About Gears
More
MXL Series Lightweight Timing Belt Pulleys
Made from polycarbonate, these pulleys are useful in applications with weight constraints. All are MXL series (miniature extra light) and have trapezoidal teeth. The teeth match up with the grooves along the inside diameter of a timing belt in order to move components forward or backward. Select a pulley with a maximum belt width that’s the same or larger than your timing belt width.
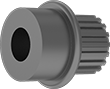
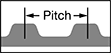
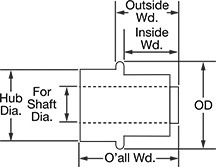
1 Flange | |||||||||||||
---|---|---|---|---|---|---|---|---|---|---|---|---|---|
OD | Number of Teeth | Pitch | For Shaft Dia. | Bore Type | Inside Wd. | Outside Wd. | Overall Wd. | Pitch Dia. | Fabrication | Material | Hub Dia. | Each | |
For 6 mm Max. Belt Wd. | |||||||||||||
69mm | 100 | 2.030mm | 8mm | Plain | 9.6mm | 11.2mm | 17.5mm | 64.7mm | Molded | Polycarbonate | 17.5mm | 0000000 | 000000 |
MXL Series Corrosion-Resistant Timing Belt Pulleys
Anodized aluminum has good corrosion resistance. Pulleys are MXL series (miniature extra light) and have trapezoidal teeth. The teeth match up with the grooves along the inside diameter of a timing belt in order to move components forward or backward. Select a pulley with a maximum belt width that’s the same or larger than your timing belt width.
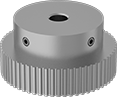
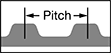
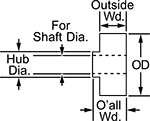
OD | Number of Teeth | Pitch | For Shaft Dia. | Bore Type | Outside Wd. | Overall Wd. | Pitch Dia. | Fabrication | Material | Hub Dia. | Each | |
For 6 mm Max. Belt Wd. | ||||||||||||
---|---|---|---|---|---|---|---|---|---|---|---|---|
64.2mm | 100 | 2.030mm | 8mm | Finished | 9.5mm | 19.1mm | 64.7mm | Machined | Anodized Aluminum | 38.1mm | 00000000 | 000000 |
For 9 mm Max. Belt Wd. | ||||||||||||
64.2mm | 100 | 2.030mm | 8mm | Finished | 12.7mm | 22.2mm | 64.7mm | Machined | Anodized Aluminum | 38.1mm | 00000000 | 00000 |
High-Strength GT Timing Belt Pulleys
For higher speed or higher torque applications, these GT series timing belt pulleys provide a more precise fit than HTD pulleys. Use them where accuracy is critical, such as in storage and retrieval systems or in robotics. Similar to HTD timing belt pulleys, their teeth are curved for high strength. The curved teeth create positive grip engagement with timing belts, so these pulleys do not require re-tensioning—unlike drives using V-belts or sheaves. And unlike chain drives, there’s no metal-on-metal contact, so these pulleys don’t require lubrication.
Anodized aluminum pulleys are lightweight and resist corrosion. They have a finished bore and come with set screws for mounting on shafts.
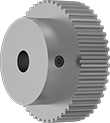
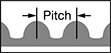
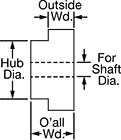
Number of Teeth | Pitch, mm | For Shaft Diameter | Bore Type | Outside Width, mm | Overall Width, mm | Pitch Diameter, mm | Fabrication | Material | Hub Diameter, mm | Each | |
For 6 mm Maximum Belt Width | |||||||||||
---|---|---|---|---|---|---|---|---|---|---|---|
100 | 2 | 5/16" | Finished | 9.65 | 19.05 | 63.652 | Machined | Anodized Aluminum | 38.1 | 00000000 | 000000 |
For 9 mm Maximum Belt Width | |||||||||||
100 | 3 | 5/16" | Finished | 12.7 | 22.26 | 95.504 | Machined | Anodized Aluminum | 31.75 | 0000000 | 00000 |
Metal Gears and Gear Racks—20° Pressure Angle
The current industry standard, these 20° pressure angle gears have thicker, stronger teeth than 14½° pressure angle gears. Compared to plastic gears and racks, they’re better for high-load, high-speed, and heavy duty applications. Also known as spur gears.
Combine gears with different numbers of teeth to change speed and torque in your assembly. Combine a gear and rack to convert rotary motion into linear motion. To minimize your footprint, mount one or more standard gears inside of an internal gear.
For components to mesh correctly, they must have the same pressure angle and pitch/module.
Carbon steel components have hard, strong, and wear-resistant teeth, although they will rust when exposed to moisture and corrosive chemicals. They're best for high-torque machines, like lifting equipment, and heavy duty applications, such as rock crushing. Gears with teeth that are not hardened can be hardened to fit your application.
Stainless steel gears and racks resist rust in damp and wet environments, so they're commonly used in food-processing plants and other areas with frequent cleaning. Gears with a clamping bore have a built-in clamp that securely grips shafts without marring them. Use the included clamping screw to tighten or loosen the grip.
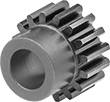
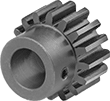
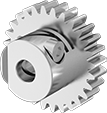
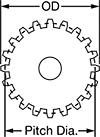

Hub | ||||||||||||||
---|---|---|---|---|---|---|---|---|---|---|---|---|---|---|
Module | Number of Teeth | Gear Pitch Dia., mm | OD, mm | Face Wd., mm | Overall Wd., mm | For Shaft Dia., mm | Material | Teeth Heat Treatment | Dia., mm | Wd., mm | Set Screw Thread Size | Clamping Screw Thread Size | Each | |
Round Bore | ||||||||||||||
1.5 | 100 | 150 | 153 | 15 | 29 | 15 | 303 Stainless Steel | Not Hardened | 80 | 14 | __ | __ | 00000000 | 0000000 |
Round Bore with Set Screw | ||||||||||||||
0.5 | 100 | 50 | 51 | 5 | 12 | 8 | Black-Oxide 1045 Carbon Steel | Not Hardened | 28 | 7 | M5 | __ | 00000000 | 00000 |
Clamping Bore with Clamping Screw | ||||||||||||||
1 | 100 | 100 | 102 | 6 | 20 | 10 | 303 Stainless Steel | Not Hardened | 24 | 14 | __ | M4 | 0000000 | 000000 |
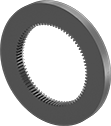
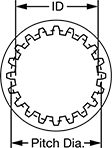
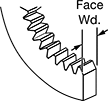
Module | Number of Teeth | Gear Pitch Dia., mm | OD, mm | ID, mm | Face Wd. | Material | Teeth Heat Treatment | Each | |
0.5 | 100 | 50 | 70 | 49 | 5mm | Black-Oxide 1045 Carbon Steel | Not Hardened | 0000000 | 000000 |
1 | 100 | 100 | 130 | 98 | 10mm | Black-Oxide 1045 Carbon Steel | Not Hardened | 0000000 | 000000 |
1.5 | 100 | 150 | 190 | 147 | 15mm | Black-Oxide 1045 Carbon Steel | Not Hardened | 0000000 | 000000 |
2 | 100 | 200 | 250 | 196 | 20mm | Black-Oxide 1045 Carbon Steel | Not Hardened | 0000000 | 000000 |
Metal Worms and Worm Gears
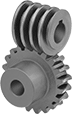
Worm gears use screw threads to make large reductions to shaft speed while transmitting motion at a right angle. They transmit motion from worm to gear and cannot be reversed. For gears and worms to mesh correctly, they must have the same pressure angle, pitch/module, number of thread starts, and thread direction. These worms are compatible with plastic worm gears.
Speed ratio is the ratio by which output shaft speed is reduced. As speed decreases, torque increases.
Cast iron gears are strong and durable.
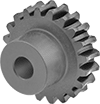
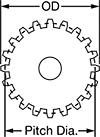
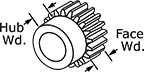
Hub | |||||||||||||||||
---|---|---|---|---|---|---|---|---|---|---|---|---|---|---|---|---|---|
Gear Pitch | Speed Ratio | Number of Teeth | Pressure Angle | Gear Pitch Dia. | For Number of Thread Starts | OD | Face Wd. | Overall Wd. | For Shaft Dia. | Dia. | Wd. | Material | For Thread Direction | Teeth Heat Treatment | Teeth Fabrication | Each | |
Round Bore—Cast Iron | |||||||||||||||||
10 | 100:1 | 100 | 14 1/2° | 10" | 1 | 10.22" | 5/8" | 1.375" | 3/4" | 2.5" | 0.75" | Cast Iron | Right Hand | Not Hardened | Not Ground | 000000000 | 0000000 |
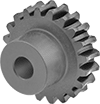
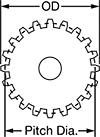
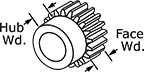
Hub | |||||||||||||||||
---|---|---|---|---|---|---|---|---|---|---|---|---|---|---|---|---|---|
Module | Speed Ratio | Number of Teeth | Pressure Angle | Gear Pitch Dia., mm | For Number of Thread Starts | OD, mm | Face Wd., mm | Overall Wd., mm | For Shaft Dia., mm | Dia., mm | Wd., mm | Material | For Thread Direction | Teeth Heat Treatment | Teeth Fabrication | Each | |
Round Bore—Cast Iron | |||||||||||||||||
1 | 100:1 | 100 | 20° | 100 | 1 | 103 | 10 | 20 | 10 | 40 | 10 | Cast Iron | Right Hand | Not Hardened | Not Ground | 000000000 | 000000 |
Plastic Gears and Gear Racks—20° Pressure Angle
The current industry standard, these 20° pressure angle gears have thicker, stronger teeth than 14½° pressure angle gears. Made of plastic, they run quieter than metal gears and have good corrosion and chemical resistance. They’re also known as spur gears.
Combine gears with different numbers of teeth to change speed and torque in your assembly. Combine a gear and rack to convert rotary motion into linear motion.
For components to mesh correctly, they must have the same pressure angle and pitch/module.
Nylon gears can be operated without lubrication, so they’re commonly used in food-processing machines.
Metal Ratcheting Gears
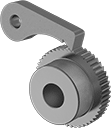
Compared to plastic gears, these metal ratcheting gears are better for high-load, high-speed, and heavy duty applications. Used to prevent unwanted motion in jacks, tie downs, clutches, and winches, ratchet gears have sloped teeth that allow motion in one direction and prevent it in the other.
Gears with hardened teeth are more wear resistant than gears with teeth that are not hardened.
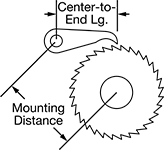
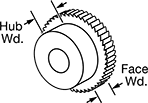
Hub | |||||||||||
---|---|---|---|---|---|---|---|---|---|---|---|
Face Wd. | Number of Teeth | OD | For Shaft Dia. | Mounting Distance | Material | Teeth Heat Treatment | Overall Wd. | Dia. | Wd. | Each | |
Round Bore | |||||||||||
6mm | 100 | 66.6mm | 12mm | 44.1mm | 1045 Carbon Steel | Hardened | 6 mm | __ | __ | 0000000 | 000000 |
6mm | 100 | 66.6mm | 12mm | 44.1mm | 1045 Carbon Steel | Hardened | 16 mm | 40 mm | 10 mm | 0000000 | 00000 |
12mm | 100 | 100mm | 15mm | 62.2mm | 1045 Carbon Steel | Hardened | 12 mm | __ | __ | 0000000 | 00000 |
12mm | 100 | 100mm | 15mm | 62.2mm | 1045 Carbon Steel | Hardened | 24 mm | 50 mm | 12 mm | 0000000 | 00000 |