 |
Conductive Surface Fillers for Electronics
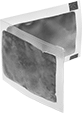

A high silver content allows these surface fillers to conduct electricity and heat. Use them to fill gaps and rebuild missing material on electrical connections or to assemble new components. They come as two parts. The size listed is the combined total of the two parts.
Volume resistivity measures how well a material opposes the flow of electricity. The lower the rating, the more electricity it conducts.
Thermal conductivity measures a material’s ability to transfer heat. The higher the rating, the more heat it transfers.
Container | Temp. Range, °F | ||||||||||||
---|---|---|---|---|---|---|---|---|---|---|---|---|---|
Mfr. Model No. | Size, fl. oz. | Net Weight, oz. | Type | Begins to Harden | Reaches Full Strength | Thermal Conductivity, W/m-K | Volume Resistivity, ohms-cm | Mix Ratio | Min. | Max. | For Use On | Each | |
Loctite® Surface Fillers | |||||||||||||
3888 | __ | 0.09 | One-Time-Use Packet | 90 min. | 24 hrs. | 1.44 | 0.001 | 100:6 | -40° | 170° | Aluminum, Brass, Bronze, Copper, Steel, Stainless Steel, Titanium, Polycarbonate Plastic | 0000000 | 000000 |
Surface Fillers | |||||||||||||
__ | __ | 0.09 | One-Time-Use Packet | 90 min. | 24 hrs. | 6.05 | 0.009 | 100:6 | -75° | 250° | Aluminum, Brass, Bronze, Copper, Steel, Stainless Steel, Titanium, Ceramic, Glass | 0000000 | 00000 |
__ | __ | 0.35 | One-Time-Use Packet | 90 min. | 24 hrs. | 6.05 | 0.009 | 100:6 | -75° | 250° | Aluminum, Brass, Bronze, Copper, Steel, Stainless Steel, Titanium, Ceramic, Glass | 0000000 | 000000 |
__ | 0.5 | __ | Jar | 4 hrs. | 5 days | 5.77 | 0.0004 | 1:1 | Not Rated | 300° | Aluminum, Brass, Copper, Steel, Stainless Steel | 0000000 | 000000 |
__ | 1 | __ | Jar | 4 hrs. | 5 days | 5.77 | 0.0004 | 1:1 | Not Rated | 300° | Aluminum, Brass, Copper, Steel, Stainless Steel | 0000000 | 000000 |
Conductive Surface Filler Pens for Electronics
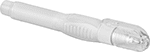
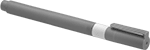
Dispense ready-to-use conductive liquid to fill pits and small gaps on circuit board components. These pens are also used to sketch and repair conductive pathways.
Product labeling requirements restrict sales to the listed areas.
Carbon acrylic pens should be used where only a small amount of conductivity is needed, such as circuit boards in keyboards. Their high surface resistivity only allows a small current to pass.
Nickel acrylic pens are best for general purpose repairs, such as bridges and traces in printed circuit boards. They have a medium surface resistivity, so they're a good balance between carbon acrylic and silver epoxy pens.
Silver epoxy pens are the most versatile—use them for any type of repair as well as for repairs that require excellent conductivity, such as connecting through holes on circuit boards without adding jumpers, wiring, or solder. Since they have the lowest surface resistivity, they allow the most current to pass.
Tip | ||||||||||||||
---|---|---|---|---|---|---|---|---|---|---|---|---|---|---|
Container Size, fl. oz. | Dia. | Shape | Begins to Harden, min. | Reaches Full Strength | Surface Resistivity, ohms/sq. | Consistency | Max. Thick. | For Use Outdoors | Temp. Range, °F | Color | For Use On | Cannot Be Sold To | Each | |
Carbon Acrylic | ||||||||||||||
0.2 | 0.06" | Point | 2 | 24 hrs. | 100 | Thin Liquid | 0.003" | Yes | -40° to 245° | Black | Plastic | Canada | 0000000 | 000000 |
Nickel Acrylic | ||||||||||||||
0.2 | 0.06" | Point | 2 | 24 hrs. | 0.49 | Thin Liquid | 0.004" | Yes | -40° to 245° | Gray | Plastic | Canada | 0000000 | 00000 |
Silver Epoxy | ||||||||||||||
0.2 | 0.03" | Point | 3 | 60 min. | 0.050 | Thin Liquid | Not Rated | No | -65° to 300° | Silver | Aluminum, Brass, Bronze, Copper, Steel, Stainless Steel, Titanium | Outside United States and Canada | 0000000 | 00000 |