About Composites
More
About Shafts
More
Rotary Shafts
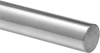
Combine these general purpose drive shafts with gears, sprockets, and bearings to transmit rotary motion. All are turned, precision ground, and polished to meet tight diameter and straightness tolerances. This means these shafts evenly distribute loads, reduce vibration, and improve accuracy and stability.
Steel shafts are generally stronger than stainless steel shafts but not as corrosion resistant. Carbon steel shafts balance high strength and good machinability, making them ideal for general purpose use. 12L14 carbon steel shafts have a lead additive that makes them easier to machine than any other rotary shaft but also more prone to wear.
Stainless steel shafts are more corrosion resistant than steel shafts but more difficult to machine. 316 stainless steel shafts are the most corrosion resistant stainless steel shaft.
Shafts with chamfered edges reduce damage to bearings, housings, and other components during installation.
Lg. | Lg. Tolerance | Straightness Tolerance | Edge Type | Hardness Rating | Hardness | Each | |
Metric—12L14 Carbon Steel | |||||||
---|---|---|---|---|---|---|---|
3mm Dia. (Tolerance: -0.005mm to 0mm) | |||||||
50mm | -0.25mm to 0.25mm | 0.12 mm per 300 mm | Chamfered | Medium | Rockwell B83 | 00000000 | 00000 |
100mm | -0.25mm to 0.25mm | 0.12 mm per 300 mm | Chamfered | Medium | Rockwell B83 | 00000000 | 0000 |
200mm | -0.25mm to 0.25mm | 0.12 mm per 300 mm | Chamfered | Medium | Rockwell B83 | 00000000 | 0000 |
400mm | -0.25mm to 0.25mm | 0.12 mm per 300 mm | Chamfered | Medium | Rockwell B83 | 00000000 | 00000 |
Metric—316 Stainless Steel | |||||||
3mm Dia. (Tolerance: -0.005mm to 0mm) | |||||||
200mm | -0.25mm to 0.25mm | 3.00 mm per 300 mm | Chamfered | Medium | Rockwell B83 | 0000000 | 00000 |
400mm | -0.25mm to 0.25mm | 3.00 mm per 300 mm | Chamfered | Medium | Rockwell B83 | 0000000 | 00000 |
600mm | -0.25mm to 0.25mm | 3.00 mm per 300 mm | Chamfered | Medium | Rockwell B83 | 0000000 | 00000 |
800mm | -0.25mm to 0.25mm | 3.00 mm per 300 mm | Chamfered | Medium | Rockwell B83 | 0000000 | 00000 |
Linear Motion Shafts
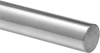
Smooth, hard, and wear resistant, these shafts work with linear bearings to reduce friction in manual and automated systems, such as those found in packing, machine tool, and material handling operations. All are turned, ground, and polished to tight diameter and straightness tolerances.
Steel shafts are generally stronger than aluminum and stainless steel shafts but not as corrosion resistant. Alloy steel shafts are stronger and more wear resistant than carbon steel.
Stainless steel shafts are more corrosion resistant than steel shafts; however, they’re not as hard as steel shafts and can be more difficult to machine. 17-4 PH stainless steel shafts are more corrosion resistant than 400 series stainless steel shafts, but they’re not as hard or as wear resistant.
Surface smoothness—The lower the microinch value, the smoother the finish and the less friction and wear it will cause on the bearing.
Lg., mm | Lg. Tolerance, mm | Straightness Tolerance | Surface Smoothness, microinch | Edge Type | Hardness Rating | Hardness | Heat Treatment | Each | |
3 mm Dia. (Tolerance: -0.012 mm to -0.004 mm) | |||||||||
---|---|---|---|---|---|---|---|---|---|
25 | -0.5 to 0.5 | 0.050 mm per 300 mm | 16 | Chamfered | Very Hard | Rockwell C60 | Case Hardened | 0000000 | 000000 |
50 | -0.5 to 0.5 | 0.050 mm per 300 mm | 16 | Chamfered | Very Hard | Rockwell C60 | Case Hardened | 00000000 | 00000 |
75 | -0.5 to 0.5 | 0.050 mm per 300 mm | 16 | Chamfered | Very Hard | Rockwell C60 | Case Hardened | 00000000 | 00000 |
100 | -0.5 to 0.5 | 0.050 mm per 300 mm | 16 | Chamfered | Very Hard | Rockwell C60 | Case Hardened | 00000000 | 00000 |
3 mm Dia. (Tolerance: -0.008 mm to -0.002 mm) | |||||||||
200 | -0.8 to 0.8 | 0.050 mm per 300 mm | 16 | Chamfered | Very Hard | Rockwell C59 | Case Hardened | 0000000 | 00000 |
400 | -0.8 to 0.8 | 0.050 mm per 300 mm | 16 | Chamfered | Very Hard | Rockwell C59 | Case Hardened | 0000000 | 00000 |
Lg., mm | Lg. Tolerance, mm | Straightness Tolerance | Surface Smoothness, microinch | Edge Type | Hardness Rating | Hardness | Heat Treatment | Each | |
3 mm Dia. (Tolerance: -0.005 mm to 0 mm) | |||||||||
---|---|---|---|---|---|---|---|---|---|
100 | -0.25 to 0.25 | 0.12 mm per 300 mm | 10 | Chamfered | Hard | Rockwell C40 | Hardened | 0000000 | 000000 |
300 | -0.25 to 0.25 | 0.12 mm per 300 mm | 10 | Chamfered | Hard | Rockwell C40 | Hardened | 0000000 | 00000 |
600 | -0.25 to 0.25 | 0.12 mm per 300 mm | 10 | Chamfered | Hard | Rockwell C40 | Hardened | 0000000 | 00000 |
900 | -0.25 to 0.25 | 0.12 mm per 300 mm | 10 | Chamfered | Hard | Rockwell C40 | Hardened | 0000000 | 00000 |
Low-Carbon Steel Rods and Discs

- Yield Strength: See table
- Hardness: See table
- Heat Treatable: Yes
- Max. Hardness After Heat Treatment: See table
- Fabrication: See table
- Specifications Met: See table
Also known as mild steel, low-carbon steel is easy to machine, form, and weld. It's widely fabricated into low-strength fasteners, pins, and axles. You can surface harden this material for added wear resistance. All have been manufactured to meet ASTM standards for quality and performance.
Cold-worked rods and discs have a finished look and quality. The cold-working process gives the steel consistent strength, hardness, and dimensions throughout.
Certificates with a traceable lot number are available for these products. Download certificates from ORDER HISTORY after your order ships.
Dia., mm | Dia. Tolerance, mm | Yield Strength, psi | Fabrication | Hardness | Max. Hardness After Heat Treatment | Specifications Met | Pkg. Qty. | Pkg. | |
75 mm Lg. | |||||||||
---|---|---|---|---|---|---|---|---|---|
3 | -0.05 to 0 | 54,000 | Cold Worked | Rockwell B70 (Medium) | Rockwell C60 | ASTM A108 | 10 | 00000000 | 000000 |
Tight-Tolerance Low-Carbon Steel Rods
- Yield Strength: Not Rated
- Hardness: Not Rated
- Heat Treatable: Yes
- Max. Hardness After Heat Treatment: See table
- Fabrication: Cold Drawn
- Specifications Met: ASTM A108
These rods are precision ground and held to a strict straightness tolerance, so they're ready for turning in a lathe. Also known as mild steel, low-carbon steel is easy to machine, form, and weld. It's widely fabricated into low-strength fasteners, pins, and axles. For added wear resistance, this material can be surface hardened with heat treating. All have been manufactured to meet ASTM A108 standards for quality and performance.
Certificates with a traceable lot number are available for these products. Download certificates from ORDER HISTORY after your order ships.
Tight-Tolerance Ultra-Machinable 12L14 Carbon Steel Rods
- Yield Strength: 65,000 psi
- Hardness: Rockwell B80 (Medium)
- Heat Treatable: Yes
- Max. Hardness After Heat Treatment: Rockwell C65
- Fabrication: Cold Worked
- Specifications Met: ASTM A108
Ready for turning in a lathe, these rods are precision ground and held to a strict straightness tolerance. The lead additive acts as a lubricant, which allows 12L14 carbon steel to withstand very fast machining. It's used to fabricate a wide variety of machine parts, such as shaft couplings, studs, and pins. These rods meet ASTM A108 quality and performance standards. For added wear resistance, they can be surface hardened with heat treating.
Certificates with a traceable lot number are available for these products. Download certificates from ORDER HISTORY after your order ships.
Tight-Tolerance Multipurpose 4140 Alloy Steel Rods
- Yield Strength: 60,000 psi
- Hardness: Rockwell B90 (Medium)
- Heat Treatable: Yes
- Max. Hardness After Heat Treatment: Rockwell C60
- Fabrication: Cold Drawn
- Specifications Met: ASTM A108
Ready for turning in your lathe, these rods are precision ground and held to a strict straightness tolerance. Also known as chrome-moly steel, this versatile alloy steel is used for a wide range of parts, such as gears, axles, shafts, collets, and die holders. It resists fracturing from repeated stress. For added wear resistance, you can surface harden these rods with heat treating. They are manufactured to ASTM A108 standards for performance and quality.
Note: Rods may be made from either 4140 or 4142 alloy steel. They are interchangeable in most applications.
Certificates with a traceable lot number are available for these products. Download certificates from ORDER HISTORY after your order ships.
Multipurpose 4140 Alloy Steel Rods and Discs

Also known as chrome-moly steel, this versatile alloy steel is used for a wide range of parts, such as gears, axles, shafts, collets, and die holders. It resists fracturing from repeated stress. For added wear resistance, the surface can be hardened with heat treating. These rods and discs have been manufactured to meet ASTM standards for quality and performance.
Note: Rods and discs may be made from either 4140 or 4142 alloy steel. They are interchangeable in most applications.
Cold-worked steel rods and discs have a smooth, polished finish. They also have consistent mechanical properties and highly accurate dimensions.
Certificates with a traceable lot number are available for these products. Download certificates from ORDER HISTORY after your order ships.
Hardened Undersized High-Speed M2 Tool Steel Rods
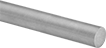
- Yield Strength: See table
- Hardness: Rockwell C60 (Very Hard)
These rods, also known as drill blanks, have an undersized diameter for machining your own drill bits. They're hardened for increased abrasion and impact resistance. M2 tool steel offers a nice balance of wear resistance and machinability. It has a high molybdenum content, which allows it to maintain sharp cutting edges even at elevated temperatures.
Dia. | Dia. Tolerance | Drill Bit Size | Lg. | Yield Strength | Mechanical Finish | Straightness Tolerance | Each | |
3mm | -0.0050mm to 0.0000mm | 3 mm | 1 7/8" | 261,000 psi | Precision Ground | 0.012" per ft. | 00000000 | 00000 |
3mm | -0.0050mm to 0.0000mm | 3 mm | 2 3/4" | Not Rated | Precision Ground | 0.012" per ft. | 00000000 | 0000 |
3mm | -0.0050mm to 0.0000mm | 3 mm | 4" | 261,000 psi | Precision Ground | 0.012" per ft. | 00000000 | 0000 |
Tight-Tolerance Multipurpose Oil-Hardening O1 Tool Steel Rods
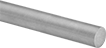
- Yield Strength: 50,000 psi
- Hardness: Rockwell B90 (Medium)
- Heat Treatable: Yes
- Maximum Hardness After Heat Treatment: Rockwell C65
- Fabrication: Hot Rolled
- Specifications Met: ASTM A681
Ready for turning in a lathe, these rods are precision ground to a tight diameter tolerance. They’re also known as drill rod. Often used for dies, punches, and gauges, O1 tool steel is an oil-hardening material that resists wear and abrasion. It can also be surface hardened with heat treating for added wear resistance. These rods have been manufactured to meet ASTM A681 standards for performance and quality.
Certificates with a traceable lot number are available for these products. Download certificates from ORDER HISTORY after your order ships.
3 ft. Lg. | |||||
---|---|---|---|---|---|
Dia. | Dia. Tolerance | Heat Treatment | Mechanical Finish | Each | |
3mm | -0.013mm to 0.013mm | Annealed (Softened) | Precision Ground | 00000000 | 00000 |
Tight-Tolerance Multipurpose Air-Hardening A2 Tool Steel Rods
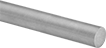
Precision ground and held to a strict straightness tolerance, these rods are ready for turning in your lathe. Also known as drill rod, this A2 tool steel is more wear resistant than O1 and keeps a sharper cutting edge. It’s air-hardening, so it doesn’t require baths or quenching after heat treatment. This tool steel is often used for punches, blades, and hammers. These rods have been manufactured to ASTM A681 standards for performance and quality.
Certificates with a traceable lot number are available for these products. Download certificates from ORDER HISTORY after your order ships.
- Yield Strength: 55,000 psi
- Hardness: See table
- Heat Treatable: Yes
- Max. Hardness After Heat Treatment: Rockwell C62
- Fabrication: Hot Rolled
- Specifications Met: ASTM A681
Multipurpose 304 Stainless Steel
From cookware to chemical-processing equipment, 304 stainless steel is a good all-around choice for a wide range of applications. It maintains its corrosion resistance in temperatures up to 1500° F.
Certificates with a traceable lot number are available for these products. Download certificates from ORDER HISTORY after your order ships.
Tight-Tolerance Multipurpose 304 Stainless Steel
This material has tighter tolerances than standard 304 stainless steel. From cookware to chemical-processing equipment, 304 stainless steel is a good all-around choice for a wide range of applications. It maintains its corrosion resistance in temperatures up to 1500° F.
Rods are precision ground and straightened, so they’re ready for turning in your lathe.
Steel that meets ASTM or SAE specifications complies with standards for materials.
Certificates with a traceable lot number are available for these products. Download certificates from ORDER HISTORY after your order ships.
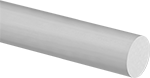
- Yield Strength: See Table
- Hardness: See Table
- Heat Treatment: Annealed (Softened)
- Heat Treatable: No
- Specifications Met: See Table
Easy-to-Machine 303 Stainless Steel
Widely used for fabricating fittings and fasteners, 303 stainless steel machines quickly without sticking to cutting tools. It maintains its corrosion resistance in temperatures up to 1500° F.
Certificates with a traceable lot number are available for these products. Download certificates from ORDER HISTORY after your order ships.
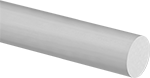
- Yield Strength: 25,000 psi
- Hardness:
Inch Sizes: Rockwell B77 (Medium)
Metric Sizes: Rockwell B85 (Medium) - Heat Treatment: Annealed (Softened)
- Heat Treatable: No
- Specifications Met:
Inch Sizes: ASTM A582
Metric Sizes: EN 10088-3
Tight-Tolerance Easy-to-Machine 303 Stainless Steel
This material has tighter tolerances than standard 303 stainless steel. Widely used for fabricating fittings and fasteners, 303 stainless steel machines quickly without sticking to cutting tools. It maintains its corrosion resistance in temperatures up to 1500° F.
Rods are precision ground and held to a strict straightness tolerance, so they are ready for turning in a lathe.
Certificates with a traceable lot number are available for these products. Download certificates from ORDER HISTORY after your order ships.
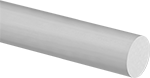
- Yield Strength: 35,000 psi
- Hardness: See Table
- Heat Treatment: Annealed (Softened)
- Heat Treatable: No
- Specifications Met: ASTM A582, SAE AMS5640
Hardened Tight-Tolerance High-Strength 17-4 PH Stainless Steel
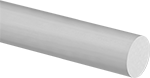
- Yield Strength: 170,000 psi
- Hardness: Rockwell C42 (Hard)
- Heat Treatment: Hardened
- Temper: H900
- Specifications Met: ASTM A564, SAE AMS5643
Hardened for improved strength and wear resistance, these rods are precision ground to a strict diameter tolerance. Use them for turning applications in your lathe. With a higher chromium content than 15-5 PH stainless steel, this high-strength 17-4 PH offers better corrosion resistance. It’s also known as 630 stainless steel. This material maintains its corrosion resistance in temperatures up to 1100° F.
Certificates with a traceable lot number are available for these products. Download certificates from ORDER HISTORY after your order ships.
Corrosion-Resistant 316 Stainless Steel
The addition of molybdenum gives 316 stainless steel excellent corrosion resistance. Use it in a variety of marine and chemical-processing applications. It maintains its corrosion resistance up to the maximum temperature.
If you don’t see the rod size you’re looking for, please specify a length under additional rod lengths.
Certificates with a traceable lot number are available for these products. Download certificates from ORDER HISTORY after your order ships.
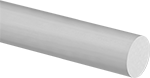
- Yield Strength:
Inch Sizes: 30,000 psi
Metric Sizes: 29,000 psi - Hardness:
Inch Sizes: Rockwell B75 (Medium)
Metric Sizes: Rockwell B80 (Medium) - Heat Treatment: Annealed (Softened)
- Heat Treatable: No
- Specifications Met:
Inch Sizes: ASTM A276
Tight-Tolerance Corrosion-Resistant 316 Stainless Steel
This material is precision ground to offer tighter tolerances than standard 316 stainless steel. The addition of molybdenum gives 316 stainless steel excellent corrosion resistance. Use it in a variety of marine and chemical-processing applications. It maintains its corrosion resistance in temperatures up to 1500° F.
Rods are held to a strict straightness tolerance, so they’re all set for turning in your lathe.
Certificates with a traceable lot number are available for these products. Download certificates from ORDER HISTORY after your order ships.
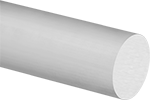
- Yield Strength: 30,000 psi
- Hardness: Rockwell B75 (Medium)
- Heat Treatment: Annealed (Softened)
- Heat Treatable: No
- Specifications Met: ASTM A276, SAE AMS5648
Ultra-Machinable 360 Brass Rods and Discs
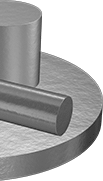
- Yield Strength:
Inch sizes: 15,000 psi
Metric sizes: 23,000 psi - Hardness: See table
- Temper:
Inch sizes: H02 (1/2 Hard)
Metric sizes: 1/2 Hard - Heat Treatable: No
- Specifications Met:
Inch sizes: ASTM B16
Metric sizes: European Standard EN 12164
With the highest lead content of all the brass alloys, 360 offers the best machinability. Often called free-machining and free-cutting brass, it stands up to high-speed drilling, milling, and tapping operations with minimal wear on your tools. It’s commonly used for gears, pinions, and lock components.
Certificates with a traceable lot number are available for these products. Download certificates from ORDER HISTORY after your order ships.
1 m Lg. | ||||
---|---|---|---|---|
Dia., mm | Dia. Tolerance Range, mm | Hardness | Each | |
3 | -0.05 to 0.05 | Rockwell B75 (Medium) | 0000000 | 00000 |
Ultra-Formable 260 Brass Rods
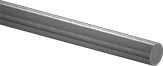
- Yield Strength:
Inch sizes: Not Rated
Metric sizes: 9,000 psi - Hardness: Not Rated
- Temper: H01 (1/4 Hard)
- Heat Treatable: No
- Specifications Met: ASTM B134
The most formable brass we offer, 260 offers better weldability than 300 series brass but it’s not as machinable. Sometimes called cartridge brass, it's commonly used for ammunition casings, radiator components, and decorative door hardware.
300 mm Lg. | ||||
---|---|---|---|---|
Dia., mm | Dia. Tolerance Range, mm | Pkg. Qty. | Pkg. | |
3 | -0.051 to 0.051 | 3 | 00000000 | 00000 |
Easy-to-Machine Architectural 385 Brass Rods
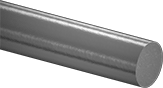
- Yield Strength:
Inch sizes: 16,000 psi
Metric sizes: 21,000 psi - Hardness:
Inch sizes: Rockwell B40 (Soft)
Metric sizes: Rockwell B55 (Soft) - Temper:
Inch sizes: M30
Metric sizes: Not Rated - Heat Treatable: No
- Specifications Met:
Inch sizes: ASTM B455
Metric Sizes: European Standard EN 12164
Often called architectural bronze, 385 brass is easy to machine and has excellent formability when heated. It is typically used for handrails, ornamental trim, and hardware, such as hinges and lock bodies.
Certificates with a traceable lot number are available for these products. Download certificates from ORDER HISTORY after your order ships.
1 m Lg. | ||||
---|---|---|---|---|
Dia., mm | Dia. Tolerance Range, mm | Straightness Tolerance | Each | |
3 | -0.05 | Not Rated | 0000000 | 00000 |
Multipurpose 110 Copper Rods and Discs
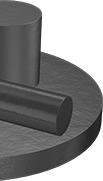
- Yield Strength:
Inch sizes: Not Rated
Metric sizes: 17,000 psi - Hardness:
Inch sizes: Rockwell F65 (Soft)
Metric sizes: Brinell 35 (Soft) - Temper:
6" dia. rods: M30
All other inch sizes: H04 (Full Hard)
Metric sizes: Not Rated - Heat Treatable: No
- Specifications Met:
Inch sizes: ASTM B187
Metric sizes: European Standard EN 13601
Offering high electrical conductivity and formability, 110 copper is 99.9% pure. Also known as ETP copper, it's often used in electrical applications, such as for bus bars and wire connectors, as well as for flashing, gaskets, and rivets.
Certificates with a traceable lot number are available for these products. Download certificates from ORDER HISTORY after your order ships.
1 m Lg. | |||
---|---|---|---|
Dia., mm | Dia. Tolerance Range , mm | Each | |
3 | -0.08 to 0 | 0000000 | 000000 |
Multipurpose Flame-Retardant Garolite G-10/FR4 Rods
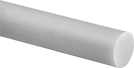
- Color: See Table
- Temperature Range: -100° F to 245° F
- Tensile Strength: 35,000-50,000 psi (Excellent)
- Impact Strength: 5.5-12 ft.-lbs./in. (Excellent)
- Hardness: Rockwell M115 (Extra Hard)
- For Use Outdoors: Yes
- Specifications Met: MIL-I-24768/27, UL 94 V-0
Made of a flame-retardant epoxy resin with fiberglass fabric reinforcement, these G-10/FR4 rods are a good all-around choice. They are strong, machinable, and electrically insulating. Garolite G-10/FR4 is also called epoxy-grade industrial laminate and phenolic.